Volume4 No.2
SPring-8 Section B: Industrial Application Report
半導体パッケージ用封止樹脂の熱硬化過程における残留応力その場観察
In situ Residual Stress Analysis in Encapsulation Resins for Semiconductor Packaging during Curing Process
住友ベークライト(株)
SUMITOMO BAKELITE CO., LTD.
- Abstract
-
半導体パッケージの長期信頼性を実現する上で、製造時の各過程において発生する熱応力を把握することが重要となる。本研究ではX線回折現象を用いた残留応力評価手法であるsin2ψ法により、樹脂の熱硬化過程において半導体パッケージの樹脂/金属界面に発生する応力のその場観察を行った。その結果、各熱硬化過程における樹脂の熱膨張や冷却収縮、また硬化収縮に伴った応力の変化を観察することに成功した。
キーワード: 残留応力解析、sin2ψ法、その場観察
背景と研究目的:
近年の半導体高性能化および長期信頼性の観点から、半導体保護のための半導体パッケージ用封止樹脂(以下、封止樹脂)には高度な耐熱性、電気絶縁性、熱伝導性、耐湿性が求められている。半導体パッケージは主に熱硬化性の封止樹脂と金属(配線および基板)で構成される複合部材であり、それら異種材料間の弾性率と線膨張率が異なるため、半導体パッケージ製造工程における封止樹脂の成形および熱硬化、半田リフローなど加熱処理に伴い、材料界面に熱応力が発生する。更に、複数の加熱冷却過程を経ることによりその応力が樹脂と金属界面に残留応力として蓄積し、半導体パッケージの歪みや反りの要因となる。それらは、界面の密着性に影響を与え、最終的には剥離という半導体パッケージにおける致命的な不良につながる。そこで半導体パッケージ製造の各工程において発生する熱応力をその場観察し、残留応力発生メカニズムを把握することができれば、プロセス改善による封止樹脂と金属界面の残留応力制御が可能となり界面密着性向上が期待される。すなわち、次世代封止樹脂開発における界面の残留応力の解析と残留応力発生メカニズムの把握は、半導体パッケージの長期信頼性を保障するためにも重要な課題である。非破壊的な異種材料界面の残留応力評価手法としては、金属材料分野で広く用いられているX線回折によるsin2ψ法が有効である[1]。我々はこのsin2ψ法を封止樹脂と金属界面の残留応力解析に適用し、評価技術に一定の目処を付けた(課題番号2014A1767)。
本検討では残留応力発生メカニズムの更なる解明のため、X線回折用試料加熱ステージを用いた熱硬化過程における残留応力その場観察について検討した。
実験:
半導体パッケージにおける封止樹脂/銅基板界面のモデル試料として、銅板(厚さ0.530 mm)上に線膨張係数(CTE)が異なる2種(樹脂①: 銅とのCTE差大、樹脂②: 銅とのCTE差小)の封止樹脂を成形(175°C, 2 min)、20 mm × 20 mm × 0.60 mmの測定試料を得た。X線回折測定はBL19B2のHUBER製多軸回折計を用いて実施し、入射X線エネルギーは25 keV、入射X線ビームサイズは縦0.2 mm × 幅6 mmとし、回折X線は発散角0.1°の受光ソーラースリットを介してシンチレーションカウンターにより計測した。試料揺動は無しとした。試料加熱ステージにはDHS1100 (アントンパール社製)を用い、図3に示す熱プロセスを実施した。残留応力は、NakamaeやNishinoらのsin2ψ法によるエポキシ樹脂/アルミ界面の残留応力解析法を参考に[1-3]、Cu(331)面の回折ピークプロフィールを側傾法により測定し、回折ピークトップはガウス関数フィッティングにより算出した。残留応力計算に用いる銅の弾性率とポアソン比は、各々65 GPa、0.343とした。
結果および考察:
図1に樹脂①の室温におけるCu(331)面の回折ピークプロフィールのオフセット角度(ψ)依存性を示す。いずれのψにおいても明瞭な回折プロフィールが得られ、ψ増加に伴うピークトップ2θの広角シフトが観測された(図中の破線部分)。また、図2に示す2θ−sin2ψプロットが直線状であることから、評価手法および直線の傾きから算出される残留応力の妥当性が確認できた。
