Volume1 No.3
Section B : Industrial Application Report
アルミニウム合金摩擦攪拌接合継手における疲労き裂進展挙動のラミノグラフィによる非破壊観察
Nondestructive Observation of Fatigue Crack Propagation Behavior in Friction Stir Welded Joints of Aluminum Alloy by Laminography
a(株)東芝, b沖縄工業高等専門学校, c(公財)高輝度光科学研究センター, dNASA - Johnson Space Center, e富士重工業(株)
aToshiba Corporation, bOkinawa National College of Technology, cJASRI, dNASA - Johnson Space Center, eFuji Heavy Industries Ltd.
- Abstract
-
アルミニウム合金A6061-T6の摩擦攪拌接合(FSW)継手試験片に曲げ疲労によりき裂を導入し、その形状をラミノグラフィにより可視化した。更に、ビームライン脇に仮設した曲げ疲労試験機を使用してき裂を進展させ、その様子を非破壊で観察した。大型の板状の構造物の場合CTの適用は困難を伴うが、ラミノグラフィの適用は原理的に可能であり、微細な疲労き裂やその進展の様子を非破壊で観察できることを確認した。
キーワード: 摩擦攪拌接合,アルミニウム合金,疲労,き裂進展,ラミノグラフィ
背景と研究目的:
摩擦攪拌接合(Friction Stir Welding; FSW)は従来の溶接と異なり、溶融温度以下で軟化した材料を局所的に攪拌して接合する新しい接合法である[1]。FSWは接合温度が低く入熱が少ないため、継手効率が高く接合後の変形が小さい。このため、柔らかく攪拌が容易なアルミニウム合金製の長尺薄肉構造物(鉄道車両のボディ、航空機の胴や翼など)への適用が広がっている[2,3]。FSW接合部は攪拌の状況を反映した特異な組織となり、疲労き裂の発生や進展がその組織に影響されるため、従来の溶接継手とは異なる複雑なき裂進展挙動を示すことが知られている[4]。
本研究は、放射光を光源としたラミノグラフィによりFSW継手に生じた微細な疲労き裂を非破壊で可視化し、その進展挙動を明らかにすることを目的としている。前回の課題(2011B1861)では、深さが異なる一連のスライス像を再構成することにより、継手内部のき裂形状が非破壊で再現できることを確認した[5]。今回の課題(2012A1274)は、小型の平板曲げ疲労試験機をビームライン脇に仮設し、き裂の進展を非破壊で可視化することを試みた。
実験方法:
1.試験片の作製
供試材には、前回の課題(2011B1861)と同様に厚さ3 mmのAl-Mg-Si系展伸用アルミニウム合金A6061-T6圧延材を使用した[6-8]。供試材の化学組成を表1に示す。FSW継手は汎用フライス盤とM4の逆ネジが切られた長さ3 mmのピンを有するφ10 mmのツールを使用して、突合せ接合により作製した。接合条件はツール回転数1400 rpm、前進角3°、送り速度41 mm/minであり、接合幅は約8 mmであった。母材とFSW継手の機械的性質を表2に示す。疲労試験片はFSW継手からワイヤ放電加工により図1に示すように採取した。試験片表面のツール走査痕はフライス加工によって除去し、表面と側面をエメリ研磨とバフ研磨により鏡面に仕上げた。
FSW接合部の中心(試験片中心)には直径0.3 mm、深さ0.3 mmのドリル穴を設け、き裂発生の起点とした。その後、後述する平板曲げ疲労試験機を使用して、応力振幅120 MPaの完全両振り(応力比R = -1)、室温・大気中、負荷繰り返し速度22 Hzの条件で試験片に2×105回の疲労負荷を与え、疲労予き裂を付与した。光学顕微鏡で観察したところ、予き裂の長さは3.2 mm程度であった。
表1 供試材(A6061-T6)の化学組成 [重量%]

表2 A6061-T6母材およびFSW継手の機械的性質

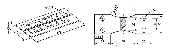
図1 疲労試験片の採取位置(左)および疲労試験片の寸法・形状(右)
2.き裂の可視化試験
ラミノグラフィによる疲労き裂の可視化試験は、これまでと同様にSPring-8産業用ビームラインBL19B2の第1ハッチで行った。測定レイアウトを図2に示す。試験片の回転軸を鉛直から傾けることを除けば、CTと同一のレイアウトである。X線エネルギーは28 keV、試験片とX線カメラの距離は0.8 m、試験片回転軸の傾きは30°とした。検出器の実効的なピクセルサイズは5.6 μmであり、視野は水平方向11.2 mm、垂直方向4.5 mmとした。
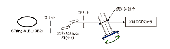
図2 ラミノグラフィ測定レイアウト(BL19B2第1ハッチ)
疲労き裂は通常では閉口しているため、図3に示す試験片ホルダーにより試験片に曲げ負荷を与え、き裂をわずかに開口させた[9-11]。投影データは0.5°刻みで全周にわたって取得した。10°毎にステージを上下させてアクリルパイプのみの投影データを取得し、アクリルパイプによるX線の減衰を補正した。
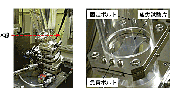
図3 ラミノグラフィ用試験片ホルダー
今回の課題(2012A1274)では、予き裂を導入した時と同一型式の平板曲げ疲労試験機PBF-30X(テークスグループ社)をビームライン脇に仮設し、曲げ疲労によるき裂進展とラミノグラフィによるき裂観察を交互に繰り返すことによって、疲労き裂の進展を非破壊で画像化することを試みた。疲労試験機の外観と試験片の取付け状況を図4に示す。
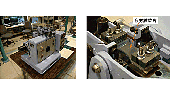
図4 両振り型曲げ疲労試験機PBF-30X(左)と試験片の取付け状況(右)
