Volume 12, No.5 Pages 409 - 414
3. 利用者懇談会研究会報告/RESEARCH GROUP REPORT (SPring-8 USERS SOCIETY)
金属疲労損傷評価研究会
Research Group on Fatigue Damage Evaluation in Metals
1. 研究会設立の目的
金属材料の疲労現象が発見されて以来1世紀半以上が経過し、これまでに多くの研究が行われてきたが、今なお疲労を主因とした破壊事故が後を絶たない。その原因は、設計者、製造者、使用者の疲労現象に対する認識不足や不注意によることもあるが、疲労寿命が種々の因子の影響を受け、あまりにも複雑な現象であるために、実用機器の疲労寿命を十分な精度で予測することが困難な場合が多いことにも起因している。その解決のためには、疲労のメカニズムの解明とそれに基づく損傷評価法の開発が必要不可欠である。特に、新たな製品が開発された場合、経験に基づく設計や保守管理のみでは十分に安全性を確保できない場合があり、メカニズムに基づいて疲労寿命および疲労損傷評価を行うことが必要となる。
さて、金属疲労研究は、金属顕微鏡、電子顕微鏡、原子間力顕微鏡の開発などのように、新たな観察手法が開発されるごとに飛躍的に進歩してきた。本研究会の目的は、SPring-8の高輝度放射光を応用して、疲労研究のブレークスルーを図ることにあり、そのための共同研究を実施してきた。以下に、これまでに得られた成果を述べる。
鉄鋼材料は、室温・大気中において疲労限度を持ち、107回の繰返しに耐えることができれば、それ以上、振幅が一定の負荷を繰り返し続けても疲労破壊することはないものと考えられてきた。しかしながら、近年、高強度鋼において、108回以上の繰返し後に疲労破壊する場合のあることがわかってきた。このような超長寿命疲労では、材料内部に存在する介在物よりき裂が発生し破断に至ることが107回以前に疲労破壊する場合と決定的に異なっている。後者の場合、材料表面に発生したき裂が進展し破断に至る。材料内部にき裂が発生する場合、通常の顕微鏡によって、き裂の発生・成長過程の観察をすることは不可能であり、それが、このような疲労現象のメカニズム解明を困難にしている。そこで、本研究会では、SPring-8を利用したイメージング技術を用いて、内部き裂の発生に関する研究を開始した。
まず、内部き裂発生の基点となる介在物の検出可能性について検討した。測定には、快削鋼(SAE12L14、SAE1215)および機械構造用炭素鋼(S35C)を用いた。放射光によるCTイメージング像を図1に示す。撮影条件は、X線エネルギー25 keV、ズーミング管倍率80倍、試料カメラ間距離299 mmである。快削鋼の場合、試料の横断面図を示した図1(a)より、複数の円状の像が試験片内部に分布していることがわかる。これらの黒い円状の像は、鉄鋼材料内の密度の異なる金属組織であると考えられる。黒い円状の直径は、約7〜9 µm程度であった。
図1(a)の右側に示した三次元イメージでは、得られたCT像に二値化処理を施し、明暗を逆に表現した後、三次元イメージ化処理を施しており、図内の白色で表現されている部分は、横断面像では黒色の部分に相当する。また、試験片の輪郭(表面)に現れる明暗線は除去し、輪郭の概要をワイヤーフレームで示している。内部に母地と異なる組織が多数分布しており、試料長手方向に細長く伸びていることがわかる。また、切削時の塑性変形により曲がった試料先端の形状に応じて組織が曲がっていることが観察できる。一方、図1(b)に示した炭素鋼S35CのCT像では、内部にこのような像が現れていない。

図1 CTイメージング像
CTイメージングにおいて検出された組織を同定するために、エッチングによる金属組織観察およびEPMA(Electron Probe Micro-Analysis)による組織分析を行った。観察は試験片長手方向断面において行った。
図2は、エッチング前および3%ナイタールによるエッチング後の組織写真である。快削鋼の組織写真(図2(a))において、他の組織と比較して黒色に見える部分は介在物であると推定される。この介在物は、試験片長手方向に細長く伸びて分布している。炭素鋼の組織写真(図2(b))では、エッチング処理を施すことにより、フェライト・パーライト相の組織が現れている。この場合、黒色に見えるパーライト相が介在物と同様に試験片長手方向に伸びるように分布している。

