Volume3 No.1
Section B : Industrial Application Report
デバイス実装構造の内部界面における不連続変形の非破壊観察
Nondestructive Measurement of Discontinuous Deformation at Internal Interfaces of Power Device Package
a(株)豊田中央研究所, b(公財)高輝度光科学研究センター
aToyota Central R&D Labs., Inc., bJASRI
- Abstract
-
異種材料の接合体である機械部品やデバイスでは、熱疲労などの損傷は内部で発生する場合が多い。高度な信頼性評価には部品形状のまま内部形態を非破壊計測できるラミノグラフィが有用である。そこで高輝度放射光でデバイス実装構造を計測した結果、数μmの分解能でモールド樹脂部の内部界面に発生する微小き裂の3次元形状を可視化できた。
キーワード: デバイス、信頼性評価、イメージング、ラミノグラフィ
背景と研究目的:
機械部品や電子デバイスは、異なる物性の材料を接合して機能を発現させる用途が大半である。異種材料を接合した部品では、製造時および使用時の温度変化等により、変形や損傷が内部で発生する場合が多い。内部の損傷挙動は、複雑な製造工程履歴や不連続な微視構造などの影響を大きく受けるため、部品のままでの実測が望まれている。市販のX線CTによる内部計測では、実部品サイズでの高分解能な計測は困難で、内部破壊が大きく進展するまで捉えられなかった。また、従来の放射光CTやSEM(走査型電子顕微鏡)等の断面観察では、高分解能観察ができるが、試料を微小に切断する必要があるため、経過観察ができず破壊のメカニズムの考察が困難であった。一方、放射光のラミノグラフィは大サイズの扁平な形状でも内部形状の3次元構築が可能であるため[1]、実部品サイズのまま、実稼働に近い負荷環境下でミクロな内部形態を計測できる可能性がある。これまでにSPring-8でラミノグラフィを試行し、電子デバイス材料の内部形態を可視化する計測条件を得た[2-3]。従来法では観えなかった形態を可視化する一方、破壊メカニズムの解析には更に高い空間および時間の分解能が必要とわかった。そこで、高輝度な光電子分光・マイクロCTビームライン(BL47XU)でラミノグラフィ計測を行い、部品サイズのままで高分解能計測による内部損傷評価の可能性を検討した。
実験:
計測試料には、単純な構成として樹脂複合材料の単体、および複層構成として薄板状のデバイス実装構造の模擬試験片を用いた。樹脂複合材料は、エポキシに平均結晶粒径約20 μmのAl粉末を混合して作成した。試料サイズは約40×13×2 mmとした。デバイス実装構造は、半導体素子、はんだ、配線金属Al、絶縁セラミックスAlNおよび冷却板Al合金をモールド樹脂(SiO2とエポキシ等)で包埋した積層構造であり市販材料を組み合わせて作成した。試料サイズは約φ40×2 mmである。作成後に一般的な使用条件より過大な熱疲労を加えて、内部に損傷を導入した。
計測はBL47XUの自動ステージおよび再構成ソフトを利用して行った。セットアップを図1に示す。試料は入射光に対して30°傾斜させたφステージ上に設置した。撮影にはCMOSカメラを使用し、解像度は約0.6 μm/pixelとした。φステージの回転間隔は0.1°とし、撮影は0.4 秒/枚で行った。波長は、はんだの吸収端を考慮して29 keVとした。なお、デバイス実装構造は参照として熱疲労前の内部形態をBL16B2でも計測した。
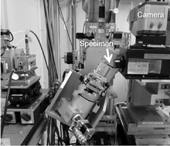
図1 薄板状デバイス実装構造試料のラミノグラフィ計測のセットアップ
結果および考察:
樹脂複合材料の計測結果を図2に示す。図は内部の水平断面を示し、明るい部分がAl、暗い領域がエポキシである。面積が約40×13 mm2の試料のまま厚さ2 mmを透過して、内部に分散する数μmのAl粒子を明確に3次元構築できた。計測領域全体の直径は約1.2 mmである。ラミノグラフィでは大面積の試料を切断せずそのまま計測しているため、本計測を複数個所で行い最終的に統合すれば、広範囲の内部損傷を観察し最弱部位を探索できると考えられる。
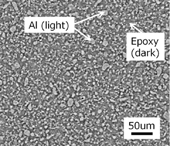
図2 樹脂複合材料(Al+エポキシ)のラミノグラフィ計測結果
デバイス実装構造の計測結果を図3に示す。(a)は計測試料と計測位置の模式図であり、円柱形状で示した計測領域内において、半導体素子の表面と平行な一断面の再構成像を(b)および(c)に示した。(b)は比較のための熱疲労前の計測結果(BL16B2)であり、(c)は熱疲労後の結果(BL47XU)である。(b)および(c)において、各画像の左下約4分の1が素子のエッジであり、周辺は素子を覆っているモールド樹脂(SiO2とエポキシ等)である。(b)では可視化が困難であった数μmのSiO2粒子を(c)では明瞭に可視化できている。熱疲労後は素子のエッジからモールド樹脂内に発生する微小な疲労き裂が観察された。き裂長さは最大で約30 μmであり、素子エッジ周辺のみに観察され、はんだ等の周辺では観察されなかった。再構成の高さが異なる水平断面における同一き裂の画像を右に重ねて示す。SiO2(画像中のグレーの球状領域)の粒径が大きい場合にき裂は粒内を伝ぱするのに対し、小さい粒子の領域では粒子間を伝ぱしている。(d)には、はんだと配線金属の界面のミクロ組織を示す。5 μm程度の粒状組織を高いコントラストの画像で可視化できている。
内部の不連続な局所変形を定量評価することにより、信頼性を更に向上した次世代デバイスの開発に寄与すると考えられる。
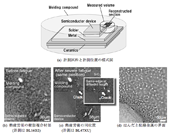
図3 デバイス実装構造内部の構造(過大な熱疲労で導入した微小き裂および界面組織)
今後の課題:
放射光ラミノグラフィは扁平な板状形状のまま内部の形態を3次元で可視化できるため、部品を生かしたまま稼働する過程の損傷を計測できる可能性がある。また、計測時の拘束が少ないため熱などの外部負荷を与えやすい。一方で、高分解能計測を行うには、外部負荷が計測に及ぼす影響を最小にし、その誤差を定量的に把握する必要があり、今後の課題である。
参考文献:
[1] M. Hoshino, K. Uesugi, A. Takeuchi, Y. Suzuki and N. Yagi, Review of Scientific Instruments, 82 (7), 6(2011).
[2] 木村英彦, 浅田崇史, 山口 聡, 加納大樹, SPring-8利用研究成果集, 3, 194 (2013).
[3] 浅田崇史, 木村英彦, 山口 聡, 妹尾与志木, 臼井正則, SPring-8サンビーム成果集, 2, 52 (2012),2011B5371.
ⒸJASRI
(Received: June 10, 2014; Early edition: August 29, 2014; Accepted: January 16, 2015; Published: February 10, 2015)