Volume2 No.1
Section B : Industrial Application Report
X線マイクロトモグラフィーを用いた炭素繊維複合材料のクラック解析
Microcrack Analysis of Carbon Fiber Reinforced Plastic by Using X-ray Micro-Tomography Method
三菱レイヨン(株)
Mitsubishi Rayon Co., Ltd.
- Abstract
-
樹脂中に炭素繊維を埋め込んだモデル試験片を用いて、炭素繊維の破断によって生じる樹脂へのクラックの形状を、X線マイクロトモグラフィーを用いて3次元的に調べた。繊維表層の破壊の起点を中心に、繊維側と樹脂側の両方に向かってクラックが放射状に発生することがわかった。さらにクラックの進展によって別の繊維が破断する様子が高分解能かつ非破壊的に初めて観測された。
キーワード: X線マイクロトモグラフィー、炭素繊維複合材料、クラック解析
背景と研究目的:
炭素繊維複合材料(以下、複合材料とよぶ)は軽量かつ物性に優れる材料として、航空宇宙用途や産業用途で需要が拡大しつつある。特に航空機分野では機体の軽量化による燃費向上が課題となっており、複合材料の更なる高性能化が求められている。
複合材料の強度向上を目指すうえで破壊現象を捉えることは非常に重要であり、炭素繊維1本(単繊維)の破断に伴うクラックの生成と進展の評価が可能となれば、強度向上に向けた有用な情報が得られる可能性がある。複合材料の破壊モデルの一つとして、単繊維の破断が周囲の繊維の破断を引き起こして、これが連続的に発生することで複合材料全体の破壊に至るモデルがある。これまでの破壊現象の解析では、切断加工したサンプル表面の顕微鏡観察が中心であった。しかしこの方法では、切断加工によって生じたクラックと本来存在していたクラックとの区別が難しいうえ、クラックの3次元的な広がりを詳細に調べることはできなかった。この問題に対して材料を非破壊的かつ3次元的に評価できるX線トモグラフィーは有用である。
近年の放射光マイクロビーム技術の進歩により高分解能な評価が可能となった。また複合材料を構成する炭素繊維および樹脂はいずれも炭素原子を主成分とするためX線の吸収コントラストが得られない状況にあったが、放射光の位相差法が確立されたことにより、炭素繊維と樹脂のコントラストが向上した[1]。X線マイクロトモグラフィーを使った複合材料のクラック解析として、分解能が数μmのビーム(ESRF・ID19)を使って複合材料に生じた100 μm前後のクラックを解析した報告がある[2,3]。しかしこの報告では、既に大きく進展したクラックを捉えているため、破壊の起点である単繊維(直径5〜7 μm)の破断によるマイクロクラック(数μm)の発生機構は明らかになっていない。
そこで本研究では分解能52 nm/pixelの放射光X線マイクロトモグラフィー(SPring-8 BL47XU)を用いて炭素繊維の単繊維の破断に伴って生じる樹脂へのクラックや、そのクラックが隣接する繊維に与える影響について調べた。
実験:
□サンプル
実験にはストランド強度が約500 kgf/mm2の2種類の炭素繊維(サンプルA, サンプルB)を用いた。まず始めに単繊維の破断に伴って生じる樹脂へのクラックを調べるために、繊維束から単繊維を取り出し図.1aに示すようにエポキシ樹脂中に埋め込んだダンベルを作成した。これを引張試験機で引っ張ることで内部の単繊維は複数の場所で破断する(図.1b:フラグメンテーション試験)。
ダンベルの一部を切り出して先端を尖らせる加工を行うことで測定サンプルとした(図.1c)。
次に単繊維の破断に伴って樹脂に生じるクラックが、隣接する繊維へ与える影響を確認するために、10本前後の単繊維を樹脂中に埋め込んだダンベル試験片を作製して、前記と同じく引張試験および切出し・加工を行って測定サンプルとした。
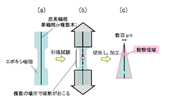
図1.測定サンプルの作製手順
□測定条件
実験はSPring-8(BL47XU)で実施した。図2に光学系を示す。また図3にはセットアップの様子を示した。炭素繊維およびマトリクス樹脂は軽元素から構成されるため、従来の吸収コントラスト法には限界がある。本実験では軽元素領域で非常に高い感度をもつ位相差コントラスト法を用いた。以下に詳細な測定条件を記載する。
・X線のエネルギー: 8 keV
・露光時間: 250 msec
・試料方位角間隔: 0.2°(ハーフスキャン0~180°)
・位相板: NTT-AT社製
厚さ0.96 μmのタンタルで描画されており8 keVのX線に対して試料からの回折波と
非回折波の間を、丁度λ/4だけ位相変化させる。