図2 組織写真
快削鋼について、EPMAを用いて組織成分の分析を行った結果を図3に示す。この図では、元素の含有量が高い部分が明るい色調で表現されている。図より、S、Mn、Pbが多く存在していることがわかる。また、これらの成分は長手方向に細長い形状で分布している。

図3 元素分析
図1と図2を比較すると、CTイメージングでは、パーライト相は検出されず、MnS介在物を検出していることがわかる。
3-1. フレッティング疲労き裂
フレッティングとは、接触した面間において、微小なすべりの繰返しが起こる現象であり、この作用により、疲労強度が著しく低下することが知られており、フレッティング疲労と呼ばれている。実際にフレッティング疲労は、車軸、タービンなど、多くの機器・構造物において生じており、これらの健全性を確保する上で、そのメカニズム解明は重要な課題である。
発生直後のフレッティング疲労き裂は、複雑な形状をしており、その進展のメカニズム解明とき裂進展寿命を評価するためには、その形状を正確に測定することが必要である。
そこで、本研究会では、CTイメージングによってフレッティング疲労き裂の観察を行った。疲労試験装置の概略とCT観察用の試料採取場所を図4に示した。観察に用いた材料は、析出硬化型ステンレス鋼である。CT観察において、X線エネルギーは35 keVとした。

図4 フレッティング疲労き裂の観察
カメラ−試料間距離Lを160 mmおよび1,160 mmと変えて、試料の同じ箇所の測定を行った結果を図5および6に示す。本測定では、0°から180°までを2°刻みで透過像を撮影した。図5では三次元形状に再構成した像の、図4に示した接触面に平行な面における断面像を示している。また図6は、図5内の点線①における横断面像である。
図6より、フレッティング疲労特有である試験片表面に対して斜めにき裂が発生・成長する形態がわかる。また、図5および6より、カメラ−試料間距離Lを160 mmとした場合では、L = 1,160 mmとした場合と比較して、点線②で示したようなき裂形状が不明瞭な箇所があることがわかる。このように、カメラ−試料間距離が小さい場合には不鮮明であったき裂が、カメラ−試料間距離を大きくすると鮮明になるのは、放射光によるCTイメージングでは屈折コントラストと呼ばれる現象が存在するためであり、通常の吸収コントラストでは観察できない組織がこの現象を利用すると観察できるようになる。
図5(a)、(b)および(c)の像を得た試料表面の電子顕微鏡(SEM)画像を図5(d)に示した。SEM画像上のき裂が屈曲を示す位置および形状と同様の形状がCTにより得られていることがわかる。また、図5(d)中のき裂が屈曲を示す位置を拡大した画像が示すように、表面におけるき裂開口量は1 µm以下であり、微小な開口量のき裂でも検出できていることがわかる。

