Volume4 No.2
SPring-8 Section B: Industrial Application Report
BL28B2における非対称反射結晶の導入
Introduction of Asymmetrically Cut Crystal at BL28B2
(公財)高輝度光科学研究センター
JASRI
- Abstract
-
標準モノクロメータから得られる37 keV以上のX線は、Si(311)回折やSi(511)回折によるものであり強度が弱い。37 keV以上のX線を用いたCT測定の測定時間を短縮するために、強度が強いSi(111)回折で高エネルギーX線が得られるモノクロメータをBL28B2に準備して実験を行った。モノクロメータ結晶には非対称反射のシリコン結晶を準備し、X線の強度を重視して迅速な測定を目指した。83 keVのX線を用いて断面が1.5 mm × 1.5 mmの鉄鋼材料中のき裂や介在物を観察することができた。
キーワード: X線CT、金属材料、高エネルギーX線
背景と研究目的:
BL28B2で得られるX線は幅広いエネルギー帯のX線を含んでいる白色X線である。本ビームラインの特徴を活かすために、白色X線を試料に照射するエネルギー分散型の応力・ひずみ測定や白色X線トポグラフィが実施されてきた。BL28B2において単色化したX線を試料に照射する実験を行うことはなく、単色X線を使った実験は標準のモノクロメータを準備しているビームラインで実施されてきた。
しかしながら、標準のモノクロメータでは対応が難しい実験が増えつつある。その一つが高エネルギーの単色X線を用いたCT測定である。BL19B2における牧野らのCT観察は現状37 keVのX線を使って断面0.5 mm × 0.5 mmの高強度鋼中のき裂発生・進展挙動を観察しているが、より厚い試料の観察が必要となってきている [1, 2]。SPring-8標準のモノクロメータは特定のエネルギーのX線のみシリコン単結晶で回折させて取り出している。図1(a)に示すように角度αを調整することで、111面や311面による回折を選択することが可能である。装置の機械的な制限により回折角度θは最小で3°であり、このとき得られるX線のエネルギーはSi(111)およびSi(311)回折ではそれぞれ37 keVおよび73 keVである。37 keV以上のX線を使用する場合はSi(311)回折など高次の回折を用いることになるが、Si(111)回折と比較して強度が弱い。回折強度は以下の式で表される積分反射能Rに比例する [3]。
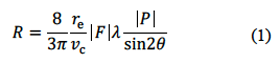
ここで、reは古典電子半径、vcは結晶の単位格子の体積、Fは結晶構造因子、λはX線の波長、Pは偏光因子およびθは回折角度である。回折指数の違いのみ考えると、Rは|F|/sin 2θに依存し、高次の回折ほど小さくなることは明らかである。現状CT測定時間は数時間に及ぶ場合があり、さらに長い測定時間での実験は現実的ではなくなってくる。一方、高エネルギーの白色X線を試料に照射してCT測定を行った場合は、バックグラウンドの増加やビームハードニングなどの画像劣化が顕著となるため、入射X線のエネルギー帯を制限することは必要である。
そこで白色X線のビームラインの特徴の一つとしてモノクロメータを自由に設計し設置できることを提案し、高エネルギーの単色X線を用いたCT実験環境整備を目的として実験を行った。特に、この際に非対称反射のモノクロメータを用いることで、より強度の強いX線を得ることを目指した。図1(b)に示すように結晶表面と回折面とが角度を持つとき、散乱面内においてX線の空間的な広がりが縮小するため単位面積当たりのX線強度を増加させることができる。入射X線の幅loと回折X線の幅lgは非対称因子bを用いて表され、非対称因子は以下の式で定義される。
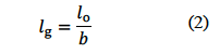
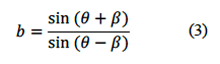
実験の評価項目として、「高エネルギーX線を使った際のき裂検出の可否」、「測定時間の長さ」、「検出可能なき裂サイズの下限値」および「時間に対するX線の強度およびエネルギーの安定性」が挙げられるが、今回は第一回目の実験であるため、まずは「高エネルギーX線を使った際のき裂検出の可否」および「測定時間の長さ」を評価した。
尚、課題申請では非対称反射のモノクロメータを用いたX線CTだけでなく、X線トポグラフィの実験も計画していたが、SPring-8の特徴をより活用することが可能である高エネルギーのCT実験に多くの時間を費やした。X線トポグラフィの実験は予備実験的に比較用のシリコン結晶のトポグラフ像を測定したに留まり、今回の課題ではそれ以上の測定は行わなかった。また、CTの観察においては試料としてセメント粒子を挙げていたが、高エネルギーX線の必要性が明らかな鉄鋼材料の観察のみ行った。
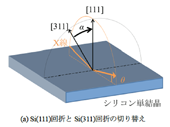
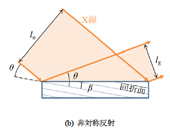
図1. モノクロメータ結晶によるX線の回折.
