Volume4 No.1
SPring-8 Section B: Industrial Application Report
塗装レス高輝度(メタリック)樹脂成形における色ムラの原因解明
Elucidation of the Uneven Color in Injection Molding of Plastics with Metallic Colors
a群馬県立群馬産業技術センター, b(株)柴田合成, c豊橋技術科学大学, d九州大学
aGunma Industrial Technology Center, bShibata Gosei Co.,Ltd, cToyohashi University of Technology, dKyushu University
- Abstract
-
自動車等のプラスチック部品においては、メタリック樹脂を使用した成形では、形状の変化による高輝度粒子の乱れや、開口部後の樹脂の合流地点に発生するウェルドラインとは別の高輝度粒子同士の溝が発生する。この現象は、輝度感が失われるだけでなく、外観不良になるが、外観やワークの切断による断面観察だけでは高輝度粒子の配向を評価することは難しい。SPring-8のシンクロトロン放射によるX線CTにより高分解能な三次元データ化により、スキン層を含む表面から100 μm以内の範囲の高輝度粒子の配向と高輝度粒子同士の溝との相関を明らかにした。
キーワード: メタリック樹脂成形、高輝度粒子、イメージング
1.背景と研究目的:
自動車等の部品に高品質外観を得るために高輝度(メタリック)の塗装を施すのが一般的であるが、塗装はコストを押し上げる主要因であり、揮発性有機化合物を発生するため、環境にも悪影響を及ぼす[1]。この課題に対して、我々はおおよそ5 μm×5 μm、厚み1 μmの小判状の高輝度粒子を混合したメタリック樹脂を使用し、環境問題やコスト問題を解決しつつ、メタリック感のある外観の樹脂成形品の実現を目指している。メタリック樹脂を使用した成形では、図1に示すように、開口部後の樹脂の合流地点では高輝度粒子の向きが表面に対して傾斜により、ウェルドラインとは別の高輝度粒子同士の溝(以下、ブラックライン)が発生する。この現象が発生すると特有の輝度感が失われるだけでなく、図2に示すように外観不良となることが知られている。
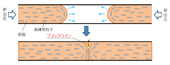
図1 ブラックラインの発生メカニズム
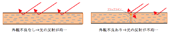
図2 高輝度粒子と向きと外観不良
我々は、ウェルドレス成形システムを発展させたメタリック成形により、このブラックラインの軽減に取り込んできた。これまでの研究は、外観やワークの切断による断面観察から生成条件や機構に関する研究を行ってきた[2]。しかしながら、ブラックラインと高輝度粒子の配向の相関を見いだすに至らず、製品化には成形品内部の高輝度粒子の配向状況や分布を系統的に評価することを迫られている。
本研究では、樹脂内部の高輝度粒子の三次元的な配向の解析を行う目的で、大型放射光施設SPring-8のシンクロトロン放射によるX線CTにより、ブラックラインを含む樹脂成形品の撮像を行った。
2.実験:
2.1 実験装置:
高輝度粒子は粒径5〜10 μmの小判形状で厚みが非常に薄く、一般的な産業用X線CTでは観察が難しい。そこで、SPring-8のシンクロトロン放射を用いた高分解能(1 μm 以下)なX線CTにより、ブラックラインを含む樹脂成形品の撮像を行った。測定に使用したビームラインはBL20XUである。測定に使用した条件は以下のとおりである。
ビームライン:BL20XU
入射光形状:Box状
X線エネルギー:8 keV
検出器の型式:Beam Monitor 3 + ORCA-Flash4.0
観察視野範囲の寸法:約1 mm×1 mm
画素数 2048×2048
露光時間 0.15 s
試料を180°回転させながら1800枚の透過画像を取得し再構成を行った。再構成画像は2048×2048 pixel、VOXELサイズは0.5 μmである。VG Studio MAX 2.2(VOLUME GRAPHICS社製)により、ボリュームデータ化し高輝度粒子の配向の解析を行った。
2.2 試験片の形状:
内部の高輝度粒子の配向を観察するため、高輝度粒子を混合したメタリック樹脂を使用し、金型表面温度を80°Cとした通常成形品(PP,通常成形)のブラックライン部分を切り出してワークを作成した。切り出した箇所を図3に示す。ブラックラインをX-Z面にとるように、各の軸を決める。
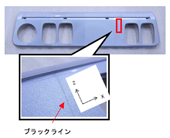
図3 ワークの切り出し箇所(ブラックライン)
図3の写真にある試料表面においてブラックラインに平行な方向がZ軸、垂直な方向がX軸。
Y軸は試料面に垂直で表面から底面に向かう方向である。
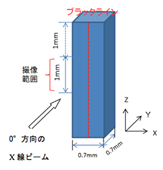
図4 ワークの撮像範囲
