Volume 28, No.2 Pages 124 - 128
1. 最近の研究から/FROM LATEST RESEARCH
長期利用課題報告2
高強度金属材料の超高サイクル疲労における内部微小き裂の発生・進展挙動
Initiation and Propagation Behaviors of Small Internal Cracks in High-Strength Metals in Very High Cycle Fatigue Regime
[1]北海道大学 大学院工学研究院 機械・宇宙航空工学部門 Division of Mechanical and Aerospace Engineering, Hokkaido University、[2]北海道大学 大学院工学院 機械宇宙工学専攻 Division of Mechanical and Space Engineering, Hokkaido University、[3](公財)高輝度光科学研究センター 放射光利用研究基盤センター 散乱・イメージング推進室 Scattering and Imaging Division, Center for Synchrotron Radiation Research, JASRI
- Abstract
- 本研究は、高強度金属材料における超高サイクル疲労の支配因子である材料内部に発生する微小き裂の非破壊観察を目的とした。ビームラインBL20XUに設置できるその場疲労試験システムを開発し、2相チタン合金((α+β)型Ti-6Al-4V)、単相チタン合金(β型Ti-22V-4Al)および超高張力鋼(SUS630)を対象として、疲労試験とマルチスケールX線CT(マイクロCTおよびナノCT)による撮像を繰り返した。その結果、3種類の材料すべてに関して、数~数十µmの内部微小き裂を検出し、その発生位置の特定や進展速度の計測に成功した。特にチタン合金では、き裂の発生・進展過程と基地組織との関係を明らかにした。超高張力鋼では、X線透過率の制限によりマイクロCTのみによる観察を行ったが、き裂が材料内部の数µmの非金属介在物から発生し、負荷方向に対して垂直に開口形で進展する様子を明瞭に捉えることができた。

1. はじめに
超高張力鋼やチタン合金等の高強度金属において、107回程度以上の繰返し数で疲労強度が大幅に低下する特異現象、いわゆる超高サイクル疲労が近年広く知られるようになった[1, 2][1] B. Pyttel, D. Schwerdt and C. Berger: Int J Fatigue 33 (2011) 49-58.
[2] T. Sakai: Fatigue Fract Eng Mater Struct 46 (2023) 1217-1255.。これは材料内部を起点とするき裂の発生・進展により生じる。しかし、X線や超音波を用いた通常の非破壊検査技術では、超高サイクル疲労で問題となる数~数十µmの大きさの内部き裂の検出は極めて困難であり、超高サイクル疲労強度評価法は確立していない。近年では機械の高速化・高経年化が年々加速しており、超高サイクル領域における材料や部品の健全性確保は重要な検討課題である。
以上を背景として、本研究ではSPring-8のビームラインBL20XUにおけるマルチスケールX線CT(マイクロCTおよびナノCT)を活用し、200 nmを超える空間分解能で内部微小き裂の発生・進展過程を非破壊で観察した。ビームライン上での疲労試験を可能とするその場(in-situ)疲労試験システムを開発し、材料内に生じたき裂を確認しつつ、その進展や開閉口挙動をリアルタイムで計測する技術を構築した。そして、このシステムを用いて繰返し負荷下で高強度金属材料に生じた微小き裂の進展挙動を観察した。対象材料は、実用上重要であり、かつ内部破壊を生じる高強度金属材料の代表として、(α+β)チタン合金、βチタン合金、析出硬化型マルテンサイト系ステンレス鋼の3種類である。具体的には、(α+β)型Ti-6Al-4V、β型Ti-22V-4Al、SUS630をそれぞれ2相チタン合金、単相チタン合金、超高張力鋼の代表として選定した。
2. その場疲労試験システムの開発
2.1. In-situ高速疲労試験機
開発したin-situ高速疲労試験システム[3, 4][3] G. Xue, T. Nakamura, N. Fujimura, K. Takahashi, H. Oguma et al.: Eng Fract Mech 263 (2022) 108308.
