Volume5 No.1
SPring-8 Section B: Industrial Application Report
レーザー衝撃を与えたアルミニウム合金のX線小角散乱
Small Angle X-ray Scattering of Laser-shocked Aluminum Alloys
a(株)東芝, b大阪大学, c(公財)高輝度光科学研究センター
aToshiba Corporation, bOsaka University, cJASRI
- Abstract
-
レーザーを照射した析出強化型アルミニウム合金のX線散乱強度を、小角散乱(SAXS)および極小角散乱(USAXS)により測定した。その結果、レーザー照射によって機械的な衝撃を与えると、散乱強度が増大することがわかった。パルス幅約8 nsのNd:YAGレーザーの照射では、散乱ベクトルqの広い範囲で散乱強度が増大した。一方、パルス幅約130 fsのTi: Sapphireレーザーの照射では、高q領域で散乱強度の顕著な増大が認められた。
キーワード: アルミニウム合金,レーザー衝撃,微細組織,SAXS,USAXS
背景と研究目的:
金属材料の強化手法の一つに析出強化があり、溶体化や時効処理といった熱処理により材料全体の特性を制御する手段として使われている。レーザーにより析出を制御できれば、必要な部位のみを高強度化することが可能となる。また、溶接などの入熱により析出物が溶解して強度が低下した部位の強度回復にも使用できる可能性がある。
析出強化型の合金に対してレーザー衝撃により高いひずみ速度で動的時効処理を行うと、微細な析出物が生成される可能性が示唆されている[1, 2]。また、TEMによる組織観察では析出物の生成が確認されているが[3]、材料強度を決定付けるμm以上のマクロな領域に対するデータは皆無である。そこで、レーザー衝撃による析出物の生成とその分布に関する知見を得ることを目的として、析出強化型のアルミニウム合金に対する小角散乱(SAXS)および極小角散乱(USAXS)を試みた。
実験方法:
1. 試験片の作製
供試材は航空機グレードのAl-Si-Mg系A6061およびAl-Cu系A2024アルミニウム合金とし、素材メーカーにてT3処理されたものを購入した。T3処理は析出物の溶体化処理を行った後に強度向上のために冷間加工を行い、さらに自然時効させることにより析出物を成長させたものである。購入した供試材はケミカルミリングにより薄肉化し、数十mm角に切断して試験片とした。一部の試験片には溶体化処理(ST)を施してT3処理によって生じた析出物を固溶させたのち、自然時効を行った。レーザー衝撃処理は表面処理技術の一つであり、その効果は表面および表面からある深さに限られるため、本実験においては試験片の厚さは薄い方が好ましい。このため、ケミカルミリングで安定に薄肉化できる試験片として、厚さ0.1 mmおよび0.2 mmの試験片を用意した。なお、当初測定を計画していたA7075については航空機グレードの供試材の調達が困難であったため、測定を見送った。
2. レーザー照射
各試験片には、レーザーパルスを照射して表面に高圧のプラズマを発生させ、機械的な衝撃を与えた。析出物の生成およびその分布に対するひずみ速度の影響を確認するため、パルス幅約8 nsのNd:YAGレーザーとパルス幅約130 fsのTi: Sapphireレーザーを使用した。レーザーを照射した際の材料のひずみ速度は、各々106 /sおよび1011 /sのオーダーと考えられている[4, 5]。
レーザーの照射条件を表1に示す。Nd:YAGレーザーはパルス幅が長いため、大気中の照射では十分な衝撃が得られない[6]。このため、試験片の表面にアクリル板を張り付けてプラズマを閉じ込め、レーザー照射による衝撃を高めた。Ti: Sapphireレーザーの場合には、パルス幅が短くピーク出力が高いため、大気中での照射においても大きな衝撃を得ることができる[5]。
Nd:YAGレーザーは試験片に対して1パルスのみ照射し、その照射痕内でSAXSおよびUSAXSを行った。Ti: Sapphireレーザーはパルスエネルギーが小さいため、十分なプラズマ圧力を発生させるためにはレーザーパルスを0.1 mm以下に絞り込む必要がある。そこで、レーザーを2次元的にスキャンして試験片に照射し、SAXSおよびUSAXSを行うための十分な面積を処理した。その際、レーザーパルスのカバレージは80%および692%とした。ここで、カバレージは試験片に照射した全レーザーパルス数をN,照射スポット径をD,処理面積をAとするとπD2N/4Aで定義され、試験片表面の各点に照射されるレーザーの平均パルス数に相当する。従って、カバレージが692%の試験片は、約7回繰返してレーザー衝撃による冷間加工を受けたことになる。
表1.レーザーの照射条件

3. X線小角散乱実験
SAXSおよびUSAXSはSPring-8の産業用ビームラインBL19B2で行った。X線のエネルギーは18 keVとし、レーザーを照射した部位とレーザーを照射していない部位について散乱強度を測定した。SAXSでは試験片と検出器(PILATUS-2M)を第3実験ハッチに設置し、カメラ長(試験片と検出器の距離)を3.1 mとした。USAXSでは試験片を第2実験ハッチに設置し、カメラ長を41.8 mとした。なお、カメラ長の校正にはコラーゲンを用いた。
実験結果:
試験片およびレーザーの照射条件と結果との対応を表2に示す。
表2.試験片およびレーザーの照射条件と結果との対応
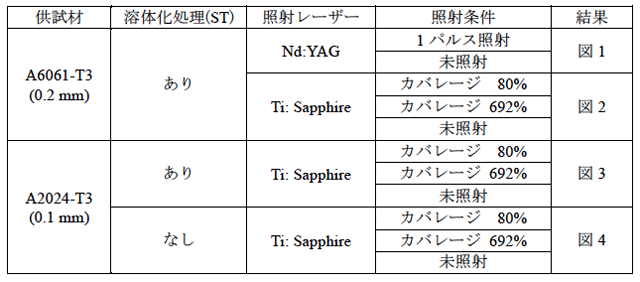
1. A6061試験片の散乱プロファイル
溶体化処理(ST)したA6061試験片(厚さ0.2 mm)の散乱強度を図1および図2に示す。両図とも左側がUSAXS,右側がSAXSの結果である。レーザーを照射していない部位の散乱プロファイルは-4乗に近いq依存性を持っている。Nd:YAGレーザーを照射すると、散乱強度が約2倍となり、プロファイルがほぼ平行に移動した(図1)。一方、Ti: Sapphireレーザーを照射した試験片は、レーザー衝撃が約1回(カバレージ80%)の場合にはq依存性が僅かに変化する程度であったが、レーザー衝撃が約7回(カバレージ692%)の場合には散乱強度が高q側で大きく増加し、q > 0.3 nm-1で20倍以上の散乱強度が得られた(図2)。カバレージ692%の試験片は、相互作用時間の短いTi: Sapphireレーザーの照射による衝撃で繰返し冷間加工を受けたため、微細な空間サイズ(高q側)の変化が誘起されたものと考えられる。
図1のA6061試験片は、SACLAにてNd:YAGレーザーを照射して動的XRD実験に供した試験片である[7]。SACLAにおける動的XRD実験では、結晶粒の微細化や亜粒界の生成などが示唆されている[1, 2]。また、Ti: Sapphireレーザーの照射では、材料は高いひずみ速度で変形を受け、相互作用時間が短いことから、より微細な空間サイズでの変化が誘起された可能性がある。
2. A2024試験片の散乱プロファイル
A2024試験片(厚さ0.1 mm)の散乱強度を図3および図4に示す。図3は溶体化処理(ST)材の結果を、図4はT3時効処理材の結果を示している。両試験片ともレーザー衝撃はTi: Sapphireレーザーにより行った。レーザー衝撃が約1回(カバレージ80%)の場合には、溶体化処理(ST)材(図3)ではほとんど変化が現れなかったが、T3時効処理材(図4)では高q側で散乱強度が増加した。レーザー衝撃により繰返し約7回(カバレージ692%)の冷間加工を行った場合には、散乱強度が大きく増大し、特にT3時効処理材(図4)の高q側で散乱強度が顕著に増大した。
図3および図4において約1回のレーザー衝撃を与えた試験片と約7回の繰返し衝撃を与えた試験片の散乱プロファイルの差に着目すると、レーザー衝撃回数を約1回から約7回に増加させたことにより散乱強度が大きく増加していることが分かる。また、散乱強度の増加分は、溶体化処理(ST)材とT3時効処理材でほぼ同様の傾向を示すことが分かる。
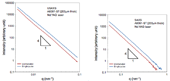
図1.Nd:YAGレーザーの照射による散乱強度の変化(A6061溶体化処理材)
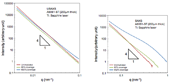
図2.Ti: Sapphireレーザーの照射による散乱強度の変化(A6061溶体化処理材)
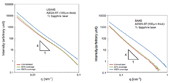
図3.Ti: Sapphireレーザーの照射による散乱強度の変化(A2024溶体化処理材)
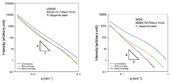
図4.Ti: Sapphireレーザーの照射による散乱強度の変化(A2024 T3時効処理材)
結論および今後の課題:
析出強化型のアルミニウム合金A6061およびA2024にレーザー照射による機械的な衝撃を加えると、散乱強度が増大することが分かった。散乱強度の増大は、結晶粒微細化による粒界の増大や析出物の生成など様々な要因が考えられる。このため、TEMによる微細組織観察、X線回折による析出物の同定、SACLAにおけるレーザーポンプ& XFELプローブ実験[1, 2]の結果なども考慮して、析出ダイナミクスの検討と散乱強度プロファイルの定量的な評価を実施していく予定である。また、最終的には、レーザー衝撃を加えた試験片の疲労試験を行い、レーザー衝撃による材料の超高強度化を実証する予定である。
参考文献:
[1] 佐野雄二, 第2回SACLAシンポジウム要旨集, 東京国際フォーラム, 2012年12月8日.
[2] 佐野雄二 他, 日本物理学会第68回年次大会, 広島大学, 2013年3月29日.
[3] Y. Liao et al., J. Appl. Phys. 110, 023518 (2011).
[4] 佐野雄二 他, 日本原子力学会誌, 42, 567 (2000).
[5] T. Sano et al., J. Appl. Phys. 90, 5576 (2001).
[6] Y. Sano et al., Nucl. Instrum. Methods Phys. Res. B, 121, 432 (1997).
[7] 佐野雄二 他, 平成24年度 利用課題実験報告書(2012A), 2012A8012, SACLA一般課題.
ⒸJASRI
(Received: September 2, 2016; Early edition: December 2, 2016; Accepted: December 12, 2016; Published: January 31, 2017)