Volume2 No.1
Section B : Industrial Application Report
放射光ラミノグラフィによるパワーモジュール構造の内部形態計測
Measurement of Internal Morphology in Power Module Package by Synchrotron X-ray Laminography
a(株)豊田中央研究所, b(公財)高輝度光科学研究センター
aToyota Central R&D Labs., Inc., bJASRI
- Abstract
-
自動車の駆動系は電動化が進んでおり、その基盤部品のひとつであるパワーモジュールの内部構造や損傷を非破壊で計測できれば、性能と信頼性の更なる向上に有用である。扁平なテストモジュールをラミノグラフィで計測した結果、モールド樹脂やはんだなどの異種材料積層体の内部形態を数μmの分解能で3次元構成できた。また、その場加熱計測を実施し、今後の内部熱ひずみ計測に必要な基礎条件を得た。
キーワード: イメージング、ラミノグラフィ、パワーモジュール、信頼性評価
背景と研究目的:
ハイブリッド車や電気自動車の駆動系基盤部品のひとつであるパワーモジュールは、運動性能や信頼性のみならず、環境性能も決定づける重要な要素である。この高性能化と高信頼化は、省エネルギーや温室効果ガス低減に有用と考えられる。パワーモジュールは、半導体、金属や樹脂等の異種材料接合体であるため、製造工程および使用時の温度変化により内部に応力が発生する。
次世代のパワーモジュールを開発する際、内部の「応力」、「変形」および「欠陥」の3要素を実測できれば、変形・損傷機構を解明して低減方法を具体化することができ、信頼性の向上に有用である。結晶材料の微小部や内部の応力計測には放射光回折法が適しており、これまでに種々の材料で応力計測を行い[1-4]、現在パワーモジュールへの適用検討を進めている。一方、変形や欠陥等の内部形態計測にはCT法が適している[5]。部品の信頼性評価は非破壊で行うことが重要であるため、切断等の試料調整をしない内部計測が重要であるが、パワーモジュールは扁平なため、従来のCT法では回転角によって透過像が得られず計測が困難であった。一方、ラミノグラフィは試料の法線(回転軸)を放射光に対して傾けて計測するため、長尺方向を透過する必要がなく、フルサイズの部品を計測できる。信頼性評価には、多種材料の多層構造でミクロな内部損傷を可視化するために適切な計測条件を明確にする必要がある。これまでの課題で、単層の棒材の負荷過程におけるCT測定[6]、および薄いモジュール基礎構造のラミノグラフィ計測[7]を行い計測条件を検討してきた。
本課題では、5種6層の構成からなる比較的厚いパワーモジュール構造の内部形態計測を行った。また、同計測セットアップのまま加熱し、熱ひずみを負荷した状態で内部形態の変化を計測するための基礎検討を行った。
実験:
計測試料の構成を図1に示す。試作したパワーモジュール構造のテスト試料であり、パワー半導体素子Si(厚さ約0.1 mm)、はんだ(約0.1 mm)、配線Al(約0.3 mm)、絶縁セラミックス(約0.6 mm)、基板Al、およびこれらを包埋するモールド樹脂からなり、直径は約50 mmで厚さ約3 mmである。本計測の解像度を再構成後に確認できるよう、はんだ部にコントラストが明瞭なボイドを熱疲労により積極的に導入した試料とした。ラミノグラフィの計測は、主にSi素子およびはんだのエッジ部(図1に赤線で示す円柱体積)で行った。
計測セットアップを図2に示す。計測はBL19B2の自動ステージおよび再構成ソフトを利用して行った。波長はSnの吸収端を考慮し29 keVとした。XYステージを搭載した自動回転ステージの下に30°の傾斜台を設置してラミノグラフィの傾斜軸とした。試料は樹脂製のジグ上にセットし、放射光はこのジグも透過する。計測にはCMOSカメラを使用し、解像度は2.7 μm/pixel、撮影は0.24°間隔とした。一定間隔で計測位置から退避してバックグラウンド像を取得した。また、本セットアップのまま外部から加熱できるようヒータを設置した。
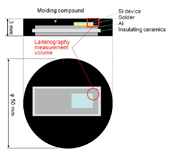
図1 異種材料の多層構造であるパワーモジュール構造の扁平テスト試料
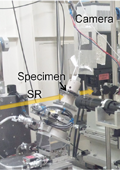
図2 ラミノグラフィ計測のセットアップ
結果および考察:
計測結果を図3に示す。左下ははんだ内部、右上はパワー半導体素子内部の位置における水平断面の再構成像である。はんだ部に導入したボイドおよびモールド樹脂の含有物の形態が明瞭に確認でき、今後、内部の変形やき裂形態を数〜10 μm程度の分解能で、高いコントラストで計測する目処が得られた。一方、ラミノグラフィ計測では回転軸を傾けた方向に高コントラスト部からアーティファクトが発生する場合があり、本計測では素子層にはんだ層のアーティファクトが顕著に見られる。はんだエッジのようなシャープな形状が既知の場合、アーティファクトの発生点とその影響はおおよそ見積ることができ、内部形態の誤差評価は可能と考えられる。また、加熱中の計測では、再構成像に若干のコントラスト低下等が見られたが、加熱前後の比較が可能な画質が得られた。加熱前後の再構成画像を図4に示す。今後、計測時の誤差評価および熱ひずみの解析を試みる。
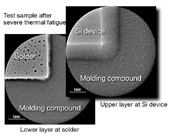
図3 扁平テストモジュール内のはんだ、素子およびモールド樹脂部の可視化
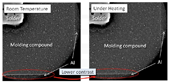
図4 外部ヒータ加熱の再構成画像への影響
今後の課題:
本ビームタイムではラミノグラフィの計測・解析条件の探索に時間を必要としたため、計測は限られた位置の内部形態観察に限られ、損傷部の探索までには至らなかった。今後、熱疲労き裂など内部損傷の可視化を試みる予定である。また、アーティファクトの影響度の定量化と低減を行う。
参考文献:
[1] Y. Akiniwa, H. Kimura, J. Shibano, K. Kiriyama and T. Shobu, Materials Science Forum, 652, 290 (2010).
[2] Y. Akiniwa, H. Kimura and T. Sasaki, Advances in X-Ray Analysis, 52, 493 (2009).
[3] 秋庭義明, 小島由梨, 木村英彦, 丸小慶介, 材料, 57(7), 660 (2008).
[4] Y. Akiniwa, H. Kimura, K. Ukai, M. Yokoyama and Y. Mizutani, Materials Science Forum, 571-572, 339 (2008).
[5] 政木清孝, 佐野雄二, 越智保雄, 秋田貢一, 梶原堅太郎, 足立隆史, 材料, 58 (12), 975 (2009).
[6] 浅田崇史 他, サンビーム年報・成果集(2012), 2011B5371.
[7] 木村英彦, 浅田崇史, 山口 聡, 加納大樹, SPring-8 利用研究成果集, 3, 194 (2013).
ⒸJASRI
(Received: February 25, 2014; Accepted: July 3, 2014; Published: July 10, 2014)