Volume2 No.1
Section B : Industrial Application Report
ゴムの摩耗の起源の解明
Analysis of the Origin of Rubber Abrasion by X-ray Imaging Method
a横浜ゴム(株), b金沢大学
aTHE YOKOHAMA RUBBER CO., LTD., bKanazawa University
- Abstract
-
先端が半球状である針をゴムに押付けて摩擦させた時に、ゴム試験片の亀裂生成の様子をX線イメージング法によって観察した。実験は、SPring-8のBL19B2にて実施し、1秒間に59枚の画像を取得することで、摩擦中のゴムの破壊の様子を観察することができた。得られたイメージング画像から、針先端部に生じるせん弾力によって、針先端付近のゴムがせん断破壊し、ゴム表面に亀裂が生じるものと推定された。
キーワード: ゴム、摩擦、摩耗、破壊、X線イメージング、リアルタイム観察
背景と研究目的:
ゴム材料では、しばしばその耐摩耗性が問題となる。省資源化や経済性の観点から摩耗しにくいゴムが望まれていることは言うまでもない。ゴム材料の摩耗は、摩擦によってその一部が破壊され、さらに繰り返し摩擦されることによって破壊が進展し、その結果として一部のゴムが脱落することによって進行していくと考えられる。従って、ゴムの摩耗メカニズムを解明するためには、破壊の起源とその進展の様子を調べる必要がある。破壊の進展に関しては、古くから耐摩耗性との関係について検討されている[1]。摩耗したゴム試験片の表面には、しばしば摩擦方向と垂直の方向に帯状の摩耗痕が見られる。これは、アブレージョンパターンと呼ばれ、そのパターン間隔と耐摩耗性が相関することが知られている。アブレージョンパターンの成長過程を直接観察して詳細に解析した報告例[2]もあり、摩擦によってアブレージョンパターンが伸張され、パターンの根元部分で亀裂が伸展していくことが知られている。
一方、破壊の起源に関しては、摩擦後のゴム試験片の観察結果から考察した例[3]はあるが、ゴムが破壊する瞬間を直接観察した報告は少ない。Schallamach[3]は、ゴムと円筒状の突起の接触部の応力分布を光弾性によって観察し、接地後端部に最も応力が集中することを示しているが、実際の破壊がこの部分で発生するかどうかの確認はされていない。亀裂の発生に関しては、その検出、解析自体が困難である。そこで、SPring-8のX線イメージング法を利用して、ゴムと突起を摩擦させた時の亀裂発生の様子を観察し、摩耗の起源を特定する研究を実施した。
実験:
図1に示す摩擦摩耗試験機を用いて、円筒状のゴム試験片と針状の突起とを摩擦させた。そして、X線をゴムと突起の接触部に測面から照射し、イメージング画像を連続して取得することにより、摩擦によってゴム片に亀裂が発生する様子を観察した。可視光線を用いた場合には、針の先端がゴムに埋もれてしまうために、先端部分のゴムの変形、破壊の様子を観察することはできないが、X線を利用すれば、ゴム中の針の挙動、および、ゴムの変形の様子を観察することが可能である。
針は根本の太さが約1 mmであり、先端が曲率半径0.07 mmの半球状のものを用いた。先端部分の角度は約30°であった。
ゴム試料としては、スチレン-ブタジエン共重合体ゴム(SBR)に硫黄を配合して加硫したものを使用した。ゴム試験片の厚みは5 mmとした。突起を2 Nの荷重でゴム片に接触させて、2 mm/sの滑り速度で摩擦させた。
X線イメージング測定では、カメラは浜松ホトニクス製ORCA-Flash2.8 C11440(f=35)を用いた。ビームモニターは、BM2のf値が50 mmのもので、蛍光体としてP-43の厚みが0.04 mmのものを用いた。視野を4.8×5.5 mmとして、露光時間を15 msとすることにより、1秒間に59枚のイメージング画像を取得できた。X線のエネルギーは20 keV、試料-カメラ間距離は600 mmとした。イメージング画像のピクセルサイズは10 μmであった。
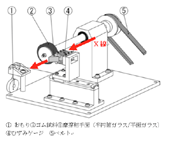
図1.摩擦摩耗試験機の概略図
結果および考察:
