Volume6 No.1
SPring-8 Section B: Industrial Application Report
異なる製造法による硫化物系固体電解質ガラスの構造解析
Structural Analysis of the Sulfide Solid Electrolyte Glass Obtained by Different Production Methods
a出光興産株式会社,b(国研)物質・材料研究機構
aIdemitsu Kosan Co., Ltd., bNIMS
- Abstract
-
硫化物系固体電解質ガラスLi3PS4において、ラボで合成可能なメカニカルミリング法(MM法)と量産化が見込める溶媒を用いた製法(新プロセス法)によるÅ~nmスケールの構造差を、HEXRD (High Energy X-Ray Diffraction) により調べた。両製法を比較した場合、二体分布関数G(r)による局所構造評価では有意な差は見られず新プロセス法においてもMM法と同等の局所構造を有する材料を合成できることが分かった。一方で構造因子S(Q)において、新プロセス法により合成した材料はQが0.5 Å-1以下の低波数領域に強い散乱が見られたことから、ナノサイズよりも大きい領域で、異なる製造法により構造差があることが分かった。また、SAXS (Small Angle X-ray Scattering) 測定の結果から、これは球形近似で数十nmの構造体であることが分かった。
キーワード: 固体電解質、HEXRD、SAXS、二体分布関数
背景と研究目的:
近年、安全性が高く、高容量のリチウムイオン電池の開発が活発になされている。現在実用化されているリチウムイオン電池は、電解質が可燃性液体であるため、安全性が低いという欠点がある。そのため、無機固体電解質が開発されている。固体電解質のなかでも、硫化物系固体電解質は高いイオン伝導性を有していることから、積極的に研究されている[1][2][3]。
硫化物系固体電解質の工業化へ向けた課題の1つとして製造費用の削減がある。材料合成は、粉末を混合して化学反応を起こすメカニカルミリング法(MM法)が用いられることが多いが、反応に長時間かかり、またエネルギー消費も大きく製造費用が非常に高く大量生産には不向きである。一方で、溶媒を使用した製法(新プロセス法)[4]なども検討されており、エネルギー消費、反応時間の面でメカニカルミリング法よりも優れており工業化へ向けた製造法として有望視されている。
