Volume3 No.2
SPring-8 Section B: Industrial Application Report
摩擦攪拌接合継手における疲労き裂進展挙動のラミノグラフィによる非破壊観察
Nondestructive Observation of Fatigue Crack Propagation Behavior in Friction Stir Welded Joints by Laminography
a(株)東芝, b沖縄工業高等専門学校, c(公財)高輝度光科学研究センター, d大阪大学, e富士重工業(株), fNASA - Johnson Space Center
aToshiba Corporation, bOkinawa National College of Technology, cJASRI, dOsaka University, eFuji Heavy Industries Ltd, fNASA - Johnson Space Center
- Abstract
-
アルミニウム合金A6061-T6の摩擦攪拌接合(FSW)継手試験片に曲げ疲労によりき裂を導入し、その形状をラミノグラフィにより可視化した。更に、ビームライン脇に仮設した曲げ疲労試験機を使用してき裂を進展させ、その様子を非破壊で観察した。FSWの使用が期待される大型の板状構造物の場合にはCTの適用は困難を伴うが、ラミノグラフィの適用は原理的に可能であり、微細な疲労き裂やその進展を非破壊で観察することができた。また、FSW組織に特有と思われるき裂の屈曲などの現象を確認した。
キーワード: 摩擦攪拌接合,アルミニウム合金,疲労,き裂進展,ラミノグラフィ
背景と研究目的:
摩擦攪拌接合(Friction Stir Welding; FSW)は従来の溶接と異なり、溶融温度以下で軟化した材料を局所に攪拌して接合する新しい接合法である[1]。FSWは接合温度が低く入熱が少ないため、継手効率が高く接合後の変形が小さいという特徴がある。このため、アルミニウム合金を中心として長尺薄肉構造物(鉄道車両のボディ、航空機の胴や翼など)への適用が広がっている[2,3]。FSW接合部は攪拌の状況を反映した特異な組織となり、疲労き裂の発生や進展がその組織に影響されるため、従来の溶接継手とは異なる複雑なき裂進展挙動を示すことが知られている[4]。
本研究は、放射光を光源としたラミノグラフィによりFSW継手に生じた微細な疲労き裂を非破壊で可視化し、その進展挙動を明らかにすることを目的としている。2011A期および2011B期の実験ではラミノグラフィの原理を確認するとともに、深さが異なる一連のスライス像を再構成することにより継手表面および内部のき裂形状が再現できることを確認した[5,6]。2012A期の実験では小型の平板曲げ疲労試験機をビームライン脇に仮設し、疲労き裂の進展の様子を非破壊で観察した[7]。今回は、前回と同一の試験片を使用して破断寸前まで疲労試験を継続し、一連のき裂進展試験を完了した。
実験方法:
1. 試験片の作製
供試材には厚さ3 mmのAl-Mg-Si系展伸用アルミニウム合金A6061-T6圧延材を使用した[8-14]。供試材の化学組成を表1に示す。FSW継手は汎用フライス盤とM4の逆ネジが切られた長さ3 mmのピンを有するφ10 mmのツールを使用して作製した。接合条件はツール回転数1400 rpm,前進角3度,送り速度41 mm/minである。A6061-T6母材とFSW継手の機械的性質を表2に示す。
疲労試験片はFSW継手からワイヤ放電加工により図1に示すように採取した。試験片表面のツール走査痕はフライス加工によって除去し、表面と側面をエメリ研磨とバフ研磨により鏡面に仕上げた。FSW接合部の中心(試験片中心)には直径0.3 mm,深さ0.3 mmのドリル穴をあけ、平板曲げ疲労試験機を使用して応力振幅120 MPa,完全両振り(応力比R = -1),室温・大気中,負荷繰り返し速度22 Hzの条件で試験片に2 × 105回の疲労負荷を与え、長さ約3.2 mmの疲労予き裂を付与した。
表1.供試材(A6061-T6)の化学組成 [重量%]

表2.A6061-T6母材およびFSW継手の機械的性質

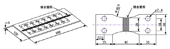
図1. 疲労試験片の採取位置(左)および疲労試験片の寸法・形状(右)
2. き裂の可視化試験
ラミノグラフィによる疲労き裂の可視化試験はSPring-8の産業利用ⅠビームラインBL19B2の第1実験ハッチで行った。測定レイアウトを図2に示す。試験片の回転軸を鉛直から30度傾けることを除けば、CTと同一のレイアウトである。X線エネルギーは28 keV,試験片とX線カメラの距離は0.8 mとした。検出器の実効的なピクセルサイズは5.6 µm,視野は水平方向11.2 mm,垂直方向4.3 mmである。
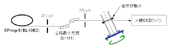
図2.ラミノグラフィ測定レイアウト(BL19B2第1実験ハッチ)
疲労き裂は通常では閉口しているため、図3に示す試験片ホルダーにより試験片に曲げ負荷を与え、き裂をわずかに開口させた[11-14]。投影データは0.5度刻みで全周にわたって取得した。10度毎にステージを上下させてアクリルパイプのみの投影データを取得し、アクリルパイプによるX線の減衰を補正した。
微細なき裂を観察するためには高い解像度が必要であり、ラミノグラフィの視野は限られる。このため、き裂が進展すると単一の視野ではき裂全体を捉えることができない。そこで、図3右に示すように分割した測定を繰返し、再構成後の画像を繋ぎ合わせることにより、き裂の全体像を作成した。