[4] G. Xue, T. Nakamura, N. Fujimura, K. Takahashi, H. Oguma et al.: Int J Fatigue 170 (2023) 107571.を図1に示す。本機は、試験片に引張・圧縮の軸荷重を与えるピエゾアクチュエータ、ロードセル、X線を透過させるためのアクリル製透過管などからなり、BL20XUの第1ハッチ回転台の上に設置できるよう軽量(2.6 kg)に設計された。これによって、試験片を取り外さずにビームライン上で疲労試験とCT観察を繰り返すことができる。定格容量は±1 kNであり、デジタルコントローラ(島津、4830)を用いたPIDフィードバック制御により、静荷重~300 Hz程度までの任意波形の荷重を±1%以上の精度で試験片に負荷することができる。なお、試験中のピエゾアクチュエータの過熱を防ぐため、装置上部から圧縮空気による冷却を行っている。試験機のアライメントは、アクリル製透過管とその上部にある試験機ハウジングの間にシムを挟むことで調整した。本研究では、周方向に4枚のひずみゲージを貼った直径3 mmの調芯用試験片を試験機に取付け、生じる曲げひずみを10 µST以下に抑えた。これによって、信頼性の高い疲労試験を実施できる。
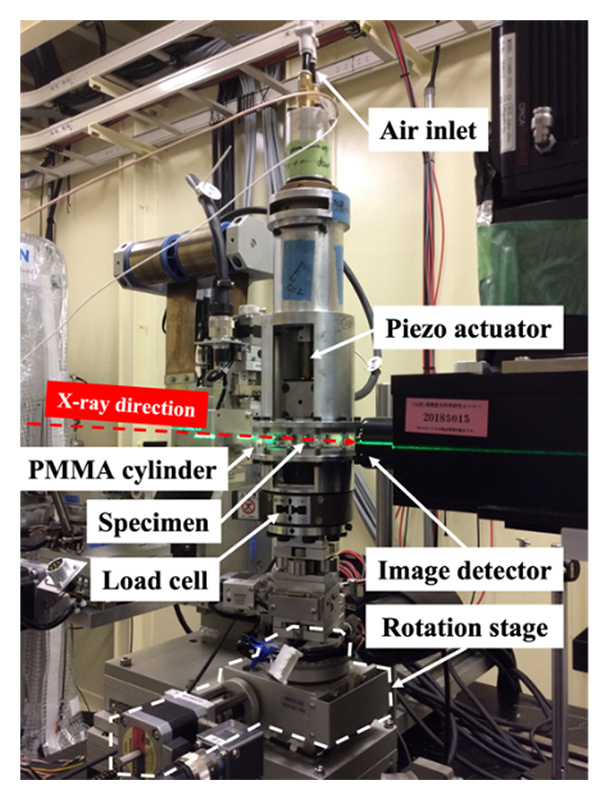
図1 in-situ高速疲労試験システム。
2.2. X線CT用小径疲労試験片
マルチスケールX線CTで材料内部に発生したき裂を捉えるためには、材料を透過したX線が十分な強度を保っている必要があり、明瞭なCT像を得るためには約20%程度のX線透過率を得ることが望ましい。例えば、X線エネルギーを30.0 keVとした場合、本研究で用いるチタン合金においてこの透過率を確保するためには試験片直径を0.6~0.7 mm程度にする必要がある。また、チタン合金に比べ密度の高い超高張力鋼SUS630において同程度の透過率を得るには、試験片直径をさらに細くしなければならない。一方、試験片は切削によって製作するため、あまりにも細い試験片を精度よく加工することは難しい。疲労試験機にセッティングする際の取扱いや試験実施の観点からも、試験片直径はできるだけ太い方が望ましい。そこで本研究では、これらのバランスを考慮して、X線エネルギーと各供試材の試験片直径を表1のように設定した。なお、SUS630に適用するX線エネルギー37.7 keVはBL20XUで通常設定できる最大のエネルギー値である。このように高輝度・高エネルギーの放射光X線を用いた場合でも、鉄鋼材料では十分な透過率を確保することは難しく、チタン合金に比べ観察の難易度が高い。
表1 各供試材の試験片におけるX線エネルギー、試験片直径、X線透過率。
Material | X-ray energy [keV] |
Specimen diameter [mm] |
X-ray transmittance [%] |
Ti-6Al-4V | 30.0 | 0.7 | 21.4 |
Ti-22V-4Al | 30.0 | 0.6 | 23.3 |
SUS630 | 37.7 | 0.6 | 11.4 |
本研究では、表1に示した小径の平行部を持つ疲労試験部とこれを試験機側で把持する部分(把持部)を別々の部品で構成する組立式の砂時計型試験片を開発した[3-5][3] G. Xue, T. Nakamura, N. Fujimura, K. Takahashi, H. Oguma et al.: Eng Fract Mech 263 (2022) 108308.