図2に、実験で得られたイメージング画像を示した。図2(a)〜(i)それぞれの左上に見られる黒色部は針状の突起である。右側の灰色の部分はゴムであり、針が押付けられて、ゴムが変形している様子が観察された。ゴム試験片は、図の右側がホイールによって固定された状態で、上から下方向に回転している。また、針の位置は固定されている。図2(a)を基準として、図2(b)は0.39 s後,図2(c)は0.53 s後,図2(d)は0.59 s後,図2(e)は0.63 s後,図2(f)は0.68 s後,図2(g)は0.86 s後,図2(h)は0.97 s後,図2(i)は1.09 s後の画像である。すなわち、図2(a)を基準として、図2(i)は2.18 mm下方にゴムが移動した位置の画像である。図2において、ゴムは上から下に流れるので、針の下方ではゴムが変形して窪みができる。図2(a)〜(c)では、針の下方で、針の先端からゴムの表面にかけて円弧状の線が観察されており、ゴムが変形して窪みが生じたことがわかる。図2(i)では、中央付近に舌状の突起が観察された。この突起は、図中に点線の矢印で示した位置を根元とし、ゴムの表面部分が裂けることによって生じたものであることがわかる。この亀裂の発生要因を調べるために、図2(h)から(f)にさかのぼって画像を見ると、図2(h)から(f)では、実線の矢印で示した部分にこぶ状の突起が観察され、点線の矢印で示した部分には窪みが観察された。図2(f)から(h)に見られるこぶ状の突起は、裂けたゴムが針とゴム表面の間で丸まったもので、その後、図2(i)に見られる舌状の突起になったと考えられる。これは、裂けたゴムの先端が針の先端に凝着して留まり、ゴム片が下方に回転するに従って亀裂の窪みだけが下方に移動したものと考えられる。図2(f)から(h)にかけて、図中の点線の矢印で示した窪みの長さは、ほとんど変化していない。従って、図2(f)から(h)の区間では、舌状の突起部分が引伸ばされていただけで、亀裂は進展していないと考えられる。また、図2(e)では窪みが観察されないことから、亀裂は図2(e)から(f)の間で発生したと考えられる。
針のゴム中への押し込み深さは、図2(a)から(e)にかけて減少した。これは、針の前面にゴムの圧力が加わると同時に、針の後方のゴムが伸張されることによって針が押し上げられたと考えられる。すなわち、針の先端には、図2(a)から(e)各図の右上から左下方向に力が生じ、針先端部のゴムにせん弾力が生じて、せん断破壊に至ったものと推定された。ただし、今回の実験では、亀裂の発生箇所を正確に特定することはできなかった。一方で、図2(e)から(i)にかけては、針のゴム中への押し込み深さが増加した。これは、亀裂が発生することにより、針後方のゴムの伸張力が低下したためと考えられる。このように、X線イメージング法によって、ゴムに亀裂が生じる過程を観察することが可能となった。
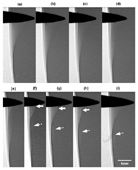
図2.ゴムと針の摩擦中のX線イメージング画像
今後の課題:
亀裂の発生箇所を特定するには、空間分解能が高く、より明確なコントラストが得られる条件で実験する必要があると考えられる。また、ゴム内部のひずみ分布を測定できるように、ゴムにマーキング粒子などを配合[4]するなどの工夫が必要である。
ゴム片の物性や配合、あるいは、突起の形状によって、亀裂生成の様子が変化することが予想される。更なる実験と詳細な解析を行うことによって摩擦によって破壊しにくいゴムの開発につなげることができると考えられる。
参考文献:
[1] E. Southern, A. G. Thomas, Plastics and Rubber: Materials and Applications, p.133 (November, 1978)
[2] T. Iwai, Y. Uchiyama, K. Shimosaka, K. Takase, Wear, 259, 669 (2005)
[3] A. Schallamach, Wear, 1, 384 (1958)
[4] 竹内正和,網野直也,石川泰弘,鈴木芳生,竹内晃久,日本ゴム協会2007年年次大会 研究発表講演会 講演要旨集,p.20(May, 2007)
ⒸJASRI
(Received: February 14, 2013; Early edition: March 25, 2014; Accepted: July 3, 2014; Published: July 10, 2014)