図3に封止樹脂/銅板界面の熱硬化過程における残留応力その場観察結果を示す。(a) 成形直後の試料はいずれも圧縮応力を示した。これは、成形時(175°C, 2 min)において樹脂が熱膨張した状態で封止樹脂/銅板界面が形成されるために、室温に戻した際の樹脂熱収縮により銅板側が圧縮されたと考えることで説明できる。また、樹脂①の圧縮応力が樹脂②よりも高い値を示したが、これは銅とのCTE差によるものと推定される。(b) 175°C硬化初期においては圧縮応力が一旦減少した後、増大する傾向が観察された。これは、加熱による樹脂の熱膨張によって圧縮応力が緩和された後、硬化反応進行による樹脂の硬化収縮によって再び圧縮応力が増大したものと推定される。(c) 硬化反応後期では、再び圧縮応力の減少が観察され、特に樹脂①において顕著であった。これは硬化反応が収束し、硬化収縮をもたらした樹脂の架橋構造が緩和したことによるものと推定される。(d) 再び室温に戻す際、150°Cから115°Cへの温度変化の過程で圧縮応力は増大した。これは、いずれの樹脂もこの温度範囲にガラス転移温度(Tg)を有しているため、樹脂のガラス転移がこの応力変化に影響していると推定される。(e) 115°Cから室温に冷却すると圧縮応力は減少し、樹脂②においては引張応力が生じた。(f) 熱硬化反応が完了した樹脂をさらに200°Cまで再加熱した後に室温に戻すと、降温過程において樹脂①と樹脂②はそれぞれ圧縮応力の増加と減少という異なる挙動を示すことなども観察された。
以上より、熱硬化過程における残留応力その場観察によって樹脂の熱膨張や収縮、硬化収縮に伴った応力変化を観察することに成功した。しかしながら特に(d)-(f)の過程における応力変化の挙動は熱収縮だけでは説明ができない。この理由として樹脂のボイド(真空の空洞)や表面形状が応力変化に影響を及ぼしている可能性も考えられる。今後はDSC(示差走査熱量測定)による熱分析やSAXS(X線小角散乱)による高次構造変化観察などとあわせた解析を行うことでそのメカニズム解明を進めたい。
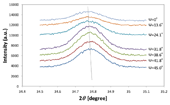
図1 室温時封止樹脂/銅板界面におけるCu(331)の回折ピークプロフィールのψ依存性
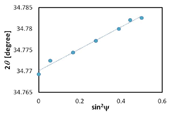
図2 室温時封止樹脂/銅板界面におけるCu(331)の回折ピークプロフィールより作成される2θ−sin2ψプロット
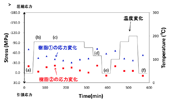
図3 熱硬化過程における封止樹脂/銅板界面の残留応力その場観察結果(1測定当たりの所要時間は40 min)
今後の課題:
本評価手法を用いて残留応力発生メカニズムについて樹脂特性や熱硬化条件の影響を比較することにより、熱プロセスという観点から信頼性向上に寄与する材料や製造条件の最適化が可能となることが期待される。具体的には現行材に対してさらに熱サイクル信頼性が向上した改良材や、成形温度や成形時間、成形圧力が異なる試料を用いて本測定を実施することにより、これらの要因が残留応力の発生メカニズムに与える影響について解明を進めていきたい。
また、今回観察された残留応力の発生メカニズムの更なる解明のため、SAXSやDSCなどとあわせた解析を検討する。なお、本課題の実施にあたり、加熱による変化を考慮した測定範囲・露光時間の最適な条件決定のための検証実験に多くの時間を要したため、当初計画していたフィラー含有率や樹脂厚みが異なる試料の残留応力のその場観察は実施できなかった。これらの検証についても今後の検討課題である。
参考文献:
[1] 田中啓介 他, "放射光による応力とひずみの評価",養賢堂 (2009).
[2] K. Nakamae et al., J. Appl. Polym. Sci., 40, 2231 (1990).
[3] T. Nishino et al., J. Appl. Polym. Sci., 45, 1239 (1992).
ⒸJASRI
(Received: April 15, 2015; Early edition: April 25, 2016; Accepted: June 24, 2016; Published: July 25, 2016)