実験:
実験はBL28B2で行った。試料は高強度鋼であり、断面が0.5 mm × 0.5 mmのもの(試料Aと呼ぶ)と1.5 mm × 1.5 mmのもの(試料Bと呼ぶ)を準備した。試料の長さはおよそ10 mmであり、長手方向の中央付近を観察した。それぞれの試料をCT観察した時のレイアウトを図2に示す。いずれの実験においてもモノクロメータ結晶はシリコンであり、表面が111面から0.75°傾いたものを用いた。単色化における散乱面は図2に示すxy面(水平方向)である。散乱X線によるノイズの増加を防止するために、スリット、モノクロメータ、試料および検出器のそれぞれの間にステンレス製のパイプを設置した。検出器はCMOSカメラ(Flash2.8 浜松ホトニクス社製)とビームモニタを組み合わせたものを用いており、ビームモニタはBM2(浜松ホトニクス社製)とBM3(浜松ホトニクス社製)を準備した。ビームモニタでは試料の透過X線像を可視光の像に変換しレンズで拡大することが可能であり、CMOSカメラの実効的な画素サイズを小さくすることができる。CMOSカメラとBM2およびCMOSカメラとBM3の組み合わせにおける実効的な画素サイズは、それぞれ1.74 µmと0.63 µmであった。視野サイズはそれぞれ横1.2 mmと縦2.1 mmおよび横1.1 mmと縦0.9 mmであった。き裂検出の可否および測定時間の長さは検出器の画素サイズに依存するため、2種類の検出器を準備した。試料AおよびBの測定においてモノクロメータ結晶表面とX線のなす角度は2.26°と2.11°とした。この配置で得られるX線のエネルギーはそれぞれ75 keVと83 keVであり、回折角度はそれぞれ1.51°と1.36°である。非対称因子はそれぞれ2.97と3.44である。図3はX線のエネルギーと測定可能な鉄の厚さを計算した結果である。測定可能な厚さはX線の透過率が1/e(e:ネイピア数)になる厚さとした。試料の対角方向のビームパスであっても測定可能なX線のエネルギーを選択したことが分かる。試料は0.2°ステップおよび0.1°ステップで、0°から180°まで回転させて、各角度ステップにおいて試料の透過像を測定した。透過像の露光時間は8 sと10 sとした。CT測定における試料の回転軸は図2に示すz軸と平行である。表1はこれらの実験条件をまとめたものである。測定条件ごとに測定1-測定4と呼ぶこととする。測定1は実験初期に行ったものであり、実験条件が定まっていない。角度ステップは測定1においては試験的に0.2°としたが、測定2以降は統計精度を向上させるために0.1°とした。測定1における露光時間は検出器が飽和する露光時間とした。測定1以外の測定において、表1に示した露光時間では検出器が飽和することはなかった。統計精度を向上させるためには飽和直前まで溜め込むことが望ましかったが、測定時間が長くなりすぎるため今回の実験では露光時間は10 s程度とした。結晶と試料との距離L1と試料とカメラの距離L2は測定1においては335 mmと350 mmとしたが、シリコン結晶からの散乱線によりスパイクノイズが多数検出されたため、シリコン結晶とカメラの距離(L1+L2)を離す必要があった。試料とカメラの距離L2を長くすると屈折コントラストの影響が強くなるため、L1を長くし測定2以降ではその値を1100 mmとした。
試料の断面像再構成前に測定画像のスパイクノイズをメディアンフィルタで除去し、また、画像を滑らかにするために平均化フィルタを施して、その後再構成を行った。再構成はフィルタードバックプロジェクション法を用いた。
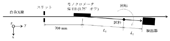
図2. 実験レイアウト(上から見た図).
