Volume3 No.2
SPring-8 Section B: Industrial Application Report
半導体パッケージ用封止樹脂の熱履歴と残留応力の解析
Residual Stress Analysis in Encapsulation Resins for Semiconductor Packaging with Thermal History
住友ベークライト(株)
SUMITOMO BAKELITE CO., LTD.
- Abstract
-
X線回折法による半導体パッケージ用封止樹脂/金属界面の残留応力評価について検討した。本研究では封止樹脂を銅箔上に成形したものをモデル材とし、sin2ψ法による評価を行った。また、有限要素法による応力シミュレーションによりX線回折法で得られた結果の妥当性を検証した結果、応力モードが圧縮応力である点および応力値のオーダーが良い一致を示したことより、本評価手法が有効であることを確認した。
キーワード: 残留応力解析、sin2ψ法、半導体パッケージ
背景と研究目的:
近年の半導体高性能化および長期信頼性の観点から、半導体保護のための半導体パッケージ用封止樹脂(以下、封止樹脂)には高度な耐熱性、電気絶縁性、熱伝導性、耐湿性が求められている。半導体パッケージは主に封止樹脂と金属(配線および基板)で構成される複合部材であり、それら異種材料間の弾性率と線膨張率が異なるため、半導体パッケージ製造工程における封止樹脂の成形および熱硬化、半田リフロ―など加熱処理に伴い、材料界面に熱応力が発生する。更に、複数の加熱冷却過程を経ることによりその応力が樹脂と金属界面に残留応力として蓄積し、半導体パッケージの歪みや反りの要因となる。それらは、界面の密着性に影響を与え、最終的には剥離という半導体パッケージにおける致命的な不良につながる。すなわち、次世代封止樹脂開発において、封止樹脂と金属界面の残留応力の解析と把握は、半導体パッケージの長期信頼性保障のためにも重要な課題である。樹脂と金属材料界面における残留応力を非破壊的に評価する手法としてはX線を利用したsin2ψ法が挙げられる[1]。しかしながら、一般的なCu Kα線を用いた実験室X線装置を用いて半導体パッケージにsin2ψ法を適用する場合、無機フィラーを多量に含有する封止樹脂はX線吸収係数が高いため、金属の回折を精度よく検出できないという課題がある。一方、放射光を用いた残留応力測定では、高エネルギーX線が利用可能であり、封止樹脂中の無機フィラーによるX線吸収を低減可能であるため、残留応力を精度よく解析することが可能であると考えられる。
本課題では半導体パッケージのモデル材料として銅箔上に当社封止樹脂を成形したものを用い、X線回折による封止樹脂と銅界面の残留応力評価の有効性について検討した。また、X線を用いた残留応力解析結果の妥当性検証のため、有限要素法(FEM)を用いたシミュレーションも実施した。
実験:
半導体パッケージにおける封止樹脂/銅配線界面のモデル試料として、銅箔(12 µm)上に封止樹脂を厚さ250, 800, 1100 µmで10 cm × 20 cmのサイズに成型後、225°Cで1時間硬化、2 cm × 2 cmにカットしたものを測定試料とした。成形品の面内バラツキの影響を考慮し、厚さ250 µmでは3種、800 µmおよび1100 µmでは5種の試料片について測定を行い、結果は平均および標準偏差として解析した。硬化前後の残留応力変化の解析のため、厚み800 µmの試料については熱硬化前の試料の測定も実施した。残留応力測定はBL19B2のHUBER製多軸回折計を用いて実施し、入射X線エネルギーは25 keV、入射X線ビームサイズは縦0.2 mm × 幅6 mmとし、回折X線は発散角0.1°の受光ソーラースリットを介してシンチレーションカウンターにより計測した。試料揺動は無しとした。残留応力解析方法はNakamaeやNishinoらによる、エポキシ樹脂/金属界面の残留応力解析法を参考にsin2ψ法を適用し[1-3]、側傾法でオフセット角度(ψ)0, 13.6, 24.1, 31.8, 38.6, 41.8, 45.0°でのCu(3 3 1)面の回折プロフィールを測定した。測定回折角(2θ)の範囲は34.4–35.2°、角度刻み幅0.005°、1角度当たりの露光時間は1秒とした。1試料当たりの測定時間は約40分であった(試料アライメントの時間は除く)。回折ピークトップはガウス関数フィッティングにより算出した。また、上記モデル系についてFEMを用いた封止樹脂と銅箔界面に発生する残留応力のシミュレーションを行い今回の測定結果との比較を行った。sin2ψ法による残留応力計算においてはCuの物性データとして弾性率は65 GPa、ポアソン比は0.343を用いた。また、FEMシミュレーションにおいてはCuの物性データは上記と同様の値に加えてCTEは16.8 ppmを用い、封止樹脂の物性データとして、弾性率およびCTEは熱分析・粘弾性測定装置(TMA, DMA)で測定した温度依存性の実験値を用い、ポアソン比は0.370とした。
