Volume4 No.1
SPring-8 Section B: Industrial Application Report
摩擦攪拌接合継手に発生した疲労き裂のレーザーピーニングによる進展抑制効果の放射光ラミノグラフィによる検証
Verification of Effect of Laser Peening for Fatigue Crack Propagation in Friction Stir Welded Joints by Laminography
a沖縄工業高等専門学校, b(公財)高輝度光科学研究センター, c大阪大学, d富士重工業(株), eNASA - Johnson Space Center
aOkinawa National College of Technology, bJASRI, cOsaka University, dFuji Heavy Industries Ltd, eNASA - Johnson Space Center
- Abstract
-
アルミニウム合金A6061-T6ならびにA2024-T3の異材摩擦攪拌接合(FSW)継手から平面曲げ疲労試験片を作成し、疲労き裂を導入した試験片を用意した。FSWの適用が期待される車両や航空構造部材などでは、き裂の発生を許容する損傷許容設計が適用されており、発生した疲労き裂の進展抑制が重要となる。そこで本研究ではレーザーピーニング(以下、LP)に注目した。疲労き裂先端にLPを施し、ビームライン脇に仮設した曲げ疲労試験機を使用してき裂を進展させるとともに、ラミノグラフィにより内部のき裂形状を逐次可視化することで、処理による疲労き裂進展 の抑制効果を調査した。ラミノグラフィによって、表面だけでなく試験片内部においてもき裂成長が抑制されること、さらにピーニング条件によって抑制効果が異なることを確認した。
キーワード: 摩擦攪拌接合,アルミニウム合金,疲労,き裂進展,ラミノグラフィ,レーザーピーニング
背景と研究目的:
摩擦攪拌接合(Friction Stir Welding; FSW)は従来の溶接と異なり、溶融温度以下で軟化した材料を局所的に攪拌して接合する新しい接合法である[1]。FSWは接合温度が低く入熱が少ないため、継手効率が高く接合後の変形が小さい。このため、アルミニウム合金を中心として長尺薄肉構造物(鉄道車両のボディ,航空機の胴や翼など)への適用が広がっている[2,3]。FSW接合部は攪拌の状況を反映した特異な組織となり、疲労き裂の発生や進展がその組織に影響されるため、従来の溶接継手とは異なる複雑なき裂進展挙動を示すことが知られている[4]。
2011A期および2011B期ではラミノグラフィの原理を確認するとともに、継手表面および内部のき裂形状が再現できることを確認した[5,6]。2012A期および2012B期では小型の平板曲げ疲労試験機をビームライン脇に仮設し、アルミニウム合金A6061-T6どうしを接合した共材FSW継手について、破断寸前までの疲労き裂の進展挙動を非破壊で可視化した[7,8]。続いて、2013B期では、2種類のアルミニウム合金(A6061-T6とA2024-T3)をFSW接合した異材FSW継手を用意し、き裂発生・進展挙動の可視化と、接合部分の試験片内部における組織の攪拌状況の可視化に成功した[9]。2014A期ではドリル穴を付与せず、疲労き裂の発生から進展・破壊に至るまでのき裂進展挙動について、攪拌組織とき裂の同時可視化を行うことを目標に、現在解析を続けている[10]。
FSW接合材の適用が期待される航空機部材においては、疲労き裂の発生を許容する損傷許容設計が行われており、疲労き裂の進展抑制が重要となる。本研究では、そのき裂進展抑制手法として、LPの適用を試みることとした。LPは疲労特性改善手法の一つであるが[11-17]、きめ細やかな 処理条件が設定できるうえに局所的な施工も可能であることから、き裂先端近傍に施工することでき裂の進展抑制効果が期待できる。しかし実用化の前には、き裂進展抑制効果の定量的な評価が必要である。
そこで本研究では、予き裂を付与した試験片のき裂先端にLPを施し、ラミノグラフィにより試験片内部のき裂進展抑制効果について明らかとするとともに、その進展抑制効果の定量的評価を試みる。
実験方法:
1. 試験片の作製
供試材には、市販の厚さ3 mmのAl-Mg-Si系アルミニウム合金A6061-T6と、Al-Cu-Mg系合金A2024-T3を突き合わせ摩擦攪拌接合した異材FSW継手を用いた。これは過去の一連の研究と同一素材である[5-17]。また、両材の0.2%耐力はほぼ同等の約320 MPaである。FSW継手は汎用フライス盤と、M4の逆ネジが切られた長さ3 mmのピンを有するφ12 mmのツール(異材用)を使用して作製した。接合条件はツール回転数1400 rpm,前進角3度,送り速度41 mm/minである。異材の接合にあたっては、前進側にA2024を配置し、後進側にA6061を配置した。疲労試験片は、図1に示すようにFSW継手材からワイヤ放電加工により採取したが、その際に継手中心と試験片中心が一致するように配慮した。その後、ツール走査痕をフライス加工によって除去するとともに、試験片の表面と裏面、そして側面をエメリ研磨とバフ研磨により鏡面仕上げとした。接合部中心(試験片中心)には直径0.3 mm,深さ0.3 mmのドリル穴をあけ、平板曲げ疲労試験機を使用して応力振幅120 MPa,完全両振り(応力比R = -1),室温・大気中,負荷繰り返し速度22 Hzの条件で疲労負荷を与え、長さ約6 mmの疲労予き裂を付与した。その後、き裂の進展を抑制するため、従来のナノ秒パルスレーザーによるLP処理と、近年新しく開発されたフェムト秒LP処理をそれぞれき裂先端付近に施した。試験片の概略を図2に示す。
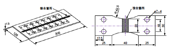
図1. 疲労試験片の採取位置(左)と疲労試験片の寸法・形状(右)
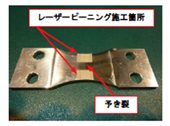
図2. 試験片外観
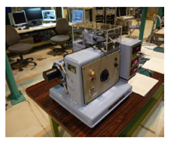
図3. 平板曲げ疲労試験機外観
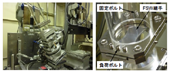
図4. 試験片ホルダー外観(左)と試験片固定部分(右)
2. き裂の可視化試験
LP施工後には、図3に示したビームライン脇に仮設した平板曲げ疲労試験機(PBF-30X)を用いて、応力振幅120 MPaの曲げ疲労負荷を与えてき裂を進展させた。1.0×104 回の疲労負荷ごとにラミノグラフィによる観察と従来のレプリカ法による観察を行い、き裂の進展挙動を非破壊で観察した。ラミノグラフィは産業利用ⅠビームラインBL19B2の第1実験ハッチで行った。試験片の固定には図4に示す試験片ホルダーを使用し、き裂の観察を容易にするために試験片に曲げ負荷を与えることでき裂をわずかに開口させた[5-10]。測定レイアウトを図5に示す。試験片の回転軸を鉛直から30度傾けることを除けば、CTと同一の実験レイアウトである。X線エネルギーは28 keV,試験片とX線カメラの距離は0.8 m,検出器の実効的なピクセルサイズは5.7 µmである。また透過像のカメラ視野は水平方向11.2 mm,垂直方向4.9 mmとした。微細な疲労き裂を観察するためには高い解像度が必要であるが、ラミノグラフィの視野は限られるため、一度にき裂全体を調査することができない。このため、き裂方向に2 mmずつ視野をずらした測定を9回繰返し、き裂全体を観察した。ステージを一定速度で回転させながら360度にわたる投影データを連続的に取得した。また、アクリルパイプのみの投影データの取得は、連続回転スキャンの前後にのみ実施した。1視野の測定時間は約7分であった。
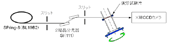
図5. ラミノグラフィ測定レイアウト(BL19B2第1実験ハッチ)
実験結果:
1. 表面における疲労き裂進展抑制確認
表面き裂を従来のレプリカ法により観察した結果を図6(a)に示す。予き裂導入後、フェムト秒およびナノ秒のLP処理を実施し、施工直後、120 MPaの負荷応力振幅で1.0×104 回,2.0×104 回,3.0×104 回および4.0×104 回の疲労負荷を与えたときの表面き裂観察結果である。LP条件の違いにより、その後のき裂進展挙動が明らかに異なっている。この表面き裂の進展挙動について、表面き裂長さと負荷繰返し数の関係で示したものが図6(b)である。き裂長さ6 mmまでが予き裂導入までのき裂進展曲線、6 mm以降がLP施工後のき裂進展曲線である。予き裂導入までのき裂進展曲線が試験片により大きく異なるが、LP施工によるき裂進展抑制効果の調査に対しては影響しない。LP施工後のき裂進展挙動に着目すると、ナノ秒LP施工材の表面き裂の進展速度が明らかに速くなっている。一方のフェムト秒LP施工材では、施工後に疲労き裂がほとんど停留している。このレプリカ法による表面き裂観察では、試験片内部のき裂形状に関する情報が得られないため、ラミノグラフィによる内部の観察を行った。
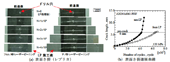
図6. レプリカ法による表面き裂進展挙動
2. ラミノグラフィによる試験片内部のき裂観察
異材FSW継手に対して、フェムト秒LP処理ならびにナノ秒LP処理を施した場合の、ラミノグラフィによる試験片内部のき裂観察結果の例を図7に示す。再構成像の上側が密度の大きいA2024(Al-Cu-Mg系),下側が密度のより小さいA6061(Al-Mg-Si系)である。レプリカ法による表面観察と同様に、LP施工直後、疲労負荷を1.0×104 回,2.0×104 回,3.0×104 回付与した後の試験片について、試験片表面近傍,表面下約170 µm,表面下約340 µmの位置における断層撮影像である。なお、4.0×104 回付与後のき裂観察は行っていない。なお、現在までにすべての再構成が終わっているわけではないので、ドリル穴を含めたき裂の一部分だけを示している。試験片表面近傍のスライス像には、疲労予き裂を導入するために付与したドリル穴(直径0.3 mm)から、疲労き裂が成長しているのが確認できる。また、き裂先端にはLP施工痕も確認できる。それぞれの試験片で、スライス像上部(FSW施工時の前進側)に輝度値の高い領域が確認される。この領域は、X線を透過しにくいCu元素を含むA2024材のCuリッチな層であり、ラミノグラフィによって異材継手の組織攪拌状況まで可視化できることを示している。
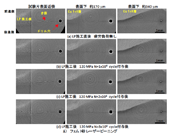
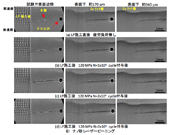
図7. ラミノグラフィによる疲労き裂観察結果例
き裂の進展抑制効果に着目すると、120 MPaの応力振幅を2.0×104 回付与したならば、LPを施工していない場合には、LP施工前のき裂先端位置(すなわち施工端)から全長で1.6 mm程度、つまり片側で0.8 mm程度成長することが事前の調査からわかっている。しかし、フェムト秒LP処理を施工すると、試験片内部も含めてき裂進展がほぼ抑制されている。一方、ナノ秒LP処理を施工すると片側で1 mm程度の成長が認められ、予想に反してき裂進展を加速させる結果となった。この違いは、LP施工により付与された残留応力の影響によるものと考えられる。今後、ラミノグラフィデータの解析をすすめ、き裂全体像について検討を行っていく。
結論および今後の課題:
アルミニウム合金A6061-T6とA2024-T3を用いた摩擦攪拌接合(FSW)継手試験片に、曲げ疲労負荷による予き裂を導入し、き裂先端近傍にLP処理を施した。処理に伴うき裂進展抑制効果の定量的評価を行うために、ラミノグラフィによる疲労き裂形状の可視化を行った。試験片に付与した予き裂の進展挙動は、LPによって付与される圧縮残留応力の影響を受けて、変化することが示唆された。また、ラミノグラフィによって、摩擦撹拌により生じた組織の流動の痕跡も可視化できた。
今後、今回の実験データの詳細な解析をすすめてき裂先端の応力拡大係数を算出し、LPにより生じた圧縮残留応力の影響を定量的に評価する。しかし、まだ試験途中であることから、今回導入したき裂によって試験片が最終破断に至るまでの過程も調査し、き裂の進展経路と撹拌組織との関係までも含めた調査が必要である。本件に関しては、今後検討すべき課題である。この課題を行うことによって、本研究がFSWプロセスの改善や最適化、航空機などの予防保全技術としてのLP処理の有効性を示す重要な成果となるであろう。
参考文献:
[1] R.S. Mishra and Z.Y. Ma: Friction stir welding and processing, Mater. Sci. Eng. R, 50, 1-78 (2005).
[2] 森久史, 他: 鉄道車両への摩擦攪拌接合の適用の現状, 軽金属, 57, 506-510 (2007).
[3] 武久浩之: 航空機用アルミニウム合金のFSW技術, 軽金属, 56, 178-183 (2006).
[4] O. Hatamleh, et al.: Mater. Sci. Eng. A, 519, 61-69 (2009).
[5] 佐野雄二, 他: 平成23年度 重点産業利用課題成果報告書 (2011A), 2011A1685.
[6] 佐野雄二, 他: 平成23年度 重点産業利用課題成果報告書 (2011B), 2011B1861.
[7] 佐野雄二, 他: 平成24年度 産業利用課題成果報告書 (2012A), 2012A1274.
[8] 佐野雄二, 他: 平成24年度 重点産業化促進課題報告書 (2012B), 2012B1740.
[9] 佐野雄二, 他: 平成25年度 重点産業化促進課題報告書 (2013B), 2013B1863.
[10] 佐野雄二, 他: 平成26年度 産業新分野支援課題報告書 (2014A), 2014A1700.
[11] 政木清孝:レーザーピーニングによる疲労特性の改善, レーザー研究, 42, 457-461 (2014).
[12] Y. Sano et al.: Mater. Des., 36, 809-814 (2012).
[13] K. Masaki, et al.: Proc. Int. Joint Symp. on Join. Weld. (IJS-JW 2013), 419-423 (2013).
[14] Y. Sano et al.: Advanced Materials Research., 891-892, 969-973 (2014).
[15] 政木清孝, 他: 日本材料学会信頼性・破壊力学合同シンポジウム講演論文集, 306-311 (2013).
[16] 政木清孝, 他: 日本材料学第63期日本材料学会学術講演会講演論文集, No.306 (2014).
[17] 政木清孝, 他: 日本材料学会第32回疲労シンポジウム講演論文集, 232-235 (2014).
ⒸJASRI
(Received: April 24, 2015; Early edition: August 25, 2015; Accepted: December 11, 2015; Published: January 25, 2016)