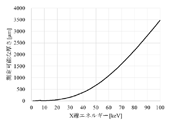
図3. 鉄鋼材料の測定可能な厚さ. 密度7.8 g/cm3として計算した。測定可能な厚さは入射X線の強度が1/eとなる厚さとした。eはネイピア数である。
表1. 実験条件.
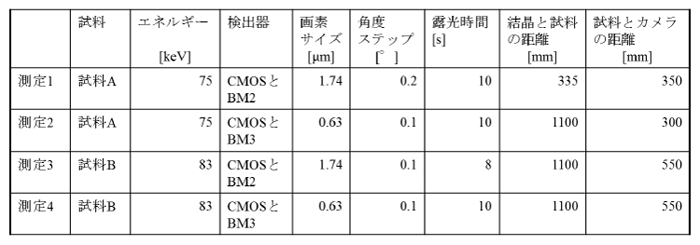
結果および考察:
CTの再構成において、測定した透過像に飽和した画素が含まれていると再構成後の画素の値が正しい値を示さない。従って露光時間は透過像内で最もカウント数が高い部分が飽和しない時間以下で、可能な限り長い(統計精度を高めるため)時間となる。測定した透過像において最もカウント数が高い部分(空気の部分)の値を調べると測定1-4でそれぞれ4000カウント、300カウント、800カウントおよび300カウントであった。今回使用した検出器の最大カウント数は4000カウントであるため、測定1-4の適切な露光時間は、表1に示した露光時間の1倍、13倍、5倍および13倍である。すなわち、10 s、130 s、40 sおよび130 sが適切な露光時間だということが分かった。図4に透過像測定例を示す。これらの画像はCMOSカメラの暗電流画像の減算および試料がない状態で得た入射X線の画像での除算による規格化を行ったものであり(メディアンフィルタと平均化フィルタは施していない)、透過率の分布を示している。明るい色は透過率の高い部分である。図4(a)-(d)はそれぞれ測定1-4においてCTの回転角が0°のときの画像である。図4(b)の四角で囲んだ部分は試料がない部分でのスパイクノイズの存在を拡大して示した例である。図5は図4の試料部分のヒストグラムである。計算上、厚さ0.5 mmの鉄に対する75 keVのX線の透過率と厚さ1.5 mmの鉄に対する83 keVのX線の透過率は、それぞれ0.77と0.52である。測定1、測定3および測定4は概ね良い値を示したが、測定2は値が小さかった。その原因として検出器の交換作業中にシリコン結晶が動いた可能性がある。検出器を動かさなければ、検出器でX線の位置を確認することで回折角度が変わったか否かを判断できるが、検出器を交換する場合は回折角度を丁寧に確認する必要があることが分かった。
ヒストグラムの幅を比較すると、検出器にBM3を用いた測定(測定2と測定4)では幅が広かった。これは露光不足による統計精度の低さが原因である。BM3を用いた検出系は実効画素サイズが小さいため露光時間を長くすべきではあったが、露光時間を長くすると、後述するスパイクノイズが非常に多くなったため長くできなかった。ノイズ対策を行い、露光時間を延ばす工夫が必要である。
図4にはスパイク状のノイズが多く含まれていた。測定画像はX線像を可視光像に変換してCMOSカメラで測定されるべきであるが、これらのノイズは高エネルギーの散乱X線がCMOSカメラに直接入射したことによるものである。X線の散乱源であるシリコン結晶から検出器を離したり、カメラにシールドを施したりしたことでノイズは低減した(図4はノイズ低減後のもの)が、図4(b)の四角で囲んだ部分を見て分かる通りまだ多くのノイズが検出されていた。実験ハッチのサイズや装置のレイアウトの制限のため、今回の実験ではシリコン結晶と試料の距離は最大1100 mmしかとれなかったが、今後の運用では更に距離を離した方が良いと考えている。
