Volume3 No.1
SPring-8 Section B: Industrial Application Report
自動車メタリック塗装のイメージング観察
Imaging Observation of an Automobile Metallic Painting
ダイハツ工業株式会社
DAIHATSU MOTOR CO., LTD.
- Abstract
-
自動車メタリック塗装の明度や彩度に影響を及ぼすアルミフレークの配向メカニズムを明らかにするため、今後計画しているin-situイメージング観察の予備試験として観察条件、観察手法を検討した。実験ハッチ外から遠隔操作で塗装し、その過程をin-situ二次元イメージング観察した結果、アルミフレークの配向挙動を観察することに成功した。またCTによるアルミフレークの立体的な配向の様子を観察することにも成功した。
キーワード: メタリック塗装、イメージング、アルミフレーク配向
背景と研究目的:
塗装はさまざまな製品の耐候性を高め長寿命化を実現するだけでなく、見栄え向上により商品価値を高めることができ、産業界にとっては広く普及した極めて重要な産業基盤技術といえる。塗装技術は自動車だけでなく家電製品・民生機器・携帯機器・住宅機器・玩具などほとんど全ての製品に使われる極めて身近な存在である。特にメタリックやマイカ塗装は表面光沢を与えるだけでなく、角度によって明度や色彩が変化することで製品に立体感(奥行き)を感じさせ高級感を醸し出せるため採用が拡大している。
自動車においては製品出荷時に塗装されるだけでなく、経年使用された後に部分的に再塗装されるなど、極めて特殊な状況もある。この際に色調や光沢を揃えることが必須であり、いくつかの科学的なアプローチ[1,2]もなされているが、熟練者の経験に頼っているのが現状である。特にメタリック塗装の色味・光沢を揃えることはさらに難易度が高く、メタリック塗装の発色・光沢のメカニズムを科学的に理解・解明することは極めて重要である。
これまで乾燥・焼付工程を経た塗装板サンプルを用いてSEM(走査型電子顕微鏡)やCTスキャン等による光輝材(アルミフレーク)の配向性が、明度や彩度に支配的な影響を与えることが分かっている。アルミフレークのサイズは、長さ20~30 μm、厚み1 μm以下の円盤状であり塗膜中で様々な方向に配向している。SEM観察により、このアルミフレークが水平に配向している割合が多いほど正面から観察した際の明度が高く、横から観察した際の明度が低くなることが分かった。しかしながらこの配向性が塗装工程中のどのような要因によって決定されるのか科学的な解明は困難であった。
今回は今後計画している塗装中・ウエット状態での重ね塗り・乾燥・焼付けに至る動的なイメージング観察のための予備試験であり、観察条件・観察手法を検討することにより、SEM観察と同様のアルミフレークの配向解析ができることを目的として実験を行った。この観察方法を確立できれば、in-situでのアルミフレークの配向状態の動的観察につながり、配向メカニズムを明らかにできることが期待され、メカニズムが明らかになれば色変動を解消し品質の向上につながることが期待される。さらにはメカニズムの理解により、これまでにない新しい塗料や塗装技術の創成へと発展することを期待する。
実験:
SPring-8のBL46XUのビームラインを使用し、入射光の形状はフロントエンドスリットの開口を1×1 mmにして、試料上でのビームサイズは測定していないが、視野サイズより少し大きい程度に成型した。ミラーの入射角度は2.94348 mradに設定した。試料は樹脂(塗装材:ポリプロピレン(PP)、塗料:アクリル樹脂)とアルミフレークからなり、比較的軽元素であるため、X線エネルギーは10 keV、15 keVで試験し最適条件を検討した。また、樹脂とアルミフレークとの吸収差が比較的大きく、屈折コントラストを用いずともアルミフレークが観察可能であると考えられるためカメラ長は30 mm、検出器は浜松ホトニクス社製のビームモニタ3(10倍レンズ)とCCDカメラ(C4880-41S)を組み合わせて用いた。in-situ測定のため実験ハッチ内に自動塗装ガン、ハロゲンヒーター、塗料吸着処理用の活性炭吸着装置を設置し実験ハッチ外から遠隔操作した(ただし、今回ハロゲンヒーターはカメラへの熱影響が懸念されたため使用しなかった)(図1)。