溶媒を使用した製造法は工業化へ向けて将来性があると期待されているものの、メカニカルミリング法と比べ電池性能として重要なイオン伝導度やサイクル特性が劣る課題がある。要因解明のため、これまでXRD、NMR、Ramanによる構造解析や、各種不純物量の分析を行っているが詳細は分かっていない。製造法によりガラス構造自体に差がありイオン伝導度へ影響している可能性を検証するため、高輝度・高エネルギーである放射光の特徴を活かした測定データを用い、非晶質構造解析を行なった。
試料はLi2S-P2S5系ガラスをMM法(1_MM、2_MM)及び新プロセス法(3_new~7_new)で合成した。その一覧を表1に記す。熱処理はガラス合成後にガラスセラミックス化させる後処理であり、製造スケールの小は実験室レベルのMM法による小量合成、中と大は工業生産が見込める新プロセス法による中~大量合成である。いずれの試料も露点-80℃のN2雰囲気下グローブボックス内において、WJM-Glas/Muller GmbH製の直径2.0 mmのホウケイ酸ガラスのキャピラリに入れ、紫外線硬化性樹脂で密封し測定した。バックグラウンドとして空のホウケイ酸ガラスキャピラリも準備し測定した(8_blank)。
表1. 測定試料一覧
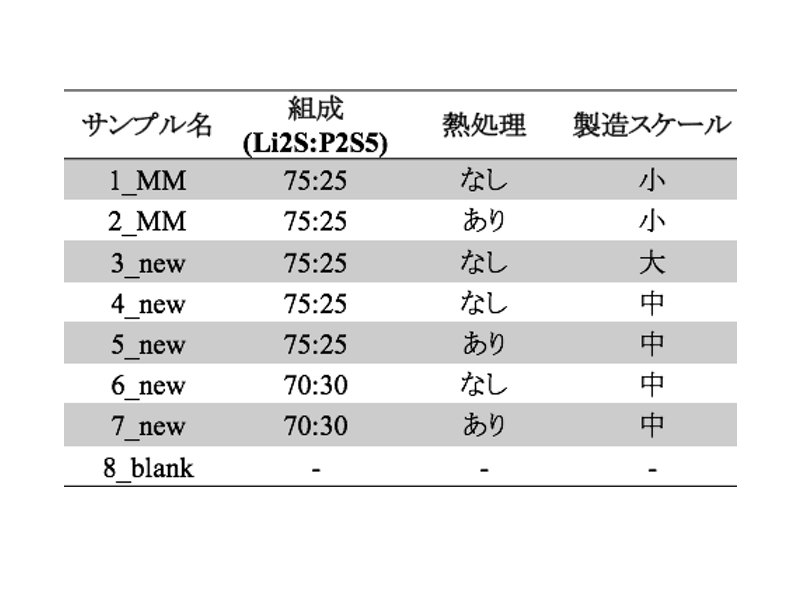
HEXRD測定はBL04B2において、入射エネルギー61.7 keV(波長約0.20 Å)とし、検出器はGe半導体0次元検出器を用いた。散乱ベクトルQのレンジは実験検討の過程で条件変更及び再測定したため、0.5~25 Å-1と0.2~25 Å-1の散乱強度I(Q)を得た(図1)。解析はBL04B2にあるRDF解析専用ソフトを用いた。なおRDF解析専用ソフトでは(式1)により散乱強度のバックグランド補正(8_blankを使用)、コンプトン散乱補正、偏光補正、吸収補正を行い、(式2)により、構造因子S(Q)を算出した(図2)。密度は1.95 g/cm3、偏光因子は0.05とした。
ここで、Iscohは試料の干渉性の散乱強度、Iobs(Q)は実験で得られた試料の散乱強度、IBG(Q)は空のホウケイ酸ガラスキャピラリの散乱強度、Icomp(Q)はコンプトン散乱、P(Q)は偏光因子、Aは吸収因子である。また、Nは粒子数に相当する規格化定数、<f(Q)>2は原子形状因子平均の2乗、<f(Q)2>は原子形状因子の2乗平均である。
また、得られた構造因子S(Q)をRDF解析専用ソフトにより(式3)に従いフーリエ変換することにより還元二体分布関数G(r)を算出した(図3)。このとき、フーリエ変換の範囲は0.2~25 Å-1とし、Window Function は Lorch 関数を用いた。