図5 屈折コントラストの影響
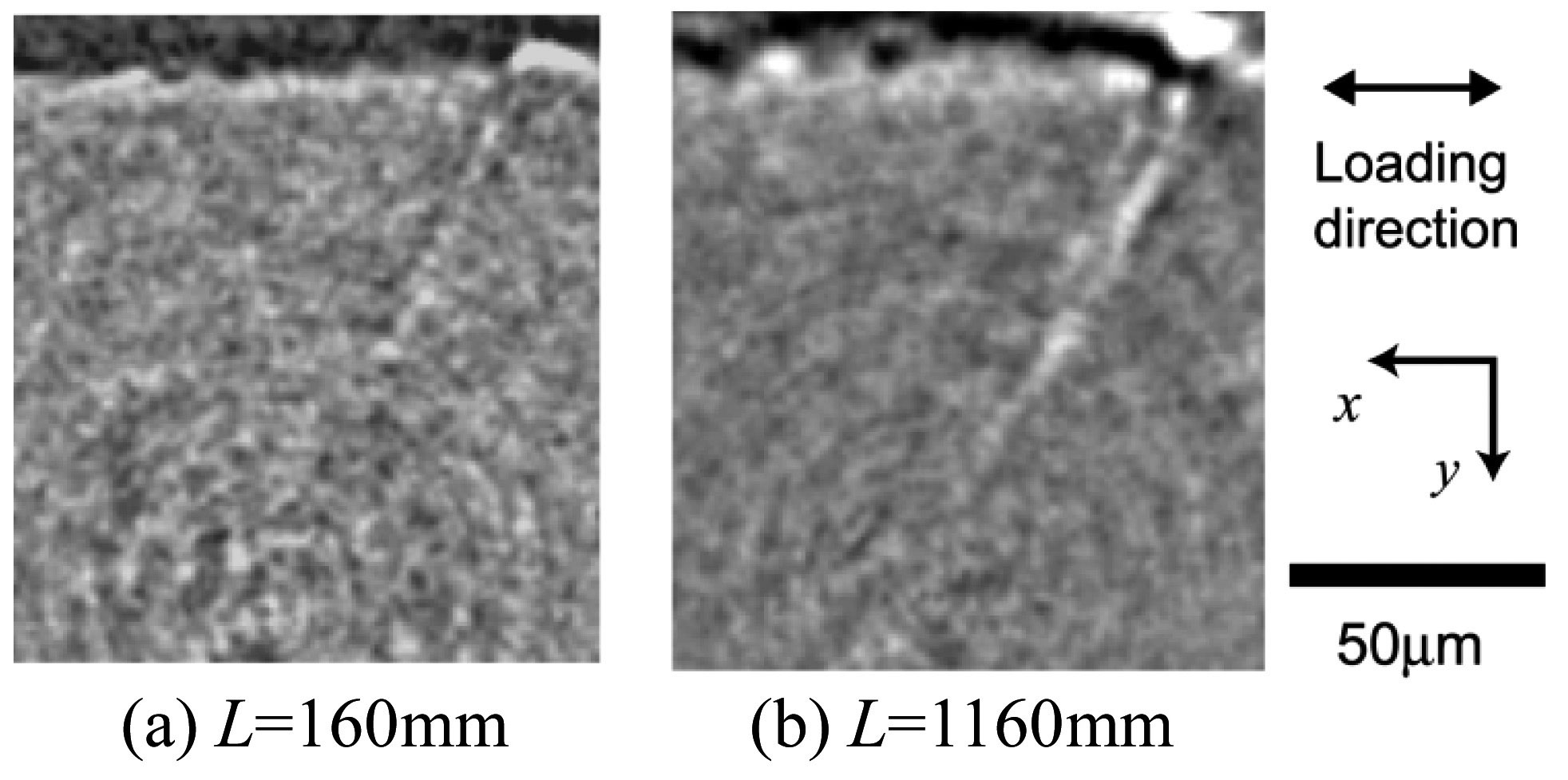
図6 屈折コントラストの影響
き裂の大きさおよび開口量が検出器のピクセルサイズよりも小さい場合、X線吸収線量の差による吸収コントラスト法のみでは、き裂近傍の吸収線量変化は1ピクセル内で生じ、き裂近傍の平均値しか観察されないため、透過像内のき裂によって生じる明度変化は小さくなる。さらに再構成における誤差が生じるためCT像上ではき裂によるコントラストは小さくなり、き裂による変化の検出が困難となる。一方、屈折コントラスト法を用いると、き裂や密度差の境界周辺部における屈折光のため、透過像におけるき裂像や境界周辺部の輪郭が太くなり、再構成画像においても開口量が微小なき裂によるコントラスト差の検出が可能となったものと考えられる。
次に、CTより得られた内部における観察結果と実際のき裂形状との対応について調べるため、CTの測定を行った後、試料をエポキシ系樹脂に埋め込み、表面から80 µm程度研磨を行った。この研磨を行った試料についてSEMにより実際の内部のき裂断面形状を観察した。
試料表面のCT像、光学顕微鏡およびSEM像を図7に示した。また、同一き裂の80 µm内部のCT像およびSEM像を図8にそれぞれ示す。この場合、X線のエネルギー35 keV、カメラ−試料間距離1,160 mmとした。測定では0°から180°まで1°刻みで透過像を得た。図7(b)に示した光学顕微鏡画像では、点線で囲まれた領域Aのように摩擦痕とき裂との区別が困難な箇所がある。一方図7(c)のSEM画像よりこの摩擦痕近傍にき裂が見られることがわかる。CT像では、SEM画像と同様の形状のき裂が観察されている。

図7 表面における観察結果の比較
試料表面から80 µm内部では、図8(a)および(b)より、SEM画像のき裂と同じ位置にCT像でもき裂像が得られていることがわかる。しかしながら、表面近傍と内部のCT像では、き裂像の様相が異なっている。表面近傍では連続な形状としてき裂が検出されているのに対し、試料内部では粒状の像が連結した形状が観察されている。図8(b)に示した、これらのき裂形状を示す箇所の詳細なSEM画像より、粒状の像が観察された領域Bではき裂面の粗さが大きく、部分的にき裂面が接触していることがわかる。き裂像のコントラストが低く観察された領域Aでは、領域Bと比較してき裂の開口量が小さい。したがって、CT像上でき裂が粒状に観察される箇所は、き裂開口量が大きくかつ部分的に接触しているものと考えられる。