ビームライン脇には図4に示す平板曲げ疲労試験機PBF-30X(テークスグループ社製)を仮設し、試験片に応力振幅120 MPaの曲げ疲労負荷を与えてき裂を進展させた。き裂進展の途中でラミノグラフィによる観察を繰り返すことにより、疲労き裂の進展を非破壊で観察した。疲労負荷により試験片に作用する応力は図3右のY方向であり、均質な組織の場合にはき裂はX方向に成長することが知られている。
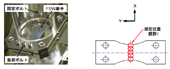
図3.試験片ホルダー(左)と試験片の測定位置(右)
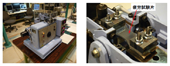
図4.平板曲げ疲労試験機PBF-30X(左)と試験片の取付け状況(右)
実験結果:
ラミノグラフィにより得られた試験片表面のき裂像を図5に示す。(b)~(g)は複数の視野の再構成像を繋ぎ合わせることによって作成した。疲労負荷回数は左から(a)2.00 × 105 回,(b)2.50 × 105 回,(c)2.75 × 105 回,(d)3.00 × 105 回,(e)3.25 × 105 回,(f)3.37 × 105 回,(g)3.42 × 105 回であり、(a)~(c)が2012A期の結果、(d)~(g)が今回の結果である。各々の画像から算出したき裂長さは光学顕微鏡で観察したき裂の長さとほぼ一致した。従って、ラミノグラフィによる画像再構成および複数視野の繋ぎ合わせは適切に行われたと考えられる[5,6]。なお,各画像の中心付近の穴は初期き裂を導入するためのドリル穴(直径0.3 mm)である。
(a)から(d)のき裂進展初期においては、疲労負荷を与えるに従ってき裂は試験片表面をほぼ円弧状に進展していることがわかる。その曲率半径は7 mm程度であり、FSWツール(半径5 mm)の回転による材料の塑性流動の範囲に関連すると思われる。(e)以降はき裂が大きく屈曲しながら進展し、(f)では試験片の端面から進展してきたき裂と合体している。
結論および今後の課題:
アルミニウム合金A6061-T6の摩擦攪拌接合(FSW)継手試験片に曲げ疲労によりき裂を導入し、その形状をラミノグラフィにより可視化した。ビームライン脇に曲げ疲労試験機を仮設し、疲労負荷によるき裂進展とラミノグラフィを交互に繰り返すことにより、FSW継手の疲労き裂進展の様子を非破壊で観察した。FSW継手では、疲労き裂の進展はその組織に依存して複雑な挙動を示すと言われている。2012A期の実験では緩やかな円弧状のき裂進展が観測され、均質な母材で一般的な直線状のき裂進展とは異なる様子が観察されていた。今回は2012A期と同一の試験片に対して破断寸前まで試験を継続した。その結果、複雑な屈曲を示す特異なき裂進展の様子が観察され、本実験の目的を達成した。
今後は、データ解析を進めてき裂の三次元的な形状を把握するとともに、組織とき裂進展との関係の把握,複数の試験片に対する再現性の確認などを行い、FSW継手におけるき裂進展のメカニズムを検討する計画である。また、き裂の進展を抑制するための接合条件や残留応力分布,レーザーピーニングなどの表面処理の効果などについても検討を行う。
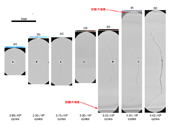
図5.FSW継手試験片表面の再構成像
参考文献:
[1] R.S. Mishra and Z.Y. Ma: Friction stir welding and processing, Mater. Sci. Eng. R, 50, 1-78 (2005).
[2] 森久史, 他: 鉄道車両への摩擦攪拌接合の適用の現状, 軽金属, 57, 506-510 (2007).
[3] 武久浩之: 航空機用アルミニウム合金の FSW 技術, 軽金属, 56, 178-183 (2006).
[4] O. Hatamleh, et al.: Mater. Sci. Eng. A, 519, 61-69 (2009).
[5] 佐野雄二, 他: 平成23年度 重点産業利用課題成果報告書 (2011A), 2011A1685.
[6] 佐野雄二, 他: 平成23年度 重点産業利用課題成果報告書 (2011B), 2011B1861.
[7] 佐野雄二, 他: 平成24年度 産業利用課題成果報告書 (2012A), 2012A1274.
[8] 山城研二, 他: 日本機械学会2010年度年次大会, S305-1-5, 2010年9月.
[9] K. Yamashiro et al.: Technical digest of 3rd Int. Conf. on Laser Peening and Related Phenomena (2011). http://www.mapse.eng.osaka-u.ac.jp/3rdLP/img/digest.pdf
[10] Y. Sano et al.: Mater. Des., 36, 809-814 (2012).
[11] 政木清孝, 他: 日本機械学会 M&M2011カンファレンス, OS0510, 2011年7月.
[12] 政木清孝, 他: 日本機械学会 2011年度年次大会, G030131, 2011年9月.
[13] 政木清孝, 他: 日本機械学会 2012年度年次大会, G030051, 2012年9月.
[14] 政木清孝, 他: 日本材料学会第31回疲労シンポジウム, 2012年11月.
ⒸJASRI
(Received: June 10, 2013; Early edition: April 28, 2015; Accepted: June 29, 2015; Published: July 21, 2015)