結果および考察:
図1に封止樹脂厚さ1100 µmの試料においてψを変化させた際のCuの回折ピークプロフィール変化を示す。いずれのψ角においても明確な回折ピークプロフィール、およびψ角増加に伴うピークトップの広角シフトが観測された。また、図2に示す2θ−sin2ψ線図が直線状であることから、本検討の残留応力評価手法の妥当性が確認された。さらに、測定結果の妥当性検証として、図3に各試料のピークトップシフトからsin2ψ法により残留応力値を算出した結果およびFEMシミュレーション結果を示す。
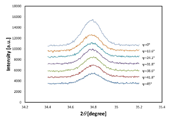
図1 封止樹脂(1100 µm)/銅箔試料におけるCu(3 3 1)の回折ピークプロフィールのψ依存性
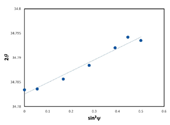
図2 Cu(3 3 1)の回折ピークトップ変化から得られた2θ−sin2ψ線図
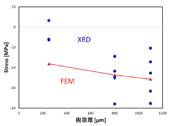
図3 封止樹脂(250, 800, 1100 µm)/銅箔界面の残留応力解析結果
X線で得られた残留応力が圧縮応力であること、およびそのオーダーがFEMの結果とよく一致していることが確認でき、当手法が妥当であることが確認できた。また、樹脂厚み800 µmの試料における封止樹脂/銅箔界面の硬化前後の残留応力の解析結果を表1に示す。この結果から樹脂の硬化前後では明確な差がないことが明らかとなった。
今回、高エネルギーおよび高輝度のSPring-8の放射光X線を用いることでCu Kα線を用いた実験室X線回折装置ではX線吸収の問題で測定不可能であった無機フィラーを含有する封止樹脂においても銅箔の回折ピークが明確に得られ残留応力解析が可能であることが確認できた。またFEMの結果の傾向と良い一致を示すことから測定手法の妥当性も確認できた。一方で本測定の課題として図3から測定のばらつきが大きいことが挙げられるが、これは10 cm × 20 cmサイズの成形品面内ばらつきによるものと推定され、例えば成形圧の面内分布が高次構造の分布ともたらしたことが要因として推定される。一般に、熱硬化性樹脂中にはnm–µmオーダーの空孔が存在し[4]、これらは主に熱硬化過程で発生する揮発性ガスによって形成される。成形圧はこの熱硬化過程で発生する空孔の形成を抑制する効果があるが、成形圧の面内ばらつきが存在すると封止樹脂/銅界面付近の樹脂中の空孔分布が不均一となり、残留応力に影響する高次構造に影響を与えたと推定される。今後はカットサンプルの取り出し位置と残留応力の相関解析、SAXSによる高次構造解析などもあわせて検討し、本要因の解明も進めたい。
表1.封止樹脂(800 µm)/銅箔界面における硬化前後の残留応力解析結果
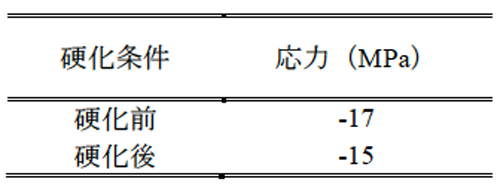
今後の課題:
本課題では半導体パッケージにおける樹脂/金属界面の応力評価手法の確立に成功し、妥当性も確認できた。今後はさらなる長期信頼性材料開発の加速のために、製造プロセス中での残留応力発生メカニズムを解明し界面剥離の要因解明、制御が求められる。そこで課題番号2014B1598では同BL19B2において試料加熱ステージを使用し、熱硬化過程および加熱冷却過程における樹脂/金属界面の残留応力のその場観察を実施する予定である。今回の測定条件を用いることで、1測定当たり約40分でデータ取得が可能であり、数時間オーダーの熱プロセス過程では、本手法の測定速度によりその場観察が実現可能である。本課題の硬化前後のみの応力評価では明らかにできなかった熱履歴にともなう残留応力の変化を評価することにより、界面剥離の発生メカニズムを解明し、製造プロセス改善による長期信頼性材料開発につなげる。なお、本課題の実施にあたり、応力算出に用いる最適な回折ピークの探索、スリット条件、揺動条件、露光時間などの最適な測定条件決定のための検証実験に多くの時間を要したため、当初計画していた金属基板種(Cu, Al)や封止樹脂中のフィラー含有量が残留応力に与える影響についての検証は実施できなかった。これらの検証についても今後の検討課題である。
参考文献:
[1] 田中啓介 et al., "放射光による応力とひずみの評価",養賢堂,(2009)
[2] K. Nakamae et al., J. Appl. Polym. Sci., 40, 2231 (1990).
[3] T. Nishino et al., J. Appl. Polym. Sci., 45, 1239 (1992).
[4] A. Izumi et al., Soft Matter, 8, 8438 (2012).
ⒸJASRI
(Received: October 12, 2014; Early edition: April 28, 2015; Accepted: June 29, 2015; Published: July 21, 2015)