・検出器: sCMOS撮像素子を利用した可視光変換型の検出器
・分解能: 54 nm/pixel
・画像の再構成: Convolution back projection法[4]
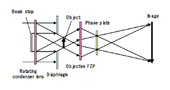
図2.光学系
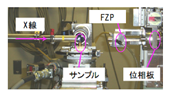
図3.セットアップの様子
結果および考察:
以下ではサンプルAの結果について述べる。図4a〜4eに破断点付近の繊維断面方向の再構成像を示す。それぞれの観察点は図4gに示すように繊維軸に沿って上から順に示した。図4gは図4aに示すA-B間でスライスした縦断面である。比較のために破断していない正常部分の再構成像を図4fに示す。図4a〜4eより単繊維の破断に伴う樹脂へのクラックは放射状に進展していることが分かった。また図4gよりクラックの長さは繊維の直径程度であった。ここで図4a, 4eを詳細に見ると、破線で示した丸枠を起点に繊維に放射状の縞模様が発生していることがわかる。周囲に樹脂が無い状態で炭素繊維の引張試験後の破断面を観察すると、炭素繊維の破断の起点は繊維表層にあり起点から放射状の亀裂が繊維側に進展することと対応する[5]。すなわち図5に示すように、繊維表層の破壊の起点を中心に繊維側と樹脂側の両方に向かってクラックが放射状に発生することがわかった。この現象は測定した5つの試料すべてに共通して確認された。このような微視的なクラックの進展を捉えた事例はこれまでに報告が無く、初めて測定に成功したと考えている。(サンプルBについて:樹脂中で破断した炭素繊維の隙間は、図4gのように数μmが妥当と考えている。しかしサンプルBは隙間が10 μm以上もあり、通常では考えにくい状態となった。試料の作製の段階で(繊維の樹脂への埋め込み、引張、加工処理のいずれかで)問題があった可能性もあるため、本報告では試料の作製に問題が無かったと思われるサンプルAについて報告した。)
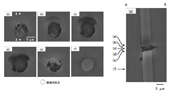
図4.単繊維の破断によって生じるクラックの様子
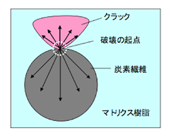
図5.炭素繊維の破壊に伴うクラックの進展の様子
次に単繊維の破断に伴って生じたクラックが周囲の繊維に与える影響を図6に示した。図6bは図6aに示すA-B間でスライスした縦断面である。図6a、6bからも分かるように、繊維Xから発生したクラックが繊維Yにぶつかったところで繊維Yが破断していることが分かる。このサンプルでは繊維Yの破断によってクラックが生じなかったため、繊維Xによって生じたクラックの進展は繊維Yで止まったことになる。周辺繊維が連続破断に至らなかった点で、このような状態は複合材料としては好ましいと推定できる。
ただし、複合材料としてより好ましくは繊維Xの破断によってクラックが発生しないことである。複合材料の高性能化のためには、例えばマトリクス樹脂の高靭性化などによるクラックの生成を抑制する方向性が考えられる。
以上のように、これまで模式図で理解されてきた複合材料の破壊現象について、高分解能かつ非破壊的な放射光X線マイクロトモグラフィー技術を用いることで破壊現象をより詳細に理解することができた。“破壊のメカニズムを理解したうえでの複合材料の開発”につながる知見を得ることができ、産業的な価値は大きいと考えている。
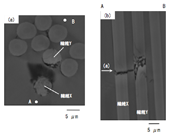
図6.単繊維(繊維X)の破断によって生じたクラックが隣接する繊維(繊維Y)を破断させる様子
参考文献:
[1] F. Cosmi, A. Bernasconi, N. Sodini, Composites Science and Technology, 71, 23 (2011).
[2] P. Wright, X. Fu, I. Sinclair, S. M. Spearing, Journal of Composite Materials, 42, 1993 (2008).
[3] A. E. Scott, M. Mavrogordato, P. Wright, I. Sinclair, S. M. Spearing, Composites Science and Technology, 71, 1471 (2011).
[4] http://www.slaney.org/pct/
[5] K. Honjo, Carbon, 41, 979 (2003).
ⒸJASRI
(Received: October 1, 2012; Early edition: March 25, 2014; Accepted: July 3, 2014; Published: July 10, 2014)