図4(c)と(d)は試料Bを観察したものであるが、入射X線の横幅(水平方向の幅)が試料の横幅より小さかった(視野の横幅は入射X線の横幅に合わせて切り出したものである)。入射X線の横幅はモノクロメータに用いたシリコン結晶の長さで決まり、今回の実験では回折面と表面とがなす角度が当初の予定より大きかったため、入射X線の横幅を試料の横幅より大きくすることができなかった。CT測定においては試料の横幅は視野の横幅より小さくしなければ再構成した断面の線吸収係数が正しい値を示さないが、今回の実験ではこのまま実験を実施した。
図6に再構成した断面像の例を示す。断面像の画素値は線吸収係数を示しており、色が明るいほど線吸収係数が小さいことを示している。図6(a)と(b)を見ると、断面0.5 mm × 0.5 mmの鉄鋼材料中のき裂を75 keVのX線を使って観察できたことが分かる。いずれの検出器を用いてもき裂および介在物は検出できており、今回の試料に対しては同じ露光時間でも統計精度が高いBM2を用いた検出器の方が効率的であることが分かった。それぞれの検出器で検出可能なき裂および介在物の下限値の調査は今後の課題とした。
図6(c)と(d)は83 keVのX線を使って断面1.5 mm × 1.5 mmの鉄鋼材料を観察した結果である。中央部分は部分的に材料が剥離した領域であり空隙である。空隙の形状、介在物やき裂を観察することができている。剥離部を含まない断面でも介在物が観察されておりX線の透過長さが1.5 mmを超える鉄鋼材料でも観察可能であることが分かった。
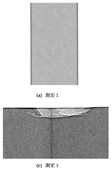
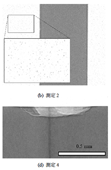
図4. 鉄鋼材料の透過像.
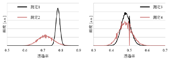
図5. 図4の試料部分のヒストグラム.
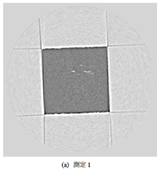
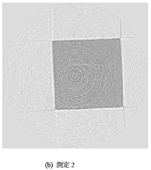
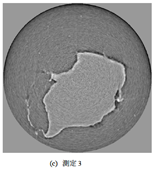
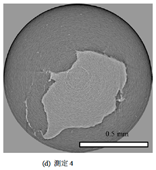
図6. 鉄鋼材料の断面再構成像.
今後の課題:
BL28B2にSi(111)回折で37 keV以上のX線を得るためのモノクロメータを導入した。83 keVのX線を使って断面1.5 mm × 1.5 mmの鉄鋼材料中のき裂や介在物を検出することができた。
今回の実験において、透過像を得るための適切な露光時間は60-120 sであった。この値を目安に実験に必要な時間を検討することができる。
ユーザー実験へ提供するためには「検出可能なき裂サイズの下限値」および「時間に対するX線の強度およびエネルギーの安定性」を評価する必要があり、また、ノイズ対策もさらに強化する必要があることが分かった。
参考文献:
[1] T. Makino, Y. Neishi, D. Shiozawa, Y. Fukuda, K. Kajiwara, Y. Nakai, Int J Fatigue, 68 (2014), 168–177
[2] 牧野泰三, 根石豊, 中井善一, 塩澤大輝, SPring-8利用研究成果集, 1 (2013), 27-30
[3] 菊田惺志, X線回折・散乱技術〈上〉東京大学出版会
ⒸJASRI
(Received: March 24, 2016; Early edition: June 15, 2016; Accepted: June 24, 2016; Published: July 25, 2016)