SAXS測定は金沢大学のNano-Viewer(リガク製)で測定した。Nano-Viewerの測定はCu-Kα(波長1.58 Å )線を用い、出力1.2 kW、カメラ長950 mm、散乱ベクトルQのレンジは0.12~3.5 nm-1で、IP検出器を用いた。粒径解析はNano-Solver(リガク製)を用いた。


図1. HEXRDにより得られた散乱強度IQ)(左:熱処理なし、右:熱処理あり)


図2. HEXRDにより得られた構造因子S(Q)(左::熱処理なし、右:熱処理あり)
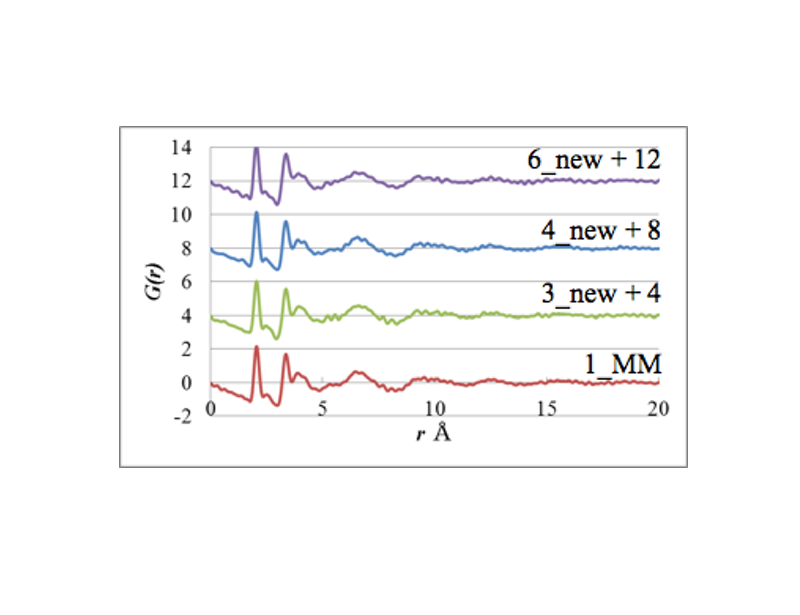

図3. HEXRDにより得られた還元二体分布巻数G(r)(左::熱処理なし、右:熱処理あり)
結果および考察:
図1のI(Q)において、熱処理なしの試料(1_MM、3_new、4_new、6_new)は原料由来のBraggピークはほとんど観察されず、MM法、新プロセス法いずれにおいてもガラスを合成できていることを確認した。熱処理ありの試料(2_MM、5_new、7_new)においては製造法よりも組成と熱処理条件によって形成される結晶相と割合が決まることを確認した。
特に着目している試料として、組成がLi2S:P2S5=75:25で製造法が異なる1_MMと3_new、4_newの還元二体分布関数G(r)を比較すると(図4)、ガラスの局所構造に違いは見られなかった。これは、製法によりガラス構造に差があるという仮説を支持せず、今回の工業化に向けた新プロセス法から合成した試料(3_new、4_new)は、平均構造としてMM法(1_MM)で合成した試料と同等の局所構造を有していることが示唆された。これは、電池性能の低下はガラス構造に起因していないことを意味する。一方で構造因子S(Q)(図5)においては、Qが0.5 Å-1以下の低波数領域において製造法による違いが確認された。より低波数側になるにつれて、MM法(1_MM)はほとんど散乱強度が確認されないが、新プロセス法(3_new、4_new)は強い散乱強度が確認された。このことから、MM法と比較し新プロセス法は、ナノサイズの密度差を有することが示唆された。
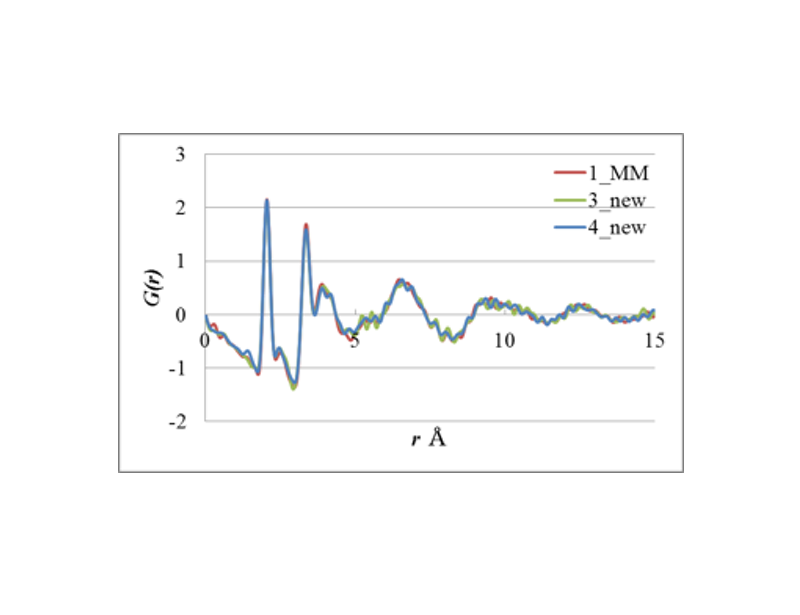
図4. 製造法の異なるLi2S:P2S2=75:25ガラスにおける還元二体分布関数G(r)の比較
図5. 製造法の異なるLi2S:P2S2=75:25ガラスにおける構造因子S(Q)の比較
