Volume2 No.1
Section B : Industrial Application Report
浸炭層模擬材のき裂発生・伝播のその場観察
Assessment of Low-cycle Fatigue Behaviors in Case Hardening Steel
a九州大学, b大同特殊鋼株式会社, c豊橋技術科学大学, d(公財)高輝度光科学研究センター
aKyushu University, bDaido Steel Co., Ltd., cToyohashi University of Technology, dJASRI
- Abstract
-
浸炭焼入鋼材は自動車用歯車等に用いられている。浸炭材の疲労挙動の詳細は明らかになっておらず、硬さ・残留オーステナイト・残留応力といった因子の影響も不明な部分が多い。浸炭層を模擬した高硬度鋼材での疲労き裂の進展過程をSPring-8の放射光によるX線CTでその場観察した。き裂の進展経路を明らかにし、浸炭材の疲労破壊メカニズムの解明を行うことを試みた。そして、高硬度鋼の疲労き裂の観察に成功した。
キーワード: 炭素鋼,X線CT,き裂発生,き裂伝播
背景と研究目的:
浸炭焼入は鋼材の表面硬化熱処理の代表的なものであり、自動車用歯車等に用いられている。浸炭された部材表面は0.8%程度の炭素を含み、700 HV以上に強化され高い疲労強度を持つ。自動車用歯車は歯元での曲げ応力に起因した疲労破壊で破損するのが一般的である。一般的に疲労破壊は、加工傷等の表面欠陥や非金属介在物などの内部欠陥からき裂が生じる「き裂発生」と1サイクルごとにストライエーション等を生じながら進展する「き裂伝播」に分けられる。しかしながら疲労試験中のき裂発生・伝播を観察する手法はなく、試験後の破面から類推するしかないことに加え、高硬度材はリバーパターンを呈し1サイクルごとの進展を観察できない。このため、浸炭材の疲労挙動の詳細は明らかになっておらず、硬さ・残留オーステナイト・残留応力といった因子の影響も不明な部分が多かった。
本研究では、浸炭層を模擬した高硬度材の疲労破壊過程を4D観察することにより、き裂伝播の直接観察を試みる。これにより、様々なミクロ組織因子がマクロ破壊特性に及ぼす影響を誤解することなく、定量的かつ精密に明らかにする。その上で、硬さ・残留オーステナイト・残留応力などの予想し得る因子、ないしはこれまで誰も気がつかなかった影響因子を特定し、浸炭材の真の疲労破壊の機構や起源を解明する。
実験:
本研究に用いた試料は、JIS SCr420の浸炭層を模擬した0.6%の炭素を含む合金である。この素材に調質を施し、Fig. 1の試験片に加工した。また、Fig. 1に示した試験片平衡部(赤破線の部分)をX線CTにより撮像した。
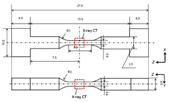
Fig. 1 試験片形状
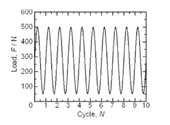
Fig. 2 疲労負荷サイクル
BL20XUの第二実験ハッチに回転ステージおよびその場観察用の材料試験機[1]を設置し、疲労試験を行いながらX線CT撮像を行った。疲労試験はFig. 2に示すように、応力比がR=0.1となるよう最大負荷荷重を500 N、最小負荷荷重50 Nのサイン波形で繰返し負荷した。疲労試験の負荷速度は1〜5 Hzの範囲で行った。CT撮像はX線透過像でき裂が確認できた後に、400 Nの引張荷重を負荷した状態で行った。
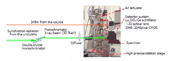
Fig. 3 X線CT撮像のセットアップ
X線CT撮像のセットアップをFig. 3に示す。二結晶モノクロメータで37.7 keVに単色化されたX線を用いた。BL20XUの第二実験ハッチは光源から245 mのところにある。光源から80 mのところにある第一実験ハッチに拡散板を設置して均一な照明とし、試料と検出器との距離を65 mmとなるところで屈折コントラストを効かせて透過像の撮像を行った。検出器は、Lu2SiO5(Ce)シンチレータ、20倍の光学レンズおよび2048×2048画素のCMOSカメラで構成される。露光時間は600 msとし、試料を180°回転させながら1800枚の透過像を撮像した。透過像はConvolution back projection法[2]により三次元のスライス画像セットに再構成した。画像は、市販のボリュームレンダリングソフトウェアを用いて三次元像とし、き裂の部分をセグメント化して、き裂形状を三次元表示した。
結果および考察:
試験片に繰返し負荷をかけたところ、き裂は2000 cycleから2100 cycleの間で発生した。そして、試験片は2200 cycleでX線CT撮像後の応力負荷の途中で破断した。2100 cycleで観察された77×41 μm2程度のき裂は、2200 cycleでは77×82 μm2程度までに成長している(Fig. 4のX線CT断層像)
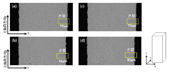
Fig. 4 2100 cycle、2200 cycleでの負荷軸を含むCT断層像; (a),(b) 2100 cycle, (c),(d) 2200 cycle
三次元ボリュームレンダリングソフトウェアで2000 cycleから2100 cycleにおいて試験片の平衡部に発生してFig. 4で確認できたき裂部分を抽出し負荷軸方向から表示した結果がFig. 5である。このき裂は、試験片の角部に生じて、2100 cycleから2200 cycleの間に、角部から概ねY軸方向にき裂が進展したことが分かる。
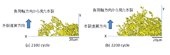
Fig. 5 負荷軸(Z)方向から見た試験片の角部のき裂の三次元画像; (a) 2100 cycle, (b) 2200 cycle
しかしながら、Fig. 6のSEM(走査型電子顕微鏡)による破面観察の結果から、(a)の黄色破線で囲まれた箇所の拡大である(c)で起点が確認できるように、破壊に至るき裂は(c)右の平面部から発生したものであり、2200 cycleのCT像で観察されていないことから、高硬度鋼の低い破壊靱性のために、撮像後の応力負荷により1サイクルで試料表面から発生したき裂が全体に拡大したことが分かる。なお、SEMでは上破面を見ているため、Fig. 5のCT像と上下反転して観察された角部のき裂は、(a)の黄色破線で囲まれた箇所の拡大である(b)の破面右上(赤破線で囲まれた箇所)に観察される。
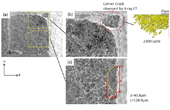
Fig. 6 破断後試験片の破面SEM像; (a)全体, (b)角部のき裂, (c)平行部のき裂
結言:
浸炭層を模擬した高硬度鋼材での疲労き裂の進展過程をSPring-8の放射光によるX線CTでその場観察し、高硬度鋼の疲労き裂の観察に成功した。また100サイクルで77×41 μm2から77×82 μm2に成長するき裂と1サイクルで試料全体に拡大するき裂の2種類が存在することが明らかになった。両者の違いが何に起因するものかは現時点において不明であり、両き裂の違いを発生位置(応力状態)・微細組織(結晶粒径・残留オーステナイト)などの観点から明らかにする予定である。
参考文献:
[1] 戸田裕之, 小林俊郎, 大垣智巳,材料試験技術, 48(2004), 5-10
[2] A. C. Kak and M. Slaney, Principles of Computerized Tomographic Imaging, Society of Industrial and Applied
Mathematics, (2001).
ⒸJASRI
(Received: February 21, 2014; Accepted: July 3, 2014; Published: July 10, 2014)