図1 実験装置外観
入射光の向きから見て、横15 mm、高さ3 mm、奥行き5 mmのPPの上部に幅0.1 mm~1 mm、高さ0.2 mmの楔形の溝を形成した塗装材の上部から、乾燥後の塗膜厚み約20 μmになるよう、アルミフレークを含むアクリル塗料を塗布し、溝内に塗装された部分を二次元イメージング(露光時間120 ms)により観察した(図2)。120 msの露光時間にデータ保存の時間を加え、0.6 s毎に1画像を撮影した(図3)。また、別途塗装済みの樹脂板を直径1 mmの円柱状にくりぬき、塗膜の断面をCTによる三次元イメージング測定(露光時間120 ms、測定画像数920枚)により観察した。
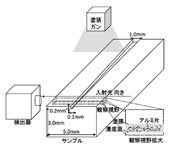
図2 測定光学系配置
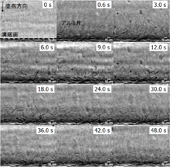
図3 塗装過程のアルミ片の挙動(0-48.0 s)
(図中の黒い針状の物質がアルミ片)
結果および考察:
塗装過程の二次元イメージングは、塗装材を奥行き方向に約5 mm透過する必要があるため10 keVでは計測できず15 keVで測定を行った。観察する溝の幅は、広い側ではアルミフレークが多く重なりあい、光が透過しなかったため狭い0.1~0.2 mm部分を観察した。
図3に塗装過程を二次元イメージング撮影した結果(0 sから48 s後)を示す。塗料が塗装材の溝の底面に塗布され始めた1コマ前の画像を0 sと定義した。今回撮影では、塗膜の上面はコントラストがつかず観察できなかったが、噴射量および実験後の塗装状態から視野の中に塗膜の表面が存在し、時間経過とともに塗膜表面は下降していると推測される。
塗装直後から24 sまではアルミフレークが塗料中を激しく動き回り、24 s以降はアルミフレークの動きが落ち着き、溶剤の揮発とともに徐々に沈降する様子を世界で初めて観察することができた。
またこれまでラボのX線CTでは、複数のアルミフレークのかたまりしか観察できず、配向を解析することができなかったのに対し、今回測定したCTによる三次元イメージングの結果、若干コントラストが低いものの、アルミフレーク一つ一つの形状・傾きを観察することができた(図4)。
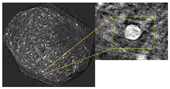
図4 塗装サンプルのCT断面図(図中の白い部分がアルミ片)
今後の課題:
今回の実験で確立した観察手法・観察条件を用いて、塗装条件を色々と変えた際の塗膜中のアルミフレークの配向挙動を観察することで、アルミフレークの配向メカニズムを明らかにする。また二次元イメージングの観察に加え、CTによる観察を組み合わせることで詳細なアルミフレークの配向状態についても解析する。今回は、PPに形成した溝に塗装した部分を観察したため、放射光を5 mm透過させる必要があり、エネルギーを15 keVから下げることができなかった。そのためアルミフレークのコントラストが低く、針状のアルミフレーク(円盤状のアルミフレークを横から観察した状態)は観察できたものの、面状(円盤状のアルミフレークを面方向から観察した状態)のものはほとんど観察されなかった。次回は、塗装サンプルの形状を工夫し、より低いエネルギーで観察できるように検討する。
参考文献:
[1] 川口洋一ら、塗料の研究, 145, 14 (2006).
[2] 佐々木宣征、TECNO-COSMOS, 22, 8 (2009).
ⒸJASRI
(Received: October 9, 2014; Accepted: January 16, 2015; Published: February 10, 2015)