[4] G. Xue, T. Nakamura, N. Fujimura, K. Takahashi, H. Oguma et al.: Int J Fatigue 170 (2023) 107571.
[5] G. Xue Y. Tomoda, T. Nakamura, N. Fujimura, K. Takahashi et al.: Fatigue Fract Eng Mater Struct 45 (2022) 2693-2702.。本試験片では、組立時、専用の組立治具を用いて試験部と把持部のアライメントを整えた。これによって、軸方向に精度よく繰返し荷重を負荷することができる。
2.3. 放射光マルチスケールX線CT
BL20XUでは、比較的広い視野(約1 × 1 mm2)で1 µm程度の空間分解能を有する投影型(マイクロCT)と視野は狭い(約0.06 × 0.06 mm2)が200 nmを超える空間分解能を有する位相コントラスト結像型CT(ナノCT)を随時切り替えて使用することができる[6, 7][6] A. Takeuchi and Y. Suzuki: Microscopy 69 (2020) 259-279.
[7] A. Takeuchi, K. Uesugi, M. Uesugi, F. Yoshinaka and T. Nakamura : Microsc Microanal 24 (2018) 106-107.。なお、CT撮像におけるボクセルサイズは、マイクロCT:0.5 µm/voxel、ナノCT:0.03~0.08 µm/voxelである。本研究では、主にマイクロCTで試験片全体を調べ、き裂が検出された場合は、その詳細をナノCTで観察した。ただし、SUS630についてはマイクロCTによる観察のみとした。
3. 高強度金属における微小き裂の発生・進展挙動
3.1. (α+β)チタン合金[5, 8][5] G. Xue Y. Tomoda, T. Nakamura, N. Fujimura, K. Takahashi et al.: Fatigue Fract Eng Mater Struct 45 (2022) 2693-2702.
[8] F. Yoshinaka, T. Nakamura, H. Oguma, N. Fujimura, A. Takeuchi et al.: Fatigue Fract Eng Mater Struct (2023) 13957.