図8 内部における観察結果の比較
これらのことによりCT像では、内部の詳細なき裂形状が反映されており、非破壊的にき裂形状の三次元像を得ることができるため、試料内部におけるき裂伝ぱのモード変化やき裂の合体に伴う複雑な形状変化を観察できることがわかった。
3-2. ねじり疲労き裂の観察
ねじり疲労におけるき裂も、その成長に伴って、せん断モードから引張りモードへき裂伝ぱモードが変化して、複雑なき裂形状を呈することが知られているため、そのメカニズムを解明することを目的としてCT観察を行った。観察に用いた材料は、高強度鋼である。X線エネルギー35 keV、カメラ−試料間距離160 mmとし、0°から180°までを1°刻みで透過像を得た。
検出されたき裂の試料表面におけるSEM画像および試料表面に平行な内部の断面におけるCT像を図9に示した。図より、試験片長手方向に伸びたCrack Aと幅方向に伸びたCrack Bの2つのき裂が存在していることがわかる。

図9 ねじり疲労き裂のCT像
フレッティング疲労き裂とは異なり、カメラ−試料間距離を160 mmと小さくした場合でも、ねじり疲労き裂が検出された。この原因として、応力比R = −1のねじり疲労試験では、き裂面が接触し摩耗することで、無負荷状態でもき裂が開口していたものと考えられる。
Crack AおよびCrack Bの三次元イメージング像を図10および11にそれぞれ示す。図10より、Crack Aはき裂長さ40 µm、き裂深さ20 µm程度のき裂と、き裂長さ30 µm、深さ10 µm程度の2つの表面き裂で構成されていることがわかる。また、図11よりCrack Bは、試料側面に向かってき裂が深くなっていることから、試料の切断面がき裂を横切っていることがわかる。Crack AおよびCrack Bはき裂先端が部分的に開口した複雑な形状を示している、また全体としては最大せん断応力面に沿っていても微視的には最大主応力方向に垂直となっている部分の多いことは興味深い点である。
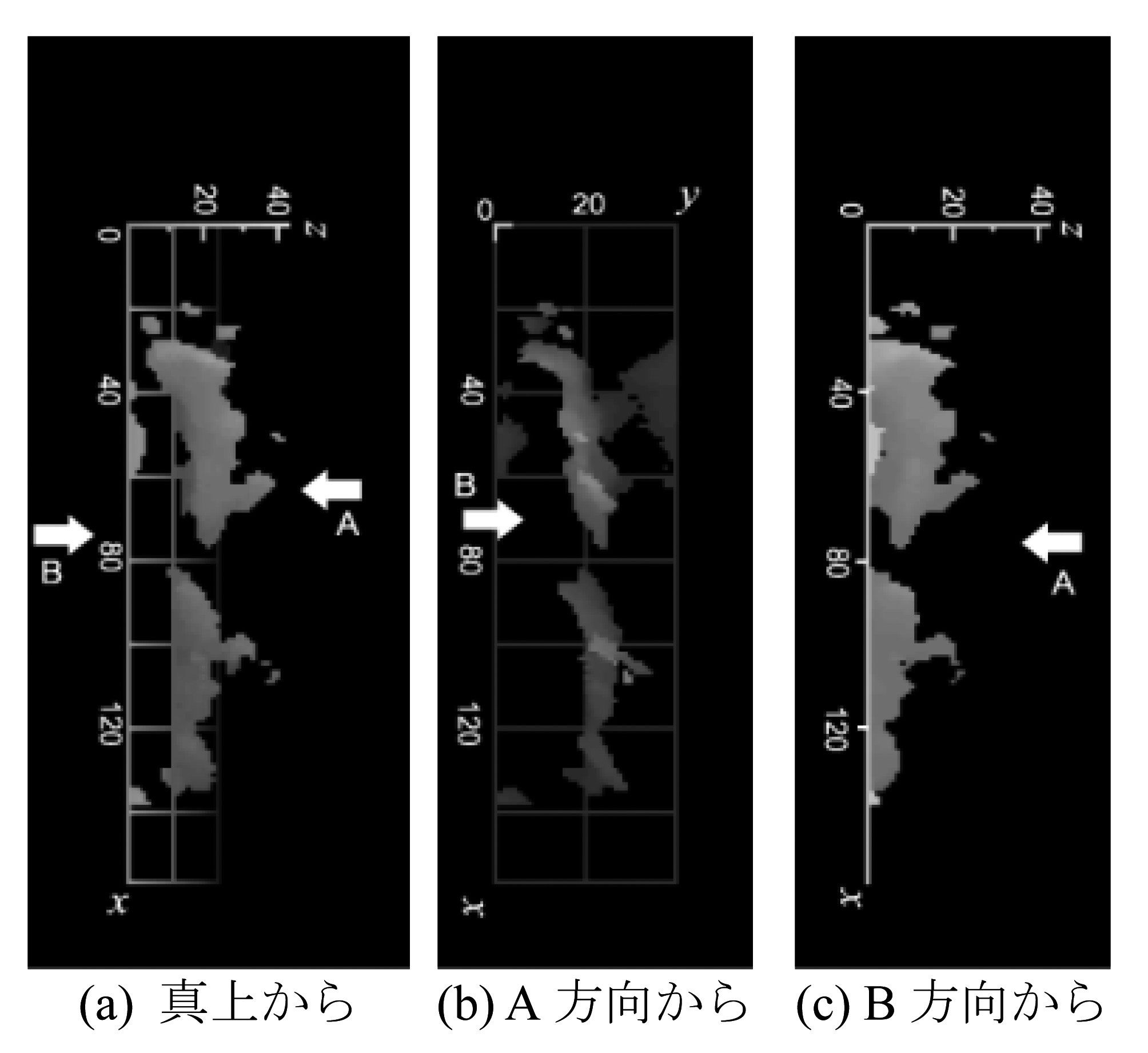
図10 ねじり疲労き裂のイメージング(Crack1)

