Volume5 No.1
SPring-8 Section B: Industrial Application Report
半導体パッケージ基板用樹脂の熱硬化過程における残留応力その場観察
による最適熱処理プロセス条件検討
In situ Residual Stress Analysis in Thermosetting Resins for Semiconductor Packaging Substrate during Curing Process for Investigation of their Optimum Thermal Process
住友ベークライト(株)
SUMITOMO BAKELITE CO., LTD.
- Abstract
-
半導体パッケージ基板用樹脂/銅箔界面の残留応力について、基板用樹脂の熱硬化過程におけるその場観察を行い低温短時間硬化の影響を確認した。加熱試料台を用い、Cu(331)面のX線回折プロフィール変化を側傾法により測定、sin2ψ法により熱時の残留応力を算出した。その結果、硬化条件によって応力が異なることが分かり、半導体パッケージ基板用樹脂の低温短時間硬化の可能性を見出した。
キーワード: 残留応力解析、sin2ψ法、その場観察、半導体パッケージ、基板材料、長期信頼性、熱プロセス検討
背景と研究目的:
近年の半導体高性能化および長期信頼性の観点から、半導体パッケージ基板用樹脂(以下、基板樹脂)には高度な耐熱性、電気絶縁性、熱伝導性、耐湿性が求められている。半導体パッケージ基板は、熱硬化性樹脂と無機フィラーを主成分とする基板樹脂と金属(配線およびリードフレーム)で構成される複合部材である。それら異種材料間の弾性率と線膨張率(CTE)が異なるため、半導体パッケージ製造工程における熱プレスおよび熱硬化、半田リフローなどの複数の加熱冷却過程を経ることにより樹脂と金属界面に発生する熱応力が残留応力として蓄積し、半導体パッケージの歪みや反りの要因となる。それらは、界面の密着性に影響を与え、最終的には剥離という半導体パッケージにおける致命的な不良につながる。また、近年は半導体製造コスト低減や省エネルギーの観点により、樹脂の成形時間の大幅な短縮が求められている。しかしながら、成形時間短縮は樹脂の硬化不足をもたらし、後の熱プロセスにおいて硬化収縮が発生するため、材料界面の残留応力にも大きく影響を与える要因となる。したがって、樹脂の最適な熱プロセス条件を残留応力の観点から評価する解析技術確立も長期信頼性保障の観点で重要となる。
半導体パッケージ基板における熱硬化性樹脂/銅箔界面の残留応力評価手法としては、我々がこれまでに検討してきたX線回折法による評価技術が特に有効である[1–3]。本検討では基板樹脂の硬化条件を様々に変化させ硬化後の残留応力をX線回折の原理に基づくsin2ψ法[4–6]を用いて測定することで、残留応力の観点から最適な熱硬化条件を得ることを目的とした。
実験:
半導体パッケージにおける基板樹脂/銅配線界面のモデル試料として、銅箔(厚さ12 μm)上にシリカフィラー含有量が70 wt%の熱硬化性の基板樹脂を140°Cで30分間成形し、ダイシングにより20 mm × 20 mm × 0.50 mmの測定試料を得た。なお、本検討で用いた基板樹脂のガラス転移温度(Tg)は約255°Cである。残留応力測定はBL19B2のHUBER社製多軸回折計を用いて実施し、入射X線エネルギーは25 keV、入射X線ビームサイズは縦0.2 mm × 幅6 mmとし、回折X線は発散角0.1°のソーラースリットを介してシンチレーションカウンターにより計測した。加熱試料台にはアントンパール社製試料加熱ステージDHS1100を用い、初めに室温での応力測定を行った後、硬化処理を行い、室温まで冷却した。更に、260°C 40分加熱および室温への冷却の加熱サイクル処理を2回実施し、再度応力測定を行った。硬化処理は、①260°C 80分、②225°C 80分、③225°C 40分の3水準とした。なお硬化後の260°C加熱は半田リフロー工程を想定した温度である。また硬化条件③においては加熱サイクル途中でビームダンプが起こったため加熱サイクルを1サイクル増やして測定を行った。残留応力解析方法はNakamaeやNishinoらによる、エポキシ樹脂/金属界面の残留応力解析法を参考にsin2ψ法を適用し[4–6]、側傾法でCu(331)面の回折ピークプロフィールを測定した。回折ピークトップはガウス関数フィッティングにより算出した。sin2ψ法におけるオフセット角度(ψ)は、0.0、13.6、24.1、31.8、38.6、41.8、45.0°とし、試料台傾斜時の試料落下防止のため、試料台付属のクリップを用いて測定試料の四つ角を固定した。sin2ψ法による残留応力計算においてはCuの物性データとして弾性率は65.0 GPa、ポアソン比は0.343を用いた[7]。
結果および考察:
図1に硬化条件②および加熱サイクル処理後の室温におけるCuの回折ピークプロフィールのψ依存性を示す。いずれのψにおいても明確な回折ピークプロフィール、およびψ増加に伴う回折ピークトップの広角シフトが観測された。また、図2に示す2θ-sin2ψ線図が直線状であることから、本検討の残留応力評価手法の妥当性が確認された。近似直線の傾きとフィッティング誤差より、圧縮応力は74.1 ± 4.2 MPaと算出された。
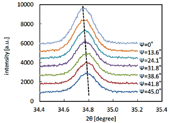
図1 硬化条件②による硬化および加熱サイクル後の
Cu(331)面の回折ピークプロフィールのψ依存性
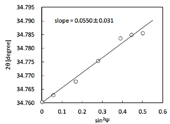