図2にマイクロCTで得られた内部疲労き裂の画像を示す。これは最大応力σmax = 650 MPaの繰返し負荷を応力比(=最小応力/最大応力)R = 0.1で加えた結果であり、負荷の繰返し数N = 1.10 × 107回からN = 1.12 × 107回の間のき裂進展を表している。本供試材はα相とα+β相の2相組織から成るが、図中の暗い領域がα相、明るい領域がα+β相であり、き裂が組織のどこをどのように進展しているかが捉えられている。特に、図2(b)では、図2(a)のき裂の右側先端がα相の中を荷重軸に対して斜めに進展した様子が確認される。図3はこの進展の様子をナノCTで観察したものである。組織とき裂の対応がさらに明瞭に観察され、き裂は荷重軸方向に対してほぼ45度の角度でα相内を進展し(A部)、α+β相との粒界で止まったことが示されている。き裂は最大せん断応力方向に優先的に進展していることから、α相のすべりがき裂進展の駆動力になったと判断される。
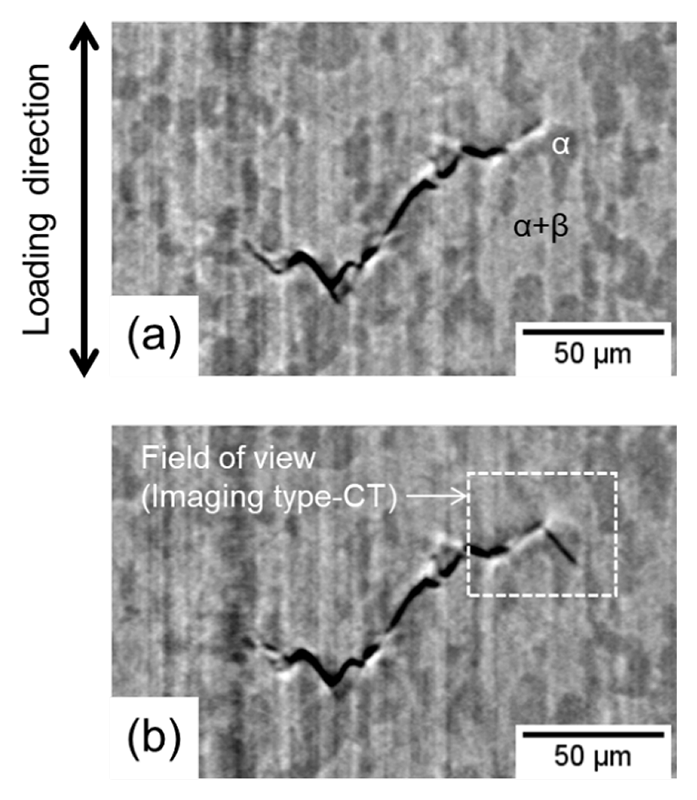
図2 (α+β)チタン合金に観察された内部き裂(マイクロCT)、(a)N = 1.10 × 107、(b)N = 1.12 × 107。
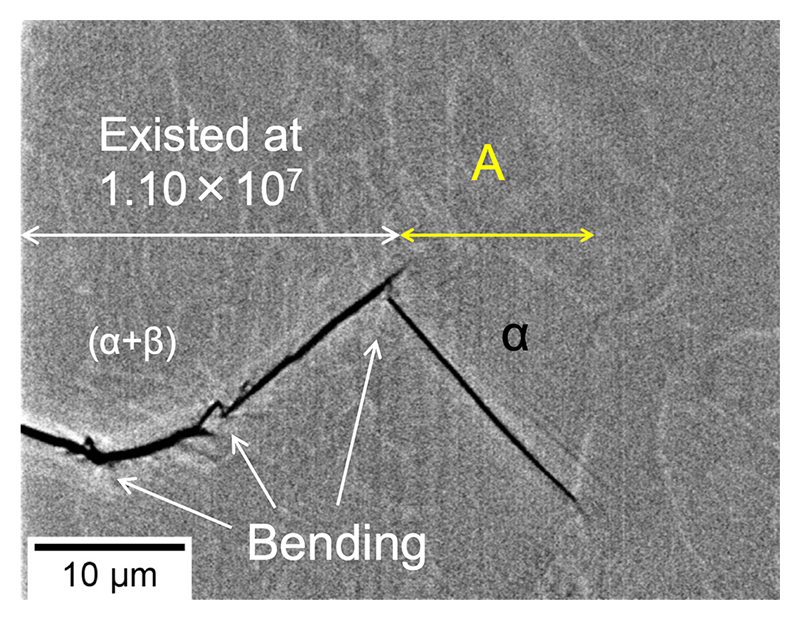
図3 図2中白点線枠内の拡大図(ナノCT)、A部はき裂進展領域。
一方、このような微小き裂は試験片内にひとつではなく、極めて多数形成されていたこともマイクロCTによる観察を通じて明らかとなった。図4に検査体積(φ0.7 × 1.9 mm)内に発生した微小き裂の空間分布を示す。同図中の数字はき裂発生の順番を示している。この試験片には合計46個のき裂が発生しており、そのうち45個が内部き裂であった。なお、印は1個のみ観察された表面き裂の発生位置である。一つの試験片にこのような多数の内部き裂が低応力域で発生していることは、これまでの金属疲労の常識と異なる結果であり、SPring-8を用いた非破壊観察により初めて明らかにされた知見である。(α+β)チタン合金の疲労強度は超高サイクル域で急激に低下するが、この現象はこのような多数のき裂の発生と競合によってもたらされた可能性がある。この結果はき裂発生寿命や発生位置が本質的に統計量として捉えられるべきものであることを示している[8, 9][8] F. Yoshinaka, T. Nakamura, H. Oguma, N. Fujimura, A. Takeuchi et al.: Fatigue Fract Eng Mater Struct (2023) 13957.