図11 ねじり疲労き裂のイメージング(Crack2)
4. おわりに
放射光を利用したCTイメージングは、これまでにも疲労研究にある程度利用されてきたが、工業的に最も多く用いられている鉄鋼材料に対しては、適用例がほとんどなかった。そのため、本研究会では、鉄鋼材料に的を絞り、共同研究を行ってきた。その結果、鉄鋼材料中の介在物やき裂に対しても、放射光CTは有効であることが明らかになった。今後は、これらの成果を活用して、鉄鋼材料における未知の疲労現象の解明を行いたいと考えている。
なお、本研究会は、SPring-8利用推進協議会・SPring-8疲労損傷評価研究会、日本材料学会疲労部門委員会・高輝度放射光による疲労損傷評価技術研究分科会とも密接な連携を保ちながら運営しており、これら委員会を通じて、産業界、学界の金属疲労に関するニーズを調査している。SPring-8に興味を持っていても、利用に関する手続きや測定方法がわからない研究者・技術者にアドバイスを行い、SPring-8の利用促進に協力したいと考えている。
参考文献
[1] Y. Nakai, D. Shiozawa, H. Tanaka, Y. Morikage, H. Okado and T. Miyashita: "Quantitative Analysis of Inclusions and Fatigue Cracks in Steel by X-ray Computed Tomography Using Ultra-bright Synchrotron Radiation", New Methods of Damage and Failure Analysis of Structural Parts, Ostrava, Czech (2006) 277-286.
[2] 塩澤大輝、中井善一、森影康、田中拓、尾角英毅、宮下卓也:「高輝度放射光のX線CTイメージングを用いた高強度鋼中の介在物の定量的評価」日本機械学会論文集(A)、第72巻、第724号 (2006) 1846-1852.
[3] Y. Nakai, D. Shiozawa, Y. Morikage, T. Kurimura, H. Tanaka, H. Okado and T. Miyashita: "Observation of Inclusions and Defects in Steels by Micro Computed-tomography using Ultrabright Synchrotron Radiation", Fourth International Conference on Very High Cycle Fatigue Edited by John E. Allison, J. Wayne Jones, James M. Larsen and Robert O. Ritchie: The Minerals, Metals & Materials Society (2007) 67-72.
[4] 塩澤大輝、中井善一、栗村隆之、森影康、田中拓、尾角英毅、宮下卓也、梶原堅太郎:「放射光マイクロトモグラフィによる鋼中のき裂観察」、材料、Vol.56, No.10 (2007)に掲載予定
中井 善一 NAKAI Yoshikazu
神戸大学大学院 工学研究科 機械工学専攻
〒657-8501 神戸市灘区六甲台町1-1
TEL : 078-803-6128 FAX : 078-803-6155
e-mail : nakai@mech.kobe-u.ac.jp