実験結果:
ラミノグラフィにより得られた試験片表面の再構成ライス像(一部)を図5に示す。左から疲労負荷回数が2.0×105回,2.5×105回,2.75×105回(応力振幅120 MPa)であり、き裂長さを各々の画像から算出すると約3.2 mm,5.1 mm,6.3 mmとなった。疲労負荷回数2.0×105回のき裂長さ(3.2 mm)が、光学顕微鏡で観察した予き裂の長さとほぼ一致したことから、ラミノグラフィにより再構成された断層像は適切なものと考えられる。
図5より試験片の表面では、疲労負荷を与えるに従ってき裂が円弧状に進展していることがわかる。き裂の曲率半径を求めると7 mm程度であり、FSWのツール(半径5 mm)の回転による材料の塑性流動の範囲に関連するものと思われる。なお、各スライス像の中心付近の穴は初期き裂を導入するためのドリル穴(直径0.3 mm)である。
試験片表面から約0.56 mm内側の再構成ライス像(一部)を図6に示す。何れの疲労負荷回数においても、き裂長さは表面と比較して短い。疲労負荷回数2.5×105回までは応力負荷方向(試験片長手方向)にほぼ垂直な方向にき裂が進展していたが、2.75×105回では試験片表面と同様にき裂の屈曲が始まっていた。試験片内部では、表面ほど塑性流動の影響は大きくないためと思われる。
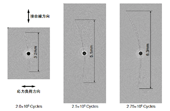
図5 FSW継手試験片表面の再構成像
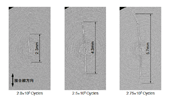
図6 試験片表面から0.56 mm内側の再構成像
結論および今後の課題:
アルミニウム合金A6061-T6のFSW継手試験片に曲げ疲労によりき裂を導入し、その形状をラミノグラフィにより可視化した。更に、ビームライン脇に曲げ疲労試験機を導入し、疲労負荷によるき裂進展とラミノグラフィを交互に繰り返すことにより、き裂進展の様子を非破壊で観察した。その結果、試験片表面ではツールの回転による材料の塑性流動の影響がき裂の形状に大きく現れていたが、試験片内部ではその影響は表面ほど大きくないことなどが明らかになった。
FSW継手では、疲労き裂の進展はその組織に依存して複雑な挙動を示すと言われていたが、その進展の様子を今回初めて非破壊で可視化することに成功した。今後は、複数の試験片に対して同様の試験を行って再現性を確認するとともに、FSW継手の組織とき裂進展との関係を調べ、き裂進展のメカニズムを検討する。また、き裂の進展を抑制するための接合条件や残留応力分布などについて検討を行う。
参考文献:
[1] R.S. Mishra and Z.Y. Ma:Friction stir welding and processing,Mater. Sci. Eng. R,50,1-78 (2005).
[2] 森久史, 他: 鉄道車両への摩擦攪拌接合の適用の現状, 軽金属,57,506-510 (2007).
[3] 武久浩之: 航空機用アルミニウム合金のFSW技術, 軽金属,56,178-183 (2006).
[4] O. Hatamleh, et al.: Fatigue crack growth performance of peened friction stir welded 2195 aluminum alloy joints at elevated and cryogenic temperatures,Mater. Sci. Eng. A,519,61-69 (2009).
[5] 佐野雄二, 他: アルミニウム合金摩擦攪拌接合継手に生じた疲労き裂のラミノグラフィによる非破壊観察, 平成23年度 SPring-8重点産業利用課題成果報告書 (2011B1861).
[6] 山城研二, 政木清孝, 屋嘉部求, 具志孝, 佐野雄二: A6061摩擦攪拌接合継手部材のLP処理による疲労特性改善, 日本機械学会2010年度年次大会, S305-1-5.
[7] K. Yamashiro, K. Masaki, T. Gushi and Y. Sano: Effects of laser peening on plane bending fatigue properties of friction stir welded A6061-T6 aluminum alloy, Technical digest of 3rd Int. Conf. on Laser Peening and Related Phenomena (2011).
http://www.mapse.eng.osaka-u.ac.jp/3rdLP/img/digest.pdf
[8] Y. Sano, K. Masaki, T. Gushi and T. Sano: Improvement in fatigue performance of friction stir welded A6061-T6 aluminum alloy by laser peening without coating, Mater. Des.,36,809-814 (2012).
[9] 政木清孝, 桑江文幸, 佐野雄二, 梶原堅太郎: 放射光μCTによる疲労き裂観察結果に及ぼす引張予負荷の影響, 日本機械学会M&M2011カンファレンス, OS0510.
[10] 政木清孝, 桑江文幸, 佐野雄二, 梶原堅太郎: 放射光CTならびに産業用X線CTによる疲労き裂観察とその比較, 日本機械学会2011年度年次大会, G030131.
[11] 政木清孝, 西銘一貴, 佐野雄二, 梶原堅太郎: 放射光ラミノグラフィによるFSW継手材の疲労き裂観察, 日本機械学会2012年度年次大会, G030051.
ⒸJASRI
(Received: February 14, 2013; Early edition: August 30, 2013; Accepted: November 1, 2013; Published: December 10, 2013)