[9] 森下弘法、中村孝、藤村奈央、髙橋航圭:材料71 (2022) 997-1004.。
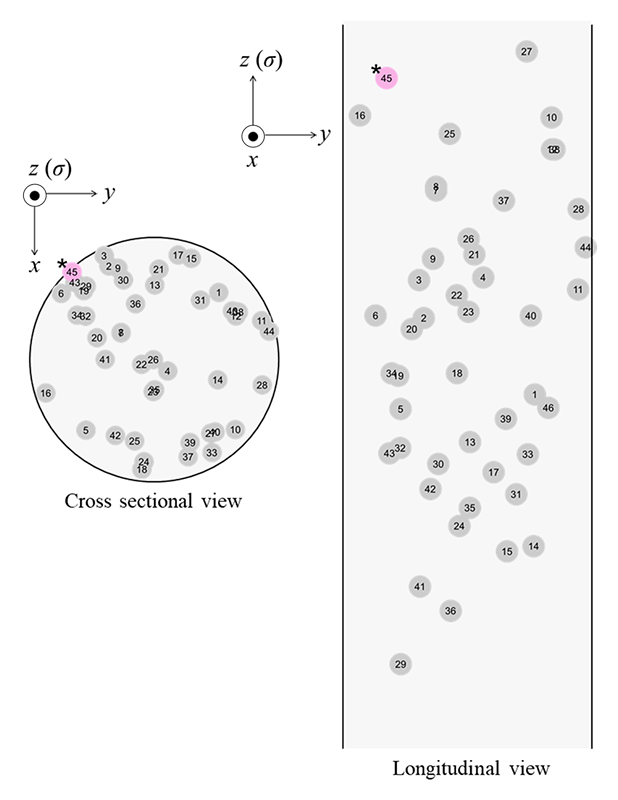
図4 (α+β)チタン合金の試験片内に観察されたき裂の空間分布(R = 0.1、σmax = 750 MPa)。
3.2. βチタン合金[3, 4][3] G. Xue, T. Nakamura, N. Fujimura, K. Takahashi, H. Oguma et al.: Eng Fract Mech 263 (2022) 108308.
[4] G. Xue, T. Nakamura, N. Fujimura, K. Takahashi, H. Oguma et al.: Int J Fatigue 170 (2023) 107571.
図5に最大応力σmax = 1050 MPaの繰返し負荷を応力比R = 0.1で加えた際にマイクロCTで観察した内部き裂の進展過程を示す。同図は荷重軸と垂直方向に投影したき裂の画像であり、繰返し数N = 4.00 × 105回で初めて検出されたき裂が進展を続け、N = 5.21 × 105回で表面に達して表面き裂に遷移した様子が捉えられている。この一連の画像を解析することで、本材料における内部き裂の進展速度を明らかにすることができた[4][4] G. Xue, T. Nakamura, N. Fujimura, K. Takahashi, H. Oguma et al.: Int J Fatigue 170 (2023) 107571.。本供試材は時効処理されたβの単相組織から成るが、ナノCTを用いた観察から、き裂の発生および初期進展は時効β粒において荷重軸方向とほぼ45度の角度で生じたことがわかっている。これは(α+β)チタン合金における内部き裂がα相のすべりにより発生した現象と類似している。しかし、βチタン合金では(α+β)チタン合金のように多数の内部き裂は検出されず、試験片はひとつのき裂の進展により破断に至った。このことは、超高サイクル疲労特性が基地組織の違いに著しく影響を受けることを示しており、今後の強度評価手法の構築にとって重要な知見が得られた。
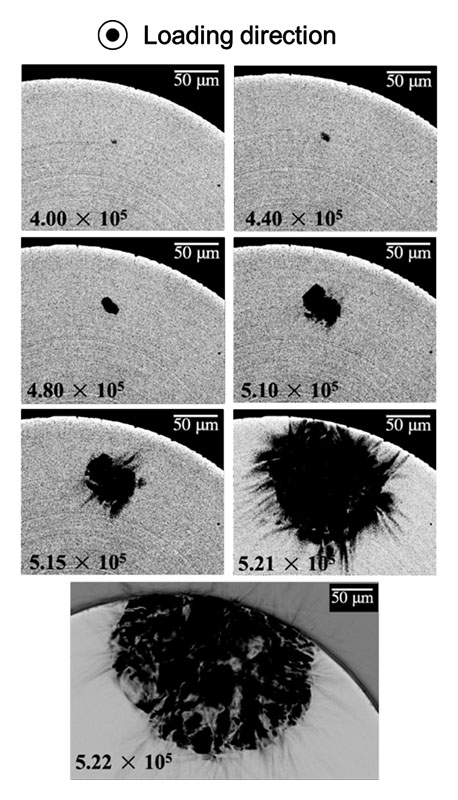
図5 βチタン合金に観察された内部き裂の進展挙動(R = 0.1、σmax = 1050 MPa)。
3.3. 析出硬化型マルテンサイト系ステンレス鋼[10][10] V. Verma, G. Xue, G. Igarashi, N. Fujimura, T. Nakamura et al.: Proceedings of the 35th Symposium on Fatigue (2022) 101-104.
図6に最大応力σmax = 675 MPaの繰返し負荷を応力比R = -1で加えた際にマイクロCTで検出された内部き裂の挙動を示す。同図は内部き裂の仮想断面であり、上下方向が荷重軸方向である。内部き裂は試験片内の数µm程度の非金属介在物から発生し、発生直後から荷重軸方向と垂直に開口形の進展を生じたことが明らかとなった。この点は結晶粒の粒内すべりを起点とする(α+β)チタン合金やβチタン合金と大きく異なり、内部き裂の進展挙動に基地組織が強く影響することを示している。本供試材においても図6の情報から内部き裂の進展速度を明らかにすることができた[10][10] V. Verma, G. Xue, G. Igarashi, N. Fujimura, T. Nakamura et al.: Proceedings of the 35th Symposium on Fatigue (2022) 101-104.。超高張力鋼の内部き裂を検出した例は、著者らが知る限り国内外で発表されておらず、本分野の発展に寄与する成果が得られた。
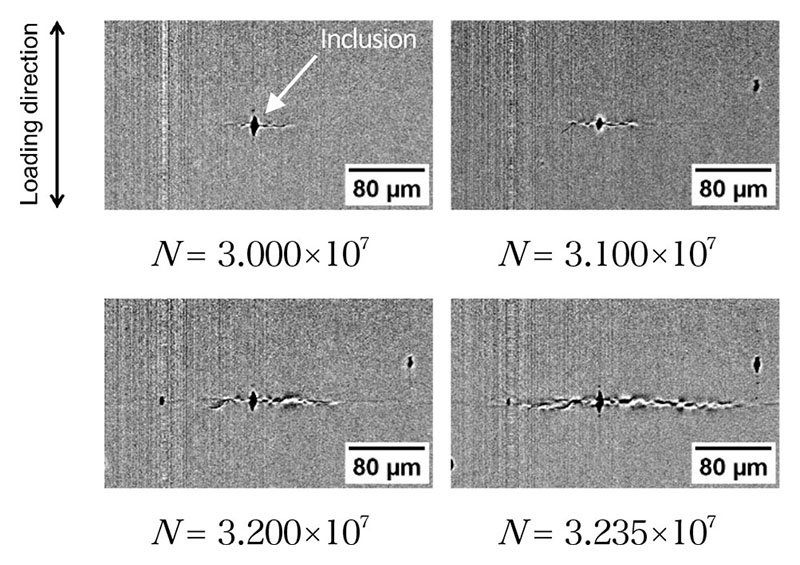
図6 析出硬化型マルテンサイト系ステンレス鋼に観察された内部き裂の進展挙動(R = -1、σmax = 675 MPa)。
4. おわりに
本研究では、in-situ高速疲労試験システムを開発し、SPring-8のBL20XUにおけるマルチスケールX線CTを用いて、(α+β)チタン合金、βチタン合金および超高張力鋼における内部微小疲労き裂の検出に成功した。チタン合金に関しては、疲労き裂と基地組織を同時に観察することで、微小き裂の発生位置や進展速度と組織との関係を明らかにした。超高張力鋼では、材料内部の非金属介在物からき裂が発生し、これが荷重軸方向に垂直に進展する様子を捉えることができた。一方、超高張力鋼についてはX線透過率の制限によりマイクロCTのみによる観察となり、き裂と材料組織との関係は明らかになっていない。そのため、今後は、ナノCTを鋼系材料に適用する技術開発が極めて重要となる。また、(α+β)チタン合金の結果より、き裂の発生寿命や発生位置は統計量として捉えられるべきものであることが示されたことから、き裂の発生・進展・停留などの情報を基に、超高サイクル疲労過程を推定するモデルの開発に取り組む[9][9] 森下弘法、中村孝、藤村奈央、髙橋航圭:材料71 (2022) 997-1004.。このモデルが構築されれば、材料の疲労寿命推定に適用できることが期待される。
参考文献
[1] B. Pyttel, D. Schwerdt and C. Berger: Int J Fatigue 33 (2011) 49-58.