図2 Cu(331)面の回折ピークトップ変化から得られた2θ-sin2ψ線図
図3に硬化条件①〜③および加熱サイクルの熱プロセスにおける基板樹脂/銅箔界面の応力のその場観察結果を示す。算出応力の誤差は、前述の通り近似直線フィッティング誤差より求め、図中にエラーバーとして示した。いずれの硬化条件においても加熱時は圧縮応力が緩和し、冷却時は圧縮応力が増大するという応力変化挙動が共通して確認できる。そこで残留応力変化を樹脂の熱膨張および硬化収縮の観点から考察する。
(a) 成形後の室温状態において、未硬化の基板樹脂はいずれも室温で圧縮応力を示した。これは樹脂成形時(140°C、30 min)において室温時と比較して樹脂が熱膨張した状態で基板樹脂/銅箔界面が形成され、140°Cから室温に戻した際の樹脂の熱収縮により銅箔側が圧縮されたためと推定される。
(b) 熱硬化過程において圧縮応力は減少した。これは樹脂の熱膨張によって銅箔側の圧縮応力が緩和されたためと考えられる。また、硬化過程において10–20 MPaの圧縮応力を示した。これは、硬化収縮によって生じた残留応力と推定される。
(c) 硬化温度から室温に冷却した結果、圧縮応力は増大した。これは、冷却に伴う樹脂の熱収縮によるものと推定される。この時、硬化条件①においては硬化前(a)と比較して硬化後(c)の圧縮応力が増加した。これは熱硬化過程(b)において、分子鎖運動性が高くなるTg近傍での緩和収縮も進行した結果と推定される。この考察は、硬化過程(b)における圧縮応力が①と②③で同等である結果と一見矛盾するが、①の熱硬化過程(b)においては熱膨張と硬化収縮の影響が、②③と比較していずれも大きいためと考えられる。
(d) 半田リフロー工程を想定した260°Cに再加熱し室温に戻した結果、硬化条件①においては加熱前後の応力に差はないが、硬化条件②においては半田リフロー工程前(c)と比較して圧縮応力が増大した。これは硬化条件①で観察されたTg近傍での緩和収縮が硬化条件②の半田リフロー工程において生じた結果と推定される。なお、硬化条件③に関しては、ビームダンプの影響のため、半田リフロー工程1サイクル目の評価ができなかった。
(e) (f) 同サイクルをさらに追加した結果、いずれの硬化条件においても室温および260°Cでの圧縮応力に変化は観察されなかった。これより、複数の半田リフロー工程においては、樹脂の更なる硬化収縮や構造緩和が生じていないことが示唆される。なお、225°Cにて熱硬化反応の完了は示差走査熱量測定によっても確認済みである。以上の結果より、本手法により試料の加熱冷却に伴う応力変化挙動の評価が可能であることが確認できた。
加熱サイクル処理後(e)の応力はそれぞれ①77.2 ± 4.6 MPa、②74.6 ± 4.2 MPa、③72.5 ± 3.9 MPaとなった。この結果から、半田リフロー工程後の残留応力の観点から、硬化条件③による半導体パッケージ基板用樹脂の低温短時間硬化の可能性を見出した。
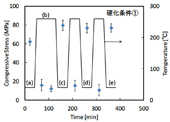
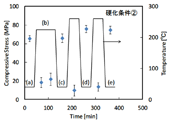
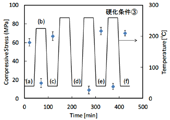
図3 硬化条件①②③の熱プロセスにおける基板樹脂/銅箔界面の応力のその場観察結果
◆:圧縮応力、―:温度
今後の課題:
本検討では硬化温度および硬化時間が異なる試料の残留応力を評価、比較することにより残留応力の観点から低温短時間硬化の可能性を見出した。今後、現在1測定あたり30–40分を要する測定時間の短縮のため、2D法もしくはcos α法などの二次元検出器を用いた残留応力評価技術についても検討を行う予定である。なお、本課題の実施にあたり、応力算出に用いる最適な回折ピークの探索、スリット条件、揺動条件、露光時間などの最適な測定条件決定のための検証実験に多くの時間を要した。また、X線回折測定用加熱試料台での加熱プロセスによって、多くの試料において測定後の反りが確認された。反りが生じた複数の試料の結果において、反りに伴う応力緩和の影響の評価は困難であり、かつ測定マクロを用いた連続測定であるためにどのタイミングで反りが生じたかの特定が困難であるため、当初計画していた異なる樹脂種についての検討は実施できなかった。X線回折測定用加熱試料台での測定に適したモデル材料の選定についても今後の検討課題である。
参考文献:
[1] 若林みどり 他, SPring-8/SACLA利用研究成果集, 3(2), 589 (2015).
[2] 若林みどり 他, SPring-8/SACLA利用研究成果集, 4(2), 275 (2016).
[3] 若林みどり 他, SPring-8/SACLA利用研究成果集, 4(2), 294 (2016).
[4] 田中啓介 他, 放射光による応力とひずみの評価, 及川清, 養賢堂, 東京 (2009) p56.
[5] K. Nakamae et al., J. Appl. Polym. Sci., 40, 2231 (1990).
[6] T. Nishino et al., J. Appl. Polym. Sci., 45, 1239 (1992).
[7] 小出昭一郎, "物理学", 真喜屋実孜, 裳華房, 東京 (2003) p89.
ⒸJASRI
(Received: November 5, 2015; Early edition: August 25, 2016; Accepted: December 12, 2016; Published: January 31, 2017)