ナノサイズの構造体を詳細に調べるため、1_MMと4_newのSAXS測定を行った。得られた散乱パターンを図6に示す。HEXRD測定結果の通り、MM法(1_MM)ではほとんど小角の散乱は確認されず、新プロセス法(4_new)では等方的な強い散乱が確認された。粒子の形状に依存した領域(Q=0.13~0.6 nm-1)において、4_newの累乗近似の指数は-4.05となり(図7)、-4に近いことからナノサイズの構造体は球形と推定した[5][6]。ナノサイズの構造体を球形の空隙と仮定し粒界解析ソフトNano-Solverを用いてQ=0.12~0.85 nm-1でカーブフィティングすると、そのサイズは約30 nm前後、規格化分散は約27%となった。
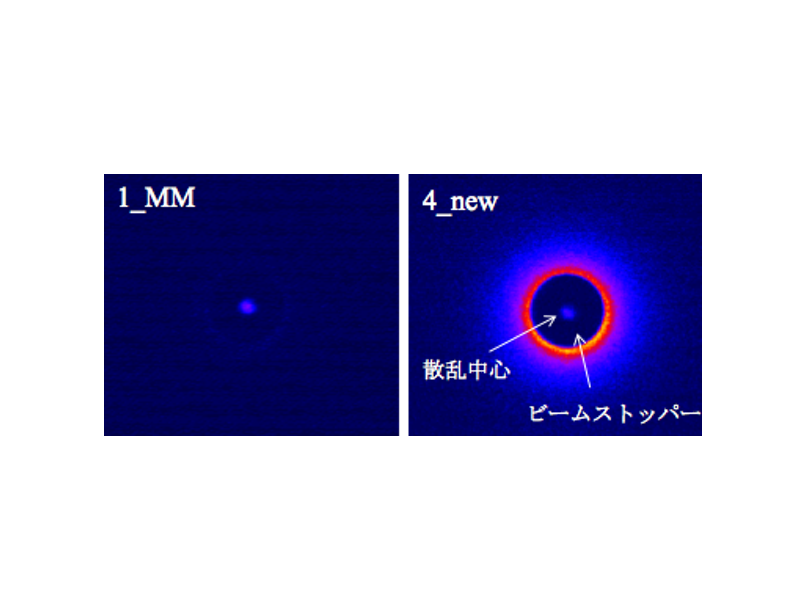

図6. SAXS測定結果(左:二次元散乱パターン、右:全方位積分した一次元プロファイル)
図7. 4_newのSAXS測定結果の累乗近似(赤線:実験データ、黒破線:累乗近似曲線
今後の課題:
HEXRDを用いることで、製造法の異なる試料間の構造差を原子レベルからナノサイズレベルまで比較でき、工業化を見据えた新プロセス法においてMM法と同等のガラス構造を作製できていることを確認し、一方でナノサイズの領域で構造差があることが分かった。全固体電池の実用化に向けては、より高イオン伝導度で安価に量産できる固体電解質材料とその製造プロセス開発が必須である。今後も材料自体の詳細構造解析と、プロセスに起因する構造と性能の相関解明に取り組む。
謝辞:
本研究の実験にご協力頂いた金沢大学理工学域物質化学類太田昭雄准教授に感謝の意を表します。
参考文献:
[1] 辰巳砂昌弘、セラミックス, 50(12), 933 (2015)
[2] Y Seino, Energy Environ. Sci., 7, 627 (2014)
[3] Y Seino, J. Mater. Chem. A, 3, 2756 (2015)
[4] 太田剛、紛体技術、8(5), 431 (2016)
[5] 雨宮慶幸、放射光, 19(6), 338 (2006)
[6] G Porod, Kolloid Z., 124, 83 (1951)
ⒸJASRI
(Received: April 18, 2017; Early edition: September 22, 2017; Accepted: December 18, 2017; Published: January 25, 2018)