[2] T. Sakai: Fatigue Fract Eng Mater Struct 46 (2023) 1217-1255.
[3] G. Xue, T. Nakamura, N. Fujimura, K. Takahashi, H. Oguma et al.: Eng Fract Mech 263 (2022) 108308.
[4] G. Xue, T. Nakamura, N. Fujimura, K. Takahashi, H. Oguma et al.: Int J Fatigue 170 (2023) 107571.
[5] G. Xue Y. Tomoda, T. Nakamura, N. Fujimura, K. Takahashi et al.: Fatigue Fract Eng Mater Struct 45 (2022) 2693-2702.
[6] A. Takeuchi and Y. Suzuki: Microscopy 69 (2020) 259-279.
[7] A. Takeuchi, K. Uesugi, M. Uesugi, F. Yoshinaka and T. Nakamura : Microsc Microanal 24 (2018) 106-107.
[8] F. Yoshinaka, T. Nakamura, H. Oguma, N. Fujimura, A. Takeuchi et al.: Fatigue Fract Eng Mater Struct (2023) 13957.
[9] 森下弘法、中村孝、藤村奈央、髙橋航圭:材料71 (2022) 997-1004.
[10] V. Verma, G. Xue, G. Igarashi, N. Fujimura, T. Nakamura et al.: Proceedings of the 35th Symposium on Fatigue (2022) 101-104.
北海道大学 大学院工学研究院 機械・宇宙航空工学部門
〒060-8628 北海道札幌市北区北13条西8丁目
TEL : 011-706-6419
e-mail : nakamut@eng.hokudai.ac.jp
北海道大学 大学院工学研究院 機械・宇宙航空工学部門
〒060-8628 北海道札幌市北区北13条西8丁目
TEL : 011-706-6421
e-mail : fujimura@eng.hokudai.ac.jp
北海道大学 大学院工学院 機械宇宙工学専攻
〒060-8628 北海道札幌市北区北13条西8丁目
TEL : 011-706-6422
e-mail : setsu_xue@eis.hokudai.ac.jp
北海道大学 大学院工学研究院 機械・宇宙航空工学部門
〒060-8628 北海道札幌市北区北13条西8丁目
TEL : 011-706-6420
e-mail : ktakahashi@eng.hokudai.ac.jp
(公財)高輝度光科学研究センター
放射光利用研究基盤センター 散乱・イメージング推進室
〒679-5198 兵庫県佐用郡佐用町光都1-1-1
TEL : 0791-58-0833
e-mail : take@spring8.or.jp
(公財)高輝度光科学研究センター
放射光利用研究基盤センター 散乱・イメージング推進室
〒679-5198 兵庫県佐用郡佐用町光都1-1-1
TEL : 0791-58-0833
e-mail : uesugi@spring8.or.jp
(公財)高輝度光科学研究センター
放射光利用研究基盤センター 散乱・イメージング推進室
〒679-5198 兵庫県佐用郡佐用町光都1-1-1
TEL : 0791-58-0833
e-mail : ueken@spring8.or.jp