ワークサイズは視野幅に入る最大の大きさである0.7×0.7×5.0 mmの直方体で、撮像範囲は図4に示すように上端面の1 mm下から、長さ1 mmとし、ブラックラインが確認される面を0°方向とした。0°方向でのX線ビームは、図4に示すとおりである。同様にして、ウェルドレス成形システムにより、金型表面を150°Cに設定したワークも用意した(PP,ウェルドレス成形)。
3.結果および考察:
PP,通常成形およびPP,ウェルドレス成形のマイクロスコープによる表面の拡大撮影を行った。PP,通常成形の結果を図5に、PP,ウェルドレス成形の結果を図6に示す。マイクロスコープはVHX-1000(KEYENCE社製)を使用し、倍率は1000倍で観察を行った。PP,通常成形には、ブラックラインが確認できる。このブラックラインの原因は高輝度粒子の配向の乱れと考えられるが、CTによる断面画像から、高輝度粒子の配向を、金型面(XZ平面)から、深さ方向(Y軸)に対する高輝度粒子の配向の解析を行った。
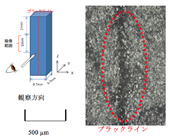
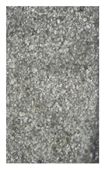
図5 表面観察(PP,通常成形) 図6 表面観察(PP,ウェルドレス成形)
PP,通常成形およびPP,ウェルドレス成形のX線CTによる断面画像から作成したボリュームデータを図7、8に示す。
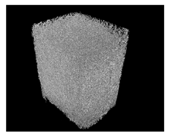
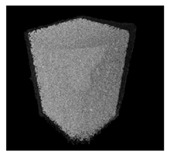
図7 ボリュームデータ(PP,通常成形) 図8 ボリュームデータ(PP,ウェルドレス成形)
図7、8に示したボリュームデータでは、成形内部の高輝度粒子の配向状況を明らかにすることが困難であるため、画像処理にて広く使用される構造テンソル解析により、各平面投影におけるローカル高輝度粒子を求めた。成形の金型に接する面をXZ平面とし、その法線ベクトル方向をY軸にとる。全データをY軸方向へ投影・演算し、Y軸に対する角度(配向)をコンターで表示し高輝度粒子の配向の可視化を行った。実際のワークの幅は上記のサイズよりもやや大きく切り出しているので、PP,通常成形とPP,ウェルドレス成形の関心領域を0.7×0.7×1.0 mmと統一した。断面画像上の緑の枠は関心領域を示す。
CTによる断面画像から、ブラックラインが観察されたPP,通常成形について、XZ平面の高輝度粒子の配向がY軸に対して180°にそろうY軸方向の深さを求めた。結果を図9に示す。Y= 0 μmでは、Y軸に対して140°〜180°と高輝度粒子の乱れが確認されたが、Y= 100 μmでは高輝度粒子のY軸に対して角度は180°と表面に平行に配向していることが分かった。
同様に、ブラックラインが軽減されたウェルドレス成形のXZ平面の高輝度粒子の配向の評価を行った。金型に接する面(Y= 0 μm)位置の高輝度粒子の配向、Y= 100 μmの位置の高輝度粒子の配向を図10に示す。ウェルドレス成形では、金型に接する面からのY軸方向0〜100 μmにおける高輝度粒子の配向の角度は180°と表面に平行した配向であることが分かった。
これらの結果から、外観不良と認識されるブラックラインは、成形表面のスキン層および表面からごく浅いエリア(〜100 μm)の配向の乱れに起因し、これ以上深いコア層の高輝度粒子の配向の乱れの影響を受けにくいことが明らかになった。ウェルドレス成形は金型表面を通常成形時の表面温度80°Cと比較し、150°Cと高温加熱することにより、成形表面を一時的に溶融、再流動させることにより高輝度粒子の配向の乱れの低減と、外観不良を改善させることが示唆された。
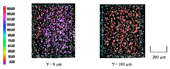
図9 高輝度粒子の配向(PP,通常成形)
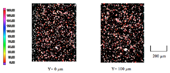
図10 高輝度粒子の配向(PP,ウェルドレス成形)
4.今後の課題:
大型放射光施設SPring-8のシンクロトロン放射によるX線CTを利用することで、メタリック成形中の粒径5〜10 μmといった微細な高輝度粒子の観察が可能であり、ボリュームデータからの全データを利用し、全データをY軸方向へ投影・演算し、角度をコンターで表示し高輝度粒子の配向の可視化した。
今回の結果により、ブラックラインがスキン層を含む成形表面近傍の高輝度粒子の配向の乱れに起因する現象と諷喩されたため、軽減のためには(株)柴田合成製の温度制御可能なウェルドレス成形システムにより、成形表面を一時的に溶融、再流動させるための基礎的なデータが採取されたことにより、金型温度をはじめとする成形条件の最適化の効率化が図られ、メタリック成形の実用化に向けた取組が飛躍的に進展するものと思われる。
謝辞::
本研究は、経済産業省の平成22年度戦略的基盤技術高度化支援事業により遂行されたものであることを記し、ここに深く謝意を表します。
参考文献:
[1] 須田、黒岩、福島、小宅、小林、高岡、寺内:成形加工’12, 79(2012)
[2] 須田、黒岩、福島、小宅、高岡、寺内:プラスチック成形加工学会誌「成形加工」第27巻第3号 論文(2015)
ⒸJASRI
(Received: July 23, 2015; Accepted: December 11, 